SHARE
MORE DETAIL
A Precise Control Method of Temperature and Pressure in Rayleigh-Brillouin Scattering Spectrometry
Abstract: For the Rayleigh-Brillouin scattering (RBS) spectroscopy experimental device, users proposed to reach high-precision control of temperature and pressure of measuring gas chamber. This article introduces a specific implementation, in which high-precision temperature control is implemented using semiconductor TEC modules and proportional control flow valve. Pressure control adopts a high-precision vacuum pressure control system, which includes a high-precision pressure sensor, a precision proportional control flow valve and a 24-bit acquisition precision PID controller. This temperature and pressure control scheme has been widely used and proven.
The introduced proportional flow control valve is introduced in https://www.genndih.com/proportional-flow-control-valve.htm
1. Technique requirement
According to customer requirements, temperature and pressure in Rayleigh-Brillouin scattering (RBS) spectroscopy as shown in Figure 1(the content of the red box area) for precise control, the specific requirements are as follows:
(1) Temperature range is 300K~318K; temperature control accuracy is ±0.02K.
(2) Pressure range is 30kPa~90kPa (absolute pressure); pressure control accuracy is ±0.1kPa; atmosphere is 99.9trogen.
2. Temperature control scheme
For high-precision temperature control near room temperature, it is proposed to use semiconductor heating and cooling technology shown in Figure 2 to reach, the specific contents include:
(1) Heating refrigerator: TEC module.
(2) Sensor: platinum resistance or thermistor temperature.
(3) PID controller: high-precision 24-bit temperature and pressure controller.
3. Pressure control scheme
The absolute pressure range required for experimental device to work is 30kPa~ 90kPa, and pressure within this range is required to be accurate and constant at any set point. Using KaoLu’s proportional control flow valve is the best choice.
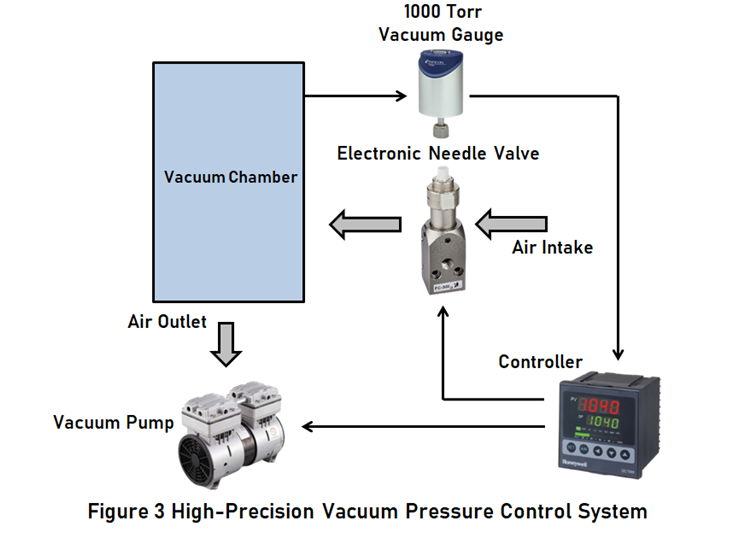
(1) Using a capacitance pressure gauge with a range of 1000torr for pressure measurement, its accuracy can reach ±0.2%. A vacuum pressure sensor with a higher accuracy of ±0.05% can also be used for measurement.
(2) The high-precision PID vacuum pressure controller with 24-bit A/D acquisition is used to match the measurement accuracy of high-precision vacuum pressure sensor and ensure control accuracy.
(3) Install a proportional flow control valve at air inlet and exhaust port of air chamber respectively. The proportional flow control valve is directly installed at air inlet.
https://www.genndih.com/proportional-flow-control-valve/mid-flow-proportional-valve-0-130L-min.html
(4) During the control process, the pumping speed is guaranteed to be constant after vacuum pump is turned on. First, you need to set the air intake electronic needle valve so that pressure and flow of intake port are constant, and then perform self-tuning of PID parameters. Last, realize precise control of air chamber pressure by automatically adjusting the flow rate of exhaust port.
Abstract: For the Rayleigh-Brillouin scattering (RBS) spectroscopy experimental device, users proposed to reach high-precision control of temperature and pressure of measuring gas chamber. This article introduces a specific implementation, in which high-precision temperature control is implemented using semiconductor TEC modules and proportional control flow valve. Pressure control adopts a high-precision vacuum pressure control system, which includes a high-precision pressure sensor, a precision proportional control flow valve and a 24-bit acquisition precision PID controller. This temperature and pressure control scheme has been widely used and proven.
The introduced proportional flow control valve is introduced in https://www.genndih.com/proportional-flow-control-valve.htm
1. Technique requirement
According to customer requirements, temperature and pressure in Rayleigh-Brillouin scattering (RBS) spectroscopy as shown in Figure 1(the content of the red box area) for precise control, the specific requirements are as follows:
(1) Temperature range is 300K~318K; temperature control accuracy is ±0.02K.
(2) Pressure range is 30kPa~90kPa (absolute pressure); pressure control accuracy is ±0.1kPa; atmosphere is 99.9trogen.
2. Temperature control scheme
For high-precision temperature control near room temperature, it is proposed to use semiconductor heating and cooling technology shown in Figure 2 to reach, the specific contents include:
(1) Heating refrigerator: TEC module.
(2) Sensor: platinum resistance or thermistor temperature.
(3) PID controller: high-precision 24-bit temperature and pressure controller.
3. Pressure control scheme
The absolute pressure range required for experimental device to work is 30kPa~ 90kPa, and pressure within this range is required to be accurate and constant at any set point. Using KaoLu’s proportional control flow valve is the best choice.
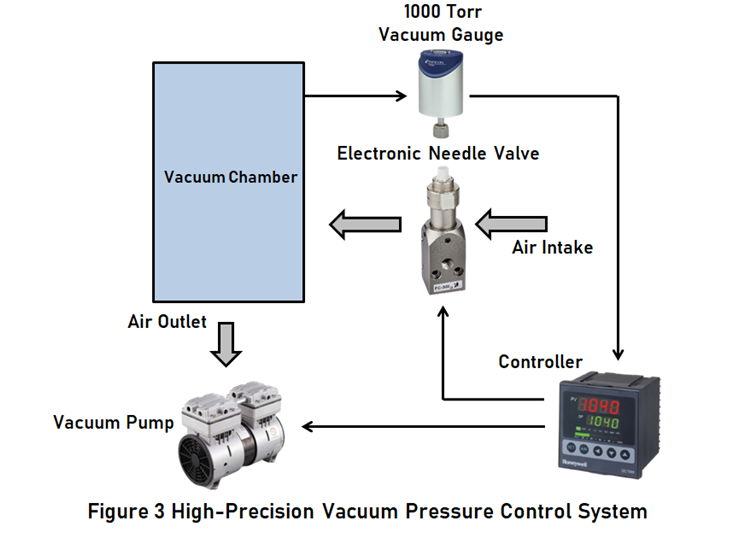
(1) Using a capacitance pressure gauge with a range of 1000torr for pressure measurement, its accuracy can reach ±0.2%. A vacuum pressure sensor with a higher accuracy of ±0.05% can also be used for measurement.
(2) The high-precision PID vacuum pressure controller with 24-bit A/D acquisition is used to match the measurement accuracy of high-precision vacuum pressure sensor and ensure control accuracy.
(3) Install a proportional flow control valve at air inlet and exhaust port of air chamber respectively. The proportional flow control valve is directly installed at air inlet.
https://www.genndih.com/proportional-flow-control-valve/mid-flow-proportional-valve-0-130L-min.html
(4) During the control process, the pumping speed is guaranteed to be constant after vacuum pump is turned on. First, you need to set the air intake electronic needle valve so that pressure and flow of intake port are constant, and then perform self-tuning of PID parameters. Last, realize precise control of air chamber pressure by automatically adjusting the flow rate of exhaust port.