SHARE
MORE DETAIL
The function of bonding machine is to directly bond the flexible circuit board or cable to the electrodes on the edge of liquid crystal glass. That is, the process of installing flexible circuit boards and cables on liquid crystal glass. Therefore, the quality of bonding machine will directly affect the productivity of LCD glass and the service life of the LCD screen.
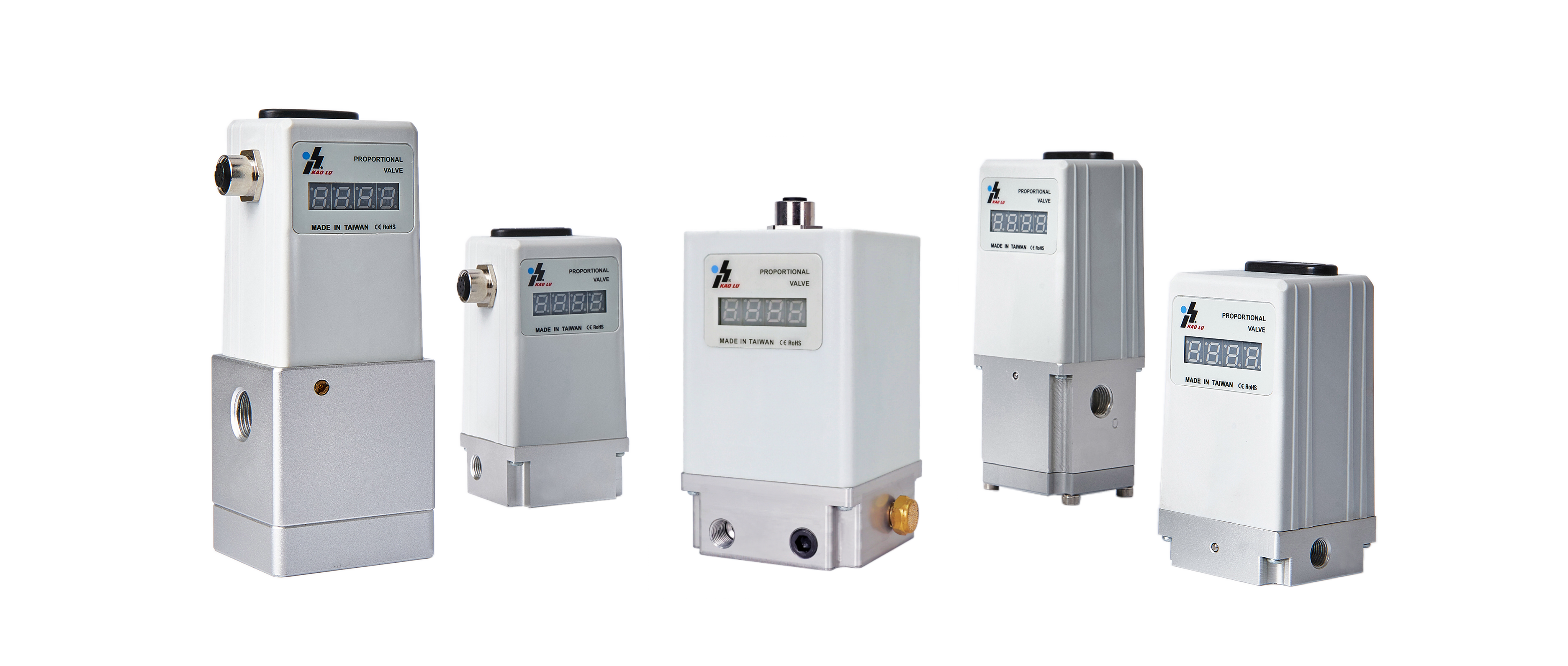
Technical parameters of bonding machine:
1. Air source pressure: 0.5~0.7MPa
2. Binding pressure: 3~40Kgf
3. Pressure accuracy: ±0.2Kgf
4. Binding temperature: RT~499℃
5. Hot pressure time: 1~99 S 6. Hot pressure accuracy: 0.14mm
The working process of bonding machine:
1. ACF pre-paste: Under the pressure and temperature by working requirement, the flexible circuit board (FPC) and the liquid crystal glass need to be bonded to the pins of ACF with a specified length, and the surface should be flat and free of air bubbles.
2. Pre-bonding: Align the pins of FPC and the liquid crystal glass through the CCD camera, and pre-press at the required pressure and temperature to form a preliminary connection. In this step, the alignment of CCD camera is an important link. As the pitch of lifting leads is getting smaller and smaller in production, the small pitch has reached 0.05MM, and the alignment accuracy should be within ±0.005mm.
3. Main bonding: Under the required pressure and temperature, the pre-bonded LCD screen is subjected to the main bonding by using a pulse hot press. At the same time, the glue in the ACF is polymerized and hardened at high temperature to form a strong physical connection between the two different materials.
Detection of bonding machine: The LCD screen after the main bonding is detected through CCD camera.
1. Temperature control: The heating rate and the maximum temperature are both important factors affecting the curing of ACF. The heating rate determines the surface quality of ACF after curing, and the maximum temperature determines the bonding strength of ACF after curing.
2. Flatness of the bonding head: The unevenness of the bonding head causes the ACF conductive particles to be unevenly broken, because the ACF conductive particles are very small, usually about 4um in diameter, and the ACF is very sensitive to pressure. When the contact surface of the bonding head is not flat, part of the ACF conductive particles will be completely broken, while another part of the ACF conductive particles will not be broken normally, resulting in poor electrical conductivity between the liquid crystal glass and the FPC.
Proportional pressure regulator control principle:
1. When the equipment is in standby, the solenoid valve controls the cylinder to rise, and the proportional valve is in the exhaust state.
2. When working, the solenoid valve controls the cylinder to descend, and the proportional valve controls the pressure when the cylinder descends. The proportional valve can be adjusted in real time according to the bonding process. If you have any needs or questions, please subscribe to our YouTube channel or contact us to learn more about proportional pressure regulator.
https://www.genndih.com
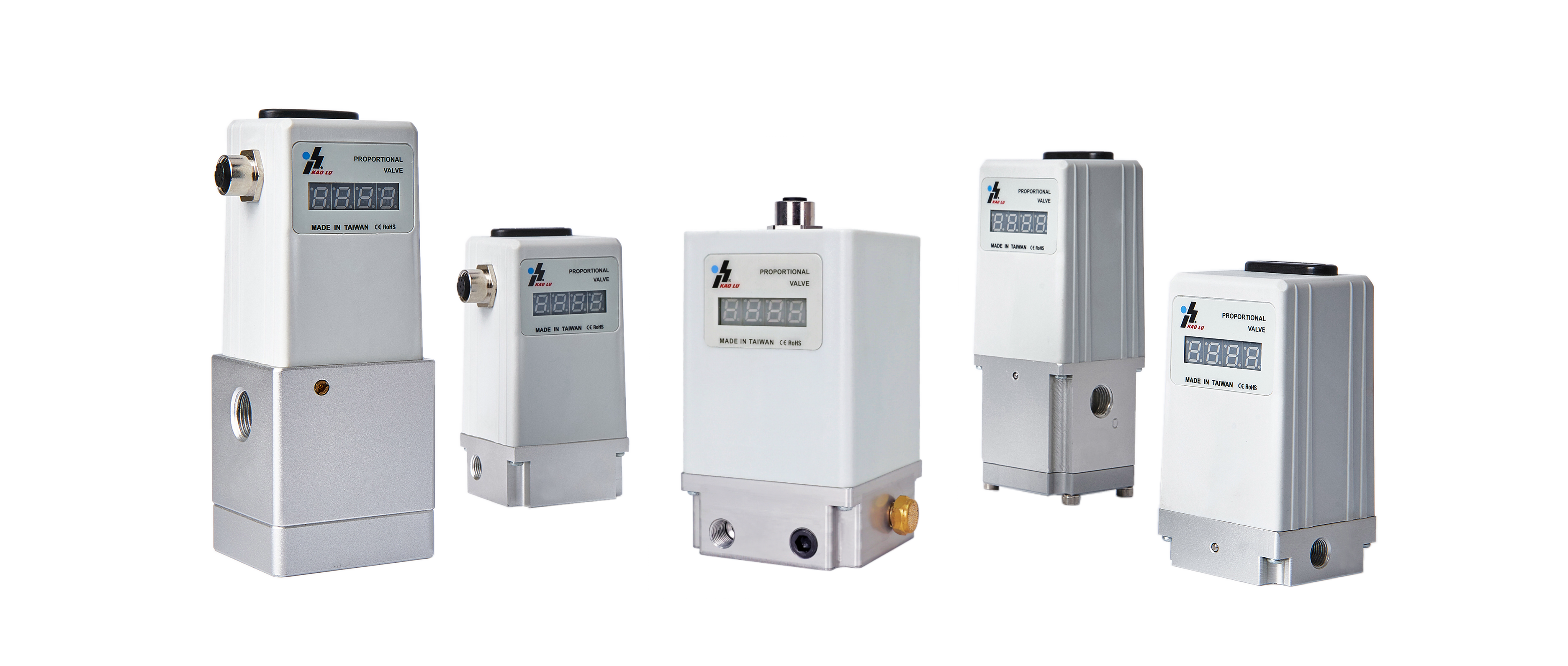
Technical parameters of bonding machine:
1. Air source pressure: 0.5~0.7MPa
2. Binding pressure: 3~40Kgf
3. Pressure accuracy: ±0.2Kgf
4. Binding temperature: RT~499℃
5. Hot pressure time: 1~99 S 6. Hot pressure accuracy: 0.14mm
The working process of bonding machine:
1. ACF pre-paste: Under the pressure and temperature by working requirement, the flexible circuit board (FPC) and the liquid crystal glass need to be bonded to the pins of ACF with a specified length, and the surface should be flat and free of air bubbles.
2. Pre-bonding: Align the pins of FPC and the liquid crystal glass through the CCD camera, and pre-press at the required pressure and temperature to form a preliminary connection. In this step, the alignment of CCD camera is an important link. As the pitch of lifting leads is getting smaller and smaller in production, the small pitch has reached 0.05MM, and the alignment accuracy should be within ±0.005mm.
3. Main bonding: Under the required pressure and temperature, the pre-bonded LCD screen is subjected to the main bonding by using a pulse hot press. At the same time, the glue in the ACF is polymerized and hardened at high temperature to form a strong physical connection between the two different materials.
Detection of bonding machine: The LCD screen after the main bonding is detected through CCD camera.
1. Temperature control: The heating rate and the maximum temperature are both important factors affecting the curing of ACF. The heating rate determines the surface quality of ACF after curing, and the maximum temperature determines the bonding strength of ACF after curing.
2. Flatness of the bonding head: The unevenness of the bonding head causes the ACF conductive particles to be unevenly broken, because the ACF conductive particles are very small, usually about 4um in diameter, and the ACF is very sensitive to pressure. When the contact surface of the bonding head is not flat, part of the ACF conductive particles will be completely broken, while another part of the ACF conductive particles will not be broken normally, resulting in poor electrical conductivity between the liquid crystal glass and the FPC.
Proportional pressure regulator control principle:
1. When the equipment is in standby, the solenoid valve controls the cylinder to rise, and the proportional valve is in the exhaust state.
2. When working, the solenoid valve controls the cylinder to descend, and the proportional valve controls the pressure when the cylinder descends. The proportional valve can be adjusted in real time according to the bonding process. If you have any needs or questions, please subscribe to our YouTube channel or contact us to learn more about proportional pressure regulator.
https://www.genndih.com