
2023.09.01
Solution of High Precision Liquid Helium Pressure Control in Low Temperature Superconducting Test System
SHARE
MORE DETAIL
1. Project Overview
Various superconducting components such as superconducting magnets and superconducting cavities need to be tested in a low-temperature superconducting test system before installation. In order to make the superconducting components reach a low-temperature environment, the tested components need to be immersed in liquid helium.
In the medium, a low-temperature Dewar is used to contain the liquid helium medium. During the entire test process, the requirements for the liquid helium pressure in the low-temperature test system are extremely high, that is, the helium pressure (absolute pressure) at the top of the Dewar is required to have excellent stability. Otherwise, the test will be unstable and the test results will be affected error.
At present, many existing low-temperature superconducting test systems have serious problems such as unstable liquid helium pressure control. Some customers have put forward corresponding technical upgrade requirements.
Two first and second pressure relief valves with different calibers are used to roughly adjust and finely adjust the pressure of liquid helium, but the pressure of liquid helium in this adjustment method can only be controlled at the range of 1.2~1.6Bar corresponds to the temperature change of liquid helium in the range of 4.39~4.74°C, resulting in a temperature fluctuation of 0.35°C.
At present, the customer proposes to try to control the temperature fluctuation within 0.1 ℃ or higher stability, so as to improve the performance test accuracy of superconducting components.
The low-temperature vertical test system for high-field superconducting magnets has a pressure control range of 1~1.3Bar. Although a liquid helium heater is used to change the liquid helium pressure in the system, due to the pressure control valve The precision of the adjustment is not enough, and finally the pressure control precision is far below the test requirements, and the customer also put forward the technical transformation requirements.
In view of the problem of insufficient liquid helium pressure control accuracy in the above two typical low-temperature superconducting test systems, this article will propose corresponding solutions. The solution will adopt two technical means of direct pressure control and flow control and supporting numerical control valves, combined with ultra-high-precision PID vacuum pressure controller and pressure sensor, which can greatly improve the pressure control accuracy of liquid helium, and ultimately reduce the low-temperature superconducting pressure. performance test error.
2. Solution
(1) Direct pressure regulation method
In the low-temperature superconducting test system, the factors that cause liquid helium to evaporate are not controllable. The test system can only be kept stable by adjusting the helium gas pressure above the liquid helium.
Therefore, in order to achieve pressure control above liquid helium, the solution uses a direct pressure regulation method, that is, a numerically controlled pressure control valve is used to replace the first and second pressure relief valves. This pressure control valve, high-precision PID controller and pressure sensor form a closed-loop control loop to achieve automatic pressure relief and high-precision pressure control.
KaoLu’s Proportional Pressure Regulator is a positive pressure and pressure reducing control valve, which can exactly meet the micro-positive pressure control needs of low-temperature superconducting testing systems. The driving pressure provided by the helium source and the pressure reducing valve enables high-precision pressure control at the control valve outlet while also maintaining very small gas leakage to save helium.
In addition, KaoLu’s Proportional Pressure Regulator has high control accuracy, and can combine with a high-precision pressure sensor and a PID vacuum pressure controller. It can control the liquid helium pressure at a high-precision level of 0.1%.
(2) Flow regulation method
In the low-temperature and ultra-low test system, one of the differences is that it has a liquid helium heater. That is, the control loop composed of the liquid helium heater and the pressure control valve can control different liquid helium pressures. This enables control of different liquid helium temperatures. In order to reach precise control of different liquid helium pressures, the solution here uses a flow regulation method.
KaoLu’s Proportional Pressure Regulator, a dual-channel high-precision PID controller, a pressure sensor and a liquid helium heater form a closed-loop control loop, which can be configured as desired. Fixed value for high-precision pressure control. The electric needle valve is a numerically controlled micro-flow regulating valve that can automatically adjust the needle valve opening through a PID pressure controller, and the outflowing helium can be directed to the helium recovery air bag.
KaoLu’s Proportional Pressure Regulator also has high control accuracy and combined with high-precision pressure sensor and PID vacuum pressure controller. It can also control the pressure of liquid helium at a high-precision level of 0.1%.
3.Conclusion
Through the technical means of the above solution, the accurate control of the liquid helium pressure in the low-temperature ultra-low test system can be reached, and the control accuracy can reach up to ±0.1%. Calculated based on absolute pressure, when the saturated vapor pressure is 1.2Bar, the temperature of liquid helium is 4.4K.
Therefore, if the pressure control accuracy is ±0.1%, the fluctuation range of liquid helium pressure is ±1.2mBar (equivalent to the absolute pressure ±120Pa), and the corresponding liquid helium temperature fluctuation range is 4.4mK, that is, the controlled liquid helium temperature is 4.4±0.0044K.
It can be seen that through the solution described in this article, only by adopting industrial-level low-cost PID vacuum pressure controllers and pressure sensors, combined with numerically controlled pressure control valves and KaoLu’s Proportional Pressure Regulator, high-precision liquid helium pressure can be reached. The temperature control accuracy can reach the mK level, which can fully meet the needs of most low-temperature superconducting test systems.
More information about KaoLu’s Proportional Pressure Regulator, please visit our website!
Various superconducting components such as superconducting magnets and superconducting cavities need to be tested in a low-temperature superconducting test system before installation. In order to make the superconducting components reach a low-temperature environment, the tested components need to be immersed in liquid helium.
In the medium, a low-temperature Dewar is used to contain the liquid helium medium. During the entire test process, the requirements for the liquid helium pressure in the low-temperature test system are extremely high, that is, the helium pressure (absolute pressure) at the top of the Dewar is required to have excellent stability. Otherwise, the test will be unstable and the test results will be affected error.
At present, many existing low-temperature superconducting test systems have serious problems such as unstable liquid helium pressure control. Some customers have put forward corresponding technical upgrade requirements.
Two first and second pressure relief valves with different calibers are used to roughly adjust and finely adjust the pressure of liquid helium, but the pressure of liquid helium in this adjustment method can only be controlled at the range of 1.2~1.6Bar corresponds to the temperature change of liquid helium in the range of 4.39~4.74°C, resulting in a temperature fluctuation of 0.35°C.
At present, the customer proposes to try to control the temperature fluctuation within 0.1 ℃ or higher stability, so as to improve the performance test accuracy of superconducting components.
The low-temperature vertical test system for high-field superconducting magnets has a pressure control range of 1~1.3Bar. Although a liquid helium heater is used to change the liquid helium pressure in the system, due to the pressure control valve The precision of the adjustment is not enough, and finally the pressure control precision is far below the test requirements, and the customer also put forward the technical transformation requirements.
In view of the problem of insufficient liquid helium pressure control accuracy in the above two typical low-temperature superconducting test systems, this article will propose corresponding solutions. The solution will adopt two technical means of direct pressure control and flow control and supporting numerical control valves, combined with ultra-high-precision PID vacuum pressure controller and pressure sensor, which can greatly improve the pressure control accuracy of liquid helium, and ultimately reduce the low-temperature superconducting pressure. performance test error.
2. Solution
(1) Direct pressure regulation method
In the low-temperature superconducting test system, the factors that cause liquid helium to evaporate are not controllable. The test system can only be kept stable by adjusting the helium gas pressure above the liquid helium.
Therefore, in order to achieve pressure control above liquid helium, the solution uses a direct pressure regulation method, that is, a numerically controlled pressure control valve is used to replace the first and second pressure relief valves. This pressure control valve, high-precision PID controller and pressure sensor form a closed-loop control loop to achieve automatic pressure relief and high-precision pressure control.
KaoLu’s Proportional Pressure Regulator is a positive pressure and pressure reducing control valve, which can exactly meet the micro-positive pressure control needs of low-temperature superconducting testing systems. The driving pressure provided by the helium source and the pressure reducing valve enables high-precision pressure control at the control valve outlet while also maintaining very small gas leakage to save helium.
In addition, KaoLu’s Proportional Pressure Regulator has high control accuracy, and can combine with a high-precision pressure sensor and a PID vacuum pressure controller. It can control the liquid helium pressure at a high-precision level of 0.1%.
(2) Flow regulation method
In the low-temperature and ultra-low test system, one of the differences is that it has a liquid helium heater. That is, the control loop composed of the liquid helium heater and the pressure control valve can control different liquid helium pressures. This enables control of different liquid helium temperatures. In order to reach precise control of different liquid helium pressures, the solution here uses a flow regulation method.
KaoLu’s Proportional Pressure Regulator, a dual-channel high-precision PID controller, a pressure sensor and a liquid helium heater form a closed-loop control loop, which can be configured as desired. Fixed value for high-precision pressure control. The electric needle valve is a numerically controlled micro-flow regulating valve that can automatically adjust the needle valve opening through a PID pressure controller, and the outflowing helium can be directed to the helium recovery air bag.
KaoLu’s Proportional Pressure Regulator also has high control accuracy and combined with high-precision pressure sensor and PID vacuum pressure controller. It can also control the pressure of liquid helium at a high-precision level of 0.1%.
3.Conclusion
Through the technical means of the above solution, the accurate control of the liquid helium pressure in the low-temperature ultra-low test system can be reached, and the control accuracy can reach up to ±0.1%. Calculated based on absolute pressure, when the saturated vapor pressure is 1.2Bar, the temperature of liquid helium is 4.4K.
Therefore, if the pressure control accuracy is ±0.1%, the fluctuation range of liquid helium pressure is ±1.2mBar (equivalent to the absolute pressure ±120Pa), and the corresponding liquid helium temperature fluctuation range is 4.4mK, that is, the controlled liquid helium temperature is 4.4±0.0044K.
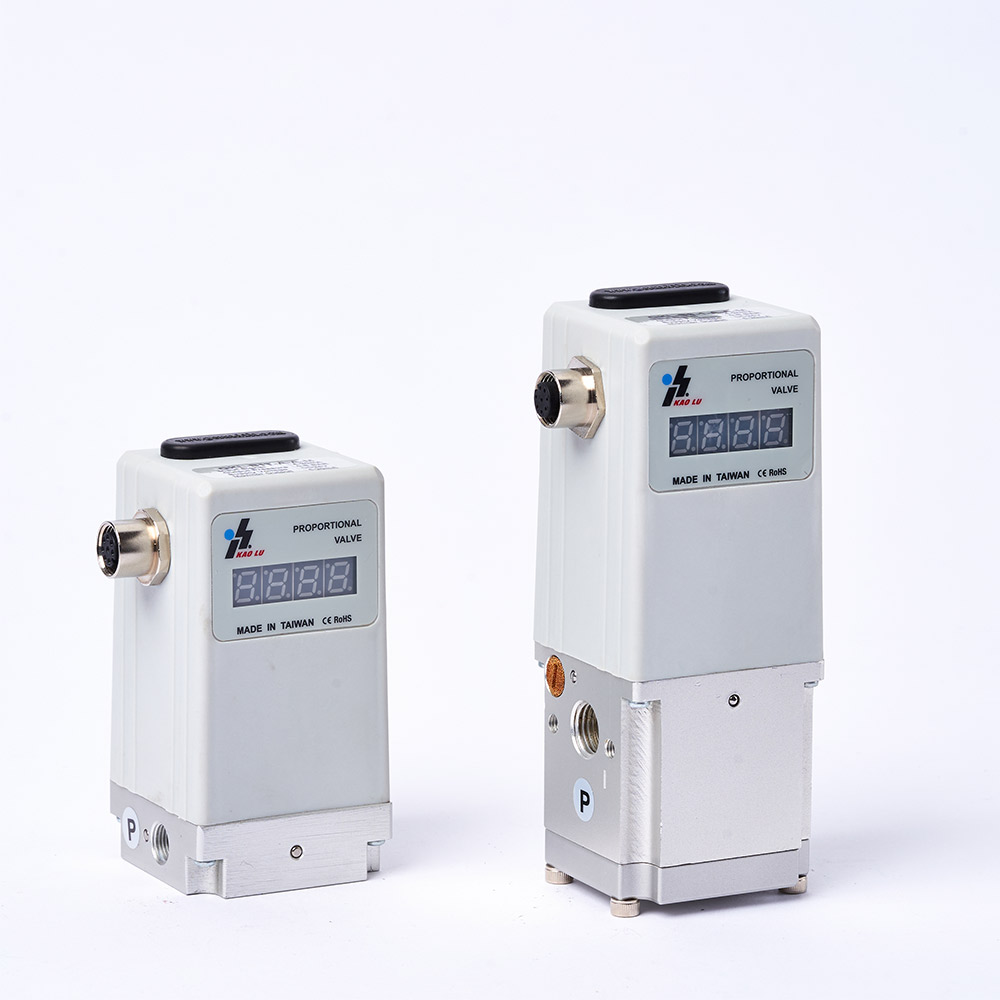
It can be seen that through the solution described in this article, only by adopting industrial-level low-cost PID vacuum pressure controllers and pressure sensors, combined with numerically controlled pressure control valves and KaoLu’s Proportional Pressure Regulator, high-precision liquid helium pressure can be reached. The temperature control accuracy can reach the mK level, which can fully meet the needs of most low-temperature superconducting test systems.
More information about KaoLu’s Proportional Pressure Regulator, please visit our website!