SHARE
MORE DETAIL
1. What is Double-layer Glass Reactor?
The double-layer glass reactor is designed with double-layer glass. The inner layer can be put into the reaction solvent for stirring reaction, and the interlayer can be passed through different cold and heat sources (refrigerated liquid, hot water, or hot oil) for cyclic heating or cooling reaction.
In the airtight glass reactor under the set constant temperature conditions, the stirring reaction can be carried out under the condition of vacuum to slightly positive pressure according to requirements and the reflux and distillation of the reaction solution can be carried out. It is ideal manufacturing equipment for modern fine chemical factories, biopharmaceuticals, and new material synthesis.
The double-layer glass reactor is the same as other reactors. Vacuum pressure is an important control variable in the reaction process. Different reaction processes often require different vacuum (negative pressure) or pressure (positive pressure) values.
However, in the vast majority of glass-stirred tank reactors at present, there are still serious deficiencies in the accurate control of vacuum pressure, which are mainly reflected in the following aspects:
- There is no automatic control method and many of them only rely on the extraction of vacuum pumps and manual intervention, which can only improve the simple vacuum environment but cannot reach control.
- Some vacuum pressure controllers also adopt switch-type air intake control mode, the vacuum pressure fluctuates greatly, and often many of them cannot reach program control.
- The control method is single, and it is impossible to control the vacuum degree of the full range (1Pa~0.1MPa), and it can only be controlled in a certain range. In addition, most glass-stirred tank reactors do not have micro-positive pressure supply and control capabilities.
- Many reactors use butterfly valves or ball valves to control the pumping rate. For smaller glass reactors, the response speed of butterfly valves and ball valves is too slow to reach accurate control of vacuum pressure, especially when the temperature changes. This phenomenon is particularly evident in the reaction process.
- Similarly, a vacuum pump with adjustable speed is also used to control the vacuum degree of the reactor. Still, there is also the problem of slow response speed resulting in large fluctuations in vacuum pressure. In addition, only adjusting the pumping rate can only control the range of low vacuum (high pressure) close to one atmospheric pressure, and it is powerless to control the range of higher vacuum (low pressure).
- Many reactors have strict requirements for gas (or liquid) parts, requiring sanitary (or food-grade) valves, but most of the current electric control valves cannot meet this special requirement.
In order to solve the above-mentioned problems in the double-layer glass reactor, this article will show you a complete and mature solution, that is, to use KaoLu's Proportional Pressure Regulator and a high-precision dual-channel PID controller, combined with vacuum gauges of different ranges, reactor, vacuum pump, and the positive pressure air source constitutes a closed-loop control loop.
Through the two-way mode of simultaneous control of upstream and downstream (intake and exhaust), automatic programming control of the full range of vacuum and micro positive pressure can be reached, which can reach high control accuracy, and communicate with the host computer to reach central control.
2. Vacuum pressure (positive and negative pressure, high and low pressure) control method
Generally, we take a standard atmospheric pressure (absolute pressure of 1Bar or 750 Torr) as a reference point and stipulate that a pressure lower than the standard atmospheric pressure is a negative pressure or vacuum environment, and a pressure greater than the standard atmospheric pressure is a positive pressure (pressure) environment.
Then, the control of the air pressure working environment of the stirred reactor is a typical vacuum pressure (positive and negative pressure or high and low pressure) control problem.
A typical method of positive and negative pressure control is the dynamic balance method, the principle of which is shown in Figure 1.
The core principle of the dynamic balance method is that the air intake and outlet in the controlled pressure vessel reach a certain set balance. The black arrow line in Figure 1 represents the gas flow direction, and the red arrow line represents the transmission and direction of the electrical signal.
Among them, the high-pressure air source is used as a positive pressure source, and the vacuum pump provides a negative pressure source for pumping air. The process regulator collects the sensor signal and compares it with the set value to adjust the opening of the inlet and outlet valves simultaneously so that the inlet and outlet flow can reach the set value in a balanced state.
There are two main advantages of using the dynamic balance method in vacuum pressure control:
- The control range is vast and can reach continuous control from vacuum to positive pressure.
- It has high control precision in the full range. When controlling in the high vacuum (low pressure) range, the opening of the exhaust valve is fixed, and the opening of the intake valve is adjusted. When controlling in a low vacuum or slightly positive pressure range, the opening of the intake valve is fixed and the opening of the exhaust valve is adjusted.
.png)
3. Solution
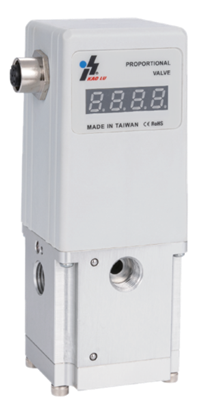
The vacuum pressure control device is mainly composed of a high-pressure air source, KaoLu's Vacuum Proportional Pressure Regulator, a vacuum pressure sensor, a PID process regulator, and a vacuum pump.
- High-pressure air source
The high-pressure gas source generally provides high-pressure gas greater than the set pressure for the micro-positive pressure control process. The gas source is generally a high-pressure gas cylinder and a high-pressure gas cylinder outputs gas at a fixed pressure through a pressure-reducing valve.
This fixed pressure needs to be slightly greater than the micro-positive pressure that needs to be controlled. If the reactor only needs to be controlled in the range of vacuum (negative pressure), there is no need for a high-pressure gas source, and the atmosphere can be used directly. - KaoLu's Vacuum Proportional Pressure Regulator
KaoLu's Vacuum Proportional Pressure Regulator is a fast-response electronic regulating valve, including an electric needle valve. KaoLu's Vacuum Proportional Pressure Regulator is suitable for small flow intake adjustment. For small-volume double-layer glass reactors, the inlet and outlet regulating valves can directly use electronically controlled needle valves, while for large-volume reactors, electronic needle valves are selected for the inlet valves.
The full opening time of KaoLu's Vacuum Proportional Pressure Regulator is 0.8s. The fast response time is one of the important factors to ensure control accuracy. - Vacuum pressure sensor
The sensor is the key to vacuum pressure measurement throughout the reaction process, and its measurement accuracy also determines the control accuracy of reactor temperature and vacuum pressure and the effectiveness of the process. It is generally recommended to use a high-precision capacitance vacuum gauge.
In the entire vacuum pressure range, two specifications of capacitance vacuum gauges (10Torr and 1000Torr) can basically cover the entire range from low pressure (vacuum) to slightly positive pressure (high pressure), and It can also guarantee the accuracy of measurement × 0.25% under any vacuum pressure. The signal output of the capacitance vacuum gauge corresponding to the measurement range is generally 0~10V DC voltage, and the output voltage has a linear relationship with the vacuum degree measurement value.
Some reactors use a Pirani gauge to measure in the vacuum range, but the measurement error of the Pirani gauge is relatively large, and the corresponding output voltage signal has a nonlinear relationship with the vacuum degree, so Pirani gauge is generally used for measurement and reactor vacuum pressure control does not require high control accuracy.
Special attention should be paid to the fact that the positive pressure measurement capability of the capacitance vacuum gauge is very limited, and the Pirani gauge cannot measure positive pressure. If positive pressure control is to be performed, a positive pressure sensor with corresponding accuracy is required. - PID process regulator
The process regulator is the key to reaching vacuum pressure control, and its acquisition accuracy and adjustment accuracy determine the final control accuracy of the vacuum pressure. This solution uses an ultra-high-precision dual-channel PID process regulator, in which two independent channels are used to adjust the inlet valve and the outlet valve respectively.
Each channel is configured with 24-bit AD, 16-bit DA, and double-precision floating-point operations, which can reach a minimum output percentage of 0.01%. This is the highest level of configuration for industrial PID regulators in the world. It is also the electronic regulating valve, which can easily reach a vacuum pressure control accuracy of better than ±1%.
The ultra-high-precision dual-channel PID process regulator has powerful functions. The PID parameters can be self-tuned, and multiple sets of PID parameters can be stored to meet the needs of different reaction processes. It also has a MODBUS standard communication protocol, and the control of multiple regulators can be reached through the host computer of central control. The computer software provided with the machine can perform remote settings, data acquisition, display, and storage of the PID controller, which greatly facilitates the debugging of the vacuum pressure control system.
4. Conclusion
In summary, the vacuum pressure accurate control solution proposed in this article can not only meet the needs of accurate control of vacuum pressure (positive and negative pressure) in double-layer glass reactors but also can be used in other various reactors and rotary skills that vacuum pressure control in.
The solution described in this article is a vacuum pressure control system with a discrete structure. The control system can also be integrated according to the needs and specific reactor design. The electronically controlled valve and PID regulator are integrated into an instrument, which is more convenient for the overall reactor of layout design and kitting.
For more information about KaoLu's Vacuum Proportional Pressure Regulator, please refer to our website.