SHARE
MORE DETAIL
Abstract: In order to meet the requirements of precise control of vacuum degree in low-pressure carburizing process (vacuum carburizing), corresponding solutions are proposed in this article, including adding a gas mixing tank for permeate gas mixing, using upstream and downstream dynamic vacuum level control methods and vacuum degree by coordinating the control method with the temperature, the rapid and precise control of the vacuum degree and temperature in the infiltration process can be reached.
1. Question
Low-pressure carburizing, also known as vacuum carburizing, is a process in which a carburizing medium is passed into a high-temperature furnace for rapid carburizing under a low-pressure vacuum state. The vacuum carburizing process can be divided into one-stage type, pulse type and swing type. Among them, the degree of vacuum, temperature and carburizing time will change according to the specific requirement, especially the degree of vacuum will change drastically with the temperature change. Therefore, in the vacuum carburizing process, the following problems need to be solved in terms of vacuum degree control:
(1) The problem of fast and accurate control of vacuum degree, such as fixed-point control, program control and fast pulse control, requires the vacuum control system to have high response speed and control accuracy. Especially to achieve precise control in the full range of vacuum, it is necessary to use different vacuum sensors and corresponding upstream and downstream control modes according to different ranges.
(2) Simultaneous control problem of vacuum degree and temperature. The carburizing is carried out in a high temperature environment, requiring simultaneous control of vacuum degree and temperature.
In order to meet the requirements of precise control of vacuum degree in low-pressure carburizing process, this article focuses on a solution for precise control of vacuum degree, and adopts dual-channel PID control to reach synchronous temperature control.
2. Solution
The overall structure of the vacuum degree and temperature control system in the low pressure carburizing process is shown in Figure 1.
The basic principle of precise control of vacuum degree is the dynamic control method, that is, according to the control set value and the measured value of vacuum gauge, the air intake flow and exhaust flow of the carburizing chamber are adjusted respectively, so that the flow in and out can reach a dynamic balance. If automatic control is required, PID control algorithms and corresponding controllers are required.
As shown in Figure 1, the precision control solution for vacuum degree proposed in this article adopts a dynamic control method, using an electronic needle valve to adjust the air intake flow, using an electronic ball valve or an electronic needle valve to adjust the exhaust flow, and the vacuum pump is used as a vacuum source. The automatic control of vacuum degree adopts PID controller.
For different low pressure carburizing processes, the control range of the vacuum degree is 1Pa~100kPa. Therefore, in the specific process, different dynamic control modes need to be adopted for the control in different vacuum degree ranges. For the vacuum degree control in the high vacuum range of 1Pa~1kPa, the upstream control mode of fixed exhaust flow and adjustable intake flow is adopted; for the vacuum degree control in the low vacuum range of 1kPa~100kPa, fixed intake flow and adjustable exhaust downstream control mode of the flow.
As shown in Figure 1, in order to reach the adjustment and control of air intake flow, a gas mixing tank is added to the intake end of carburizing chamber, and a gas mass flow meter is used to distribute various permeated gases into the gas mixing tank. The gas flows through the electronic needle valve for flow regulation and control.
In order to reach the temperature control function at the same time, this scheme adopts a dual-channel PID controller, one channel is used to control the vacuum degree, and the other channel is used to control the temperature. This PID control has 24-bit A/D and 16-bit D/A, with 47 input signal forms (thermocouple, thermal resistance, DC voltage), and can be connected to various vacuum and temperature sensors for measurement, display and control of 2 independent measurement control channels, two-wire RS485, standard MODBUS RTU communication protocol.
In order to reach high-precision adjustment in the vacuum degree control process, an electronic needle valve with fine adjustment by a numerically controlled stepping motor is used, as shown in Figure 2. The hysteresis of FC series of needle valves is much smaller than that of solenoid valves, and has a high-speed response within 1 second, especially the use of fluorine rubber (FKM) sealing technology, which makes the valve have superior corrosion resistance. Equipped with a stepper motor drive circuit module with the numerical control electronic needle valve, it provides the required power supply (24VDC) and control signal (0~10VDC) for the numerical control needle valve, and can also provide direct control of RS485 serial communication.
In conclusion, through the solution described in this article, the vacuum degree control accuracy in the low pressure carburizing process can reach 1% in the full scale range, and the corresponding temperature control can also be carried out.
1. Question
Low-pressure carburizing, also known as vacuum carburizing, is a process in which a carburizing medium is passed into a high-temperature furnace for rapid carburizing under a low-pressure vacuum state. The vacuum carburizing process can be divided into one-stage type, pulse type and swing type. Among them, the degree of vacuum, temperature and carburizing time will change according to the specific requirement, especially the degree of vacuum will change drastically with the temperature change. Therefore, in the vacuum carburizing process, the following problems need to be solved in terms of vacuum degree control:
(1) The problem of fast and accurate control of vacuum degree, such as fixed-point control, program control and fast pulse control, requires the vacuum control system to have high response speed and control accuracy. Especially to achieve precise control in the full range of vacuum, it is necessary to use different vacuum sensors and corresponding upstream and downstream control modes according to different ranges.
(2) Simultaneous control problem of vacuum degree and temperature. The carburizing is carried out in a high temperature environment, requiring simultaneous control of vacuum degree and temperature.
In order to meet the requirements of precise control of vacuum degree in low-pressure carburizing process, this article focuses on a solution for precise control of vacuum degree, and adopts dual-channel PID control to reach synchronous temperature control.
2. Solution
The overall structure of the vacuum degree and temperature control system in the low pressure carburizing process is shown in Figure 1.
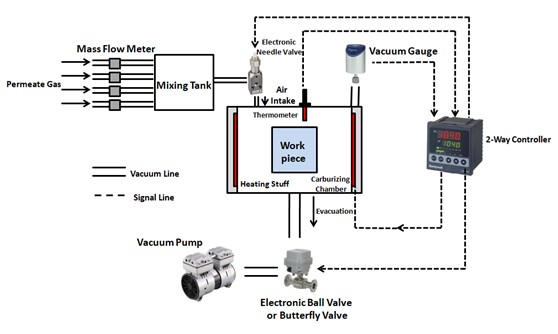
Figure 1 Schematic diagram of the structure of vacuum degree and temperature control system in low pressure carburizing process
The basic principle of precise control of vacuum degree is the dynamic control method, that is, according to the control set value and the measured value of vacuum gauge, the air intake flow and exhaust flow of the carburizing chamber are adjusted respectively, so that the flow in and out can reach a dynamic balance. If automatic control is required, PID control algorithms and corresponding controllers are required.
As shown in Figure 1, the precision control solution for vacuum degree proposed in this article adopts a dynamic control method, using an electronic needle valve to adjust the air intake flow, using an electronic ball valve or an electronic needle valve to adjust the exhaust flow, and the vacuum pump is used as a vacuum source. The automatic control of vacuum degree adopts PID controller.
For different low pressure carburizing processes, the control range of the vacuum degree is 1Pa~100kPa. Therefore, in the specific process, different dynamic control modes need to be adopted for the control in different vacuum degree ranges. For the vacuum degree control in the high vacuum range of 1Pa~1kPa, the upstream control mode of fixed exhaust flow and adjustable intake flow is adopted; for the vacuum degree control in the low vacuum range of 1kPa~100kPa, fixed intake flow and adjustable exhaust downstream control mode of the flow.
As shown in Figure 1, in order to reach the adjustment and control of air intake flow, a gas mixing tank is added to the intake end of carburizing chamber, and a gas mass flow meter is used to distribute various permeated gases into the gas mixing tank. The gas flows through the electronic needle valve for flow regulation and control.
In order to reach the temperature control function at the same time, this scheme adopts a dual-channel PID controller, one channel is used to control the vacuum degree, and the other channel is used to control the temperature. This PID control has 24-bit A/D and 16-bit D/A, with 47 input signal forms (thermocouple, thermal resistance, DC voltage), and can be connected to various vacuum and temperature sensors for measurement, display and control of 2 independent measurement control channels, two-wire RS485, standard MODBUS RTU communication protocol.
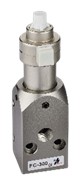
Figure 2 FC series electronic needle valve
In order to reach high-precision adjustment in the vacuum degree control process, an electronic needle valve with fine adjustment by a numerically controlled stepping motor is used, as shown in Figure 2. The hysteresis of FC series of needle valves is much smaller than that of solenoid valves, and has a high-speed response within 1 second, especially the use of fluorine rubber (FKM) sealing technology, which makes the valve have superior corrosion resistance. Equipped with a stepper motor drive circuit module with the numerical control electronic needle valve, it provides the required power supply (24VDC) and control signal (0~10VDC) for the numerical control needle valve, and can also provide direct control of RS485 serial communication.
In conclusion, through the solution described in this article, the vacuum degree control accuracy in the low pressure carburizing process can reach 1% in the full scale range, and the corresponding temperature control can also be carried out.