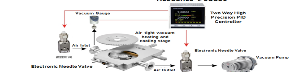
2022.03.15
Precise Control of Vacuum in Cold and Hot Stage
SHARE
MORE DETAIL
Precise Control of Vacuum in Cold and Hot Stage
Abstract: Focusing on current problems of poor vacuum control accuracy and high price of supporting control system in the airtight vacuum cooling and heating stage, this article introduces the solution using domestic products, and introduces the details of upstream and downstream bi-directional control mode using KaoLu’s FC series electronic needle valve implementation process. This solution has been applied and verified, which can reach precise control of vacuum degree in a wide range, and the fluctuation of vacuum degree can be controlled within ±1%. The whole control system has high cost performance.
1. Question
The airtight vacuum heating and cooling stage is a precision temperature-controlled heating and cooling stage that can be used in both vacuum and airtight environments. It has heating and cooling functions, and is suitable for applications such as microscopes and spectrometers to accurately heat or cool samples in a controlled vacuum environment. According to user requirements, for the current various airtight vacuum heating and cooling stage, in terms of vacuum degree control, the following problems need to be solved:
(1) Whether it is international or domestic vacuum heating and cooling stage, the vacuum measurement and control also use Pirani vacuum gauge, so that the matching control system cannot achieve precise control of vacuum, such as the accuracy of research and simulation freeze-drying process cannot meet requirement.
(2) The air-tight vacuum heating and cooling stage is generally small in size, and it has always been difficult to reach precise control within a wide range of vacuum degrees. The fluctuation of vacuum degree is large, and the fluctuation of vacuum degree in turn affects the temperature stability.
(3) The international vacuum degree control system not only fails to meet the requirements of control accuracy, but also is expensive. Focusing on the above problems existing in the air-tight vacuum heating and cooling table, this article will introduce a solution with domestic products and high cost performance, and introduce the detailed implementation process.
2. Solution
The overall structure of the vacuum degree precision control system of the airtight vacuum cooling and heating stage is shown in Figure 1. The whole system mainly includes a vacuum gauge, a numerical control needle valve, a PID controller and a vacuum pump. In order to improve the accuracy of vacuum measurement and control, a capacitive vacuum gauge with higher measurement accuracy (up to 0.2% of full scale) is used, which can cover the vacuum range of 0.01 to 760 Torr. If a higher vacuum environment is required, a Pirani vacuum gauge can also be used for measurement and control. In order to reach full-range vacuum control, two electronic needle valves are installed at the air inlet and outlet of hot and cold stage respectively. By adopting the upstream and downstream control modes respectively, precise control with a full-scale fluctuation rate of less than ±1% can be reached. The controller is the key to precise control. The high-precision PID controller of 24-bit A/D and 16-bit D/A is used in the scheme, and the independent dual-channel is convenient for upstream and downstream gas flow regulation and control. In conclusion, cost-effective precision control of KaoLu’s FC series electronic needle valve is possible with this proven vacuum control solution.
For further information, please visit https://www.genndih.com/proportional-flow-control-valve/miniature-proportional-valve-0-32L-min.html
Abstract: Focusing on current problems of poor vacuum control accuracy and high price of supporting control system in the airtight vacuum cooling and heating stage, this article introduces the solution using domestic products, and introduces the details of upstream and downstream bi-directional control mode using KaoLu’s FC series electronic needle valve implementation process. This solution has been applied and verified, which can reach precise control of vacuum degree in a wide range, and the fluctuation of vacuum degree can be controlled within ±1%. The whole control system has high cost performance.
1. Question
The airtight vacuum heating and cooling stage is a precision temperature-controlled heating and cooling stage that can be used in both vacuum and airtight environments. It has heating and cooling functions, and is suitable for applications such as microscopes and spectrometers to accurately heat or cool samples in a controlled vacuum environment. According to user requirements, for the current various airtight vacuum heating and cooling stage, in terms of vacuum degree control, the following problems need to be solved:
(1) Whether it is international or domestic vacuum heating and cooling stage, the vacuum measurement and control also use Pirani vacuum gauge, so that the matching control system cannot achieve precise control of vacuum, such as the accuracy of research and simulation freeze-drying process cannot meet requirement.
(2) The air-tight vacuum heating and cooling stage is generally small in size, and it has always been difficult to reach precise control within a wide range of vacuum degrees. The fluctuation of vacuum degree is large, and the fluctuation of vacuum degree in turn affects the temperature stability.
(3) The international vacuum degree control system not only fails to meet the requirements of control accuracy, but also is expensive. Focusing on the above problems existing in the air-tight vacuum heating and cooling table, this article will introduce a solution with domestic products and high cost performance, and introduce the detailed implementation process.
2. Solution
The overall structure of the vacuum degree precision control system of the airtight vacuum cooling and heating stage is shown in Figure 1. The whole system mainly includes a vacuum gauge, a numerical control needle valve, a PID controller and a vacuum pump. In order to improve the accuracy of vacuum measurement and control, a capacitive vacuum gauge with higher measurement accuracy (up to 0.2% of full scale) is used, which can cover the vacuum range of 0.01 to 760 Torr. If a higher vacuum environment is required, a Pirani vacuum gauge can also be used for measurement and control. In order to reach full-range vacuum control, two electronic needle valves are installed at the air inlet and outlet of hot and cold stage respectively. By adopting the upstream and downstream control modes respectively, precise control with a full-scale fluctuation rate of less than ±1% can be reached. The controller is the key to precise control. The high-precision PID controller of 24-bit A/D and 16-bit D/A is used in the scheme, and the independent dual-channel is convenient for upstream and downstream gas flow regulation and control. In conclusion, cost-effective precision control of KaoLu’s FC series electronic needle valve is possible with this proven vacuum control solution.
For further information, please visit https://www.genndih.com/proportional-flow-control-valve/miniature-proportional-valve-0-32L-min.html
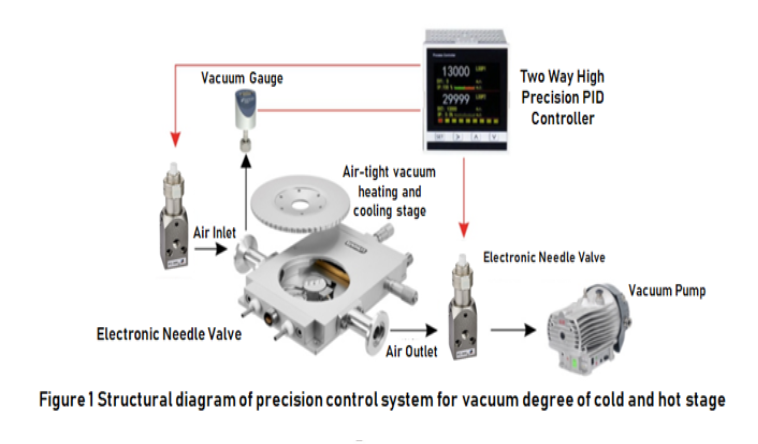