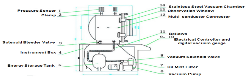
2022.03.14
Upgrade of Pressure Control System of Low-Pressure Environment Simulation Cabin for Radiosonde Verification
SHARE
MORE DETAIL
Upgrade of Pressure Control System of Low-Pressure Environment Simulation Cabin for Radiosonde Verification
Abstract: Focusing on problem of poor control accuracy and stability of pressure control system of low-pressure environment simulation chamber used for radiosonde verification, and inaccurate configuration of pressure sensors and control systems. Users proposed upgrading and transformation requirements. This article introduces the implementation scheme of a new generation of low-pressure environment simulation chamber pressure control system, adopts a two-way control mode, and conducts a scheme verification test. The test results show that the control accuracy and stability are greatly improved.
1. Question
One of the important methods of calibrating radiosonde is to test low-pressure environment simulation cabin on the ground. The structure of low-pressure environment simulation cabin in use is shown in Figure 1.
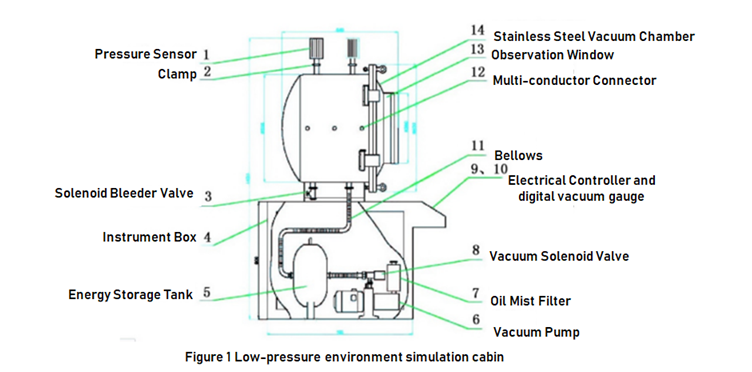
There is a problem that the pressure control fluctuates greatly during the use of this low-pressure environment simulation chamber. The closer the pressure is to 1 atmosphere, the greater the fluctuation. The analysis believes that it is mainly caused by the following reasons:
(1) The selection of pressure sensor is inaccurate. Proportion of the sensor error in the full-scale pressure range is not the same, which shows that the fluctuation is large when it is close to 1 atmosphere and the fluctuation is small when it is far away from 1 atmosphere. In real world, all problems exist. Large fluctuations, but the pressure sensor has the highest accuracy near 1 atmospheric pressure, and the pressure sensor error has completely covered the pressure fluctuation range at a distance away from 1 atmosphere pressure. In fact, there are large fluctuations as a whole, but the pressure sensor has the highest accuracy near 1 atmosphere pressure, and the error of pressure sensor has completely covered pressure fluctuation range at a distance away from 1 atmosphere pressure.
(2) Pressure control adopts switch control mode. Vacuum pump and solenoid valve are opened or closed at the same time according to pressure setting value. Although gas storage tank is added as a buffer, it is difficult to achieve accurate and constant pressure in this semi-automatic control mode.
(3) Controller does not use the PID automatic control method which is also the main reason for affecting pressure control accuracy. Based on the above analysis, focusing on the problems of poor control accuracy and stability of pressure control system with low-pressure environment simulation chamber used for calibration of the previous generation sound, and an inaccurate configuration of the pressure sensor and control system. Users proposed upgrading and transformation requirements. This article will introduce implementation scheme of the new generation with low-pressure environment simulation chamber pressure control system. Bi-directional control mode is proposed to be adopted, and the scheme verification test will be carried out, which proves that control accuracy and stability can be greatly improved.
2. Upgrading and reforming pressure control system using FC series electric needle valve The absolute pressure range of the low-pressure environment simulation chamber for sonde verification is 1torr~760torr.It is required that pressure of simulation chamber can be accurately and constant at any set point within this range, and it can even be controlled according to the set pressure transformation rate. For this reason, the specific upgrade scheme is to keep vacuum pump and vacuum solenoid valve on the basis of original pressure control system, replace pressure sensor and controller, remove energy storage tank, and increase numerically controlled air intake valve and exhaust valve. The specific scheme is as follows:
(1) Capacitance pressure gauge with 10torr and 1000torrare used to cover measurement of the entire low pressure range, thereby ensuring measurement accuracy of the full range.
(2) High-precision PID vacuum pressure controller is used to match measurement accuracy of capacitive pressure gauge and ensure control accuracy.
(3) Install an electric needle valve at air inlet and exhaust port of vacuum chamber respectively. The electric needle valve is directly installed at air inlet.
(4) The control mode adopts upstream mode and downstream mode respectively. Upstream mode is used to control air pressure below 10torr, and downstream mode is used to control air pressure in the range of 10~760torr using KaoLu electric needle valve (https://www.genndih.com/proportional-flow-control-valve.htm)
(5) As shown in Figure 2, upstream mode is to maintain upstream pressure and outlet flow constant, and control chamber pressure by adjusting inlet flow.
(6) As shown in Figure 3, downstream mode is to maintain upstream pressure and inlet flow constant, and control chamber pressure by adjusting exhaust flow.
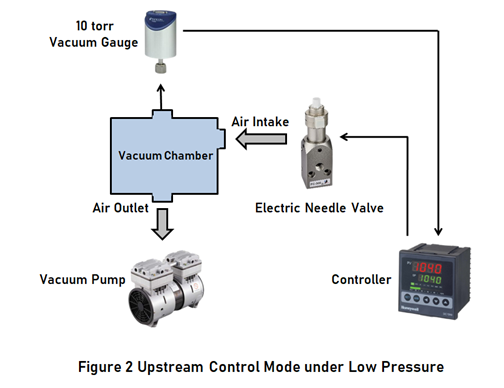
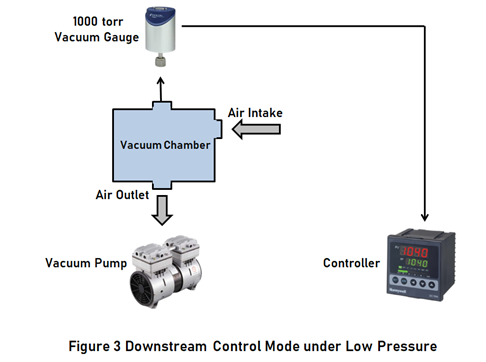
3. Certification test of scheme
For the above two control modes, two capacitive pressure gauges of 1torr and 1000torr, an electric needle valve and a 24-bit high-precision pressure controller were used to conduct the assessment test. The internal space of vacuum chamber used for test was 400×400× 500mm; the test device is shown in Figure 4 and Figure 5.
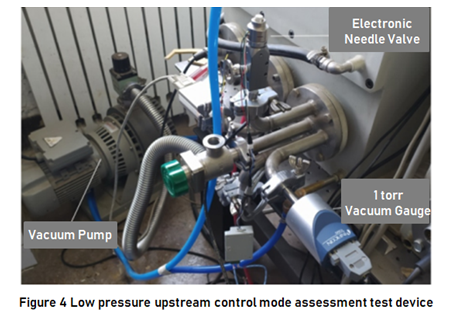
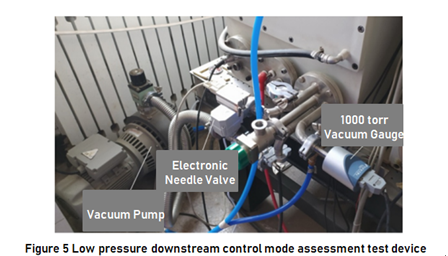
During the upstream mode test, vacuum pump was first turned on and then pumped at full speed. Then the PID parameters of controller were self-tuned at about 68Pa. After the auto-tuning is completed, 8 set points of 12, 27, 40, 53, 67, 80, 93 and 107Pa are controlled respectively. The air pressure changes during the whole control process are shown in Figure 6. During the downstream mode test, vacuum pump was first turned on and then pumped at full speed, and air intake electric needle valve was adjusted to the position of micro intake. Then the PID parameters of controller were self-tuned at about 300torr. After the auto-tuning is completed, 5 set points of 70, 200, 300, 450 and 600 Torr are controlled respectively. The air pressure changes during the whole control process are shown in Figure 7.
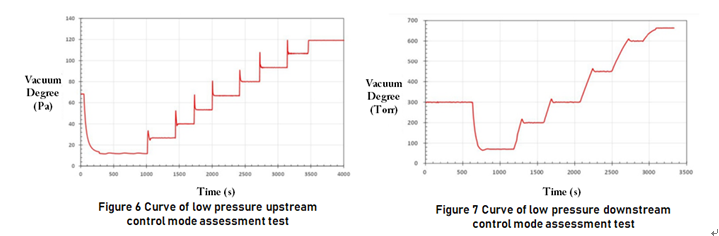
By expressing the above control effects at different low pressure constant points as fluctuation rate, fluctuation rate distribution in the entire range shown in Figures 8 and 9 is obtained. It can be seen from fluctuation rate distribution diagram that fluctuation rate can be accurately controlled within the range of ±1% in the whole range of low pressure. The large fluctuation at 12Pa is because the PID parameters obtained by self-tuning at 68Pa are invalid, and a separate PID parameter self-tuning is required.
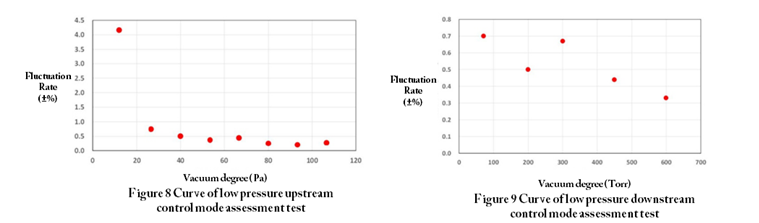
It can be seen from the above test results that the electric needle valve can improve the pressure control accuracy and stability by more than five times, and greatly improve the automation level and reliability of the low-pressure environment simulation chamber. For further information on the introduced electric needle valve, please visit https://www.genndih.com/proportional-flow-control-valve/miniature-proportional-valve-0-32L-min.html
Abstract: Focusing on problem of poor control accuracy and stability of pressure control system of low-pressure environment simulation chamber used for radiosonde verification, and inaccurate configuration of pressure sensors and control systems. Users proposed upgrading and transformation requirements. This article introduces the implementation scheme of a new generation of low-pressure environment simulation chamber pressure control system, adopts a two-way control mode, and conducts a scheme verification test. The test results show that the control accuracy and stability are greatly improved.
1. Question
One of the important methods of calibrating radiosonde is to test low-pressure environment simulation cabin on the ground. The structure of low-pressure environment simulation cabin in use is shown in Figure 1.
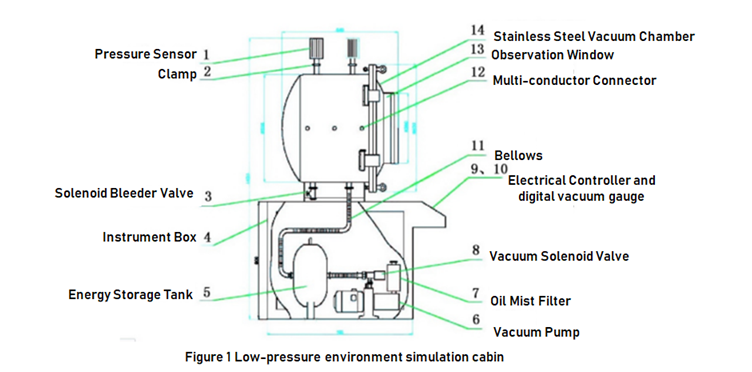
There is a problem that the pressure control fluctuates greatly during the use of this low-pressure environment simulation chamber. The closer the pressure is to 1 atmosphere, the greater the fluctuation. The analysis believes that it is mainly caused by the following reasons:
(1) The selection of pressure sensor is inaccurate. Proportion of the sensor error in the full-scale pressure range is not the same, which shows that the fluctuation is large when it is close to 1 atmosphere and the fluctuation is small when it is far away from 1 atmosphere. In real world, all problems exist. Large fluctuations, but the pressure sensor has the highest accuracy near 1 atmospheric pressure, and the pressure sensor error has completely covered the pressure fluctuation range at a distance away from 1 atmosphere pressure. In fact, there are large fluctuations as a whole, but the pressure sensor has the highest accuracy near 1 atmosphere pressure, and the error of pressure sensor has completely covered pressure fluctuation range at a distance away from 1 atmosphere pressure.
(2) Pressure control adopts switch control mode. Vacuum pump and solenoid valve are opened or closed at the same time according to pressure setting value. Although gas storage tank is added as a buffer, it is difficult to achieve accurate and constant pressure in this semi-automatic control mode.
(3) Controller does not use the PID automatic control method which is also the main reason for affecting pressure control accuracy. Based on the above analysis, focusing on the problems of poor control accuracy and stability of pressure control system with low-pressure environment simulation chamber used for calibration of the previous generation sound, and an inaccurate configuration of the pressure sensor and control system. Users proposed upgrading and transformation requirements. This article will introduce implementation scheme of the new generation with low-pressure environment simulation chamber pressure control system. Bi-directional control mode is proposed to be adopted, and the scheme verification test will be carried out, which proves that control accuracy and stability can be greatly improved.
2. Upgrading and reforming pressure control system using FC series electric needle valve The absolute pressure range of the low-pressure environment simulation chamber for sonde verification is 1torr~760torr.It is required that pressure of simulation chamber can be accurately and constant at any set point within this range, and it can even be controlled according to the set pressure transformation rate. For this reason, the specific upgrade scheme is to keep vacuum pump and vacuum solenoid valve on the basis of original pressure control system, replace pressure sensor and controller, remove energy storage tank, and increase numerically controlled air intake valve and exhaust valve. The specific scheme is as follows:
(1) Capacitance pressure gauge with 10torr and 1000torrare used to cover measurement of the entire low pressure range, thereby ensuring measurement accuracy of the full range.
(2) High-precision PID vacuum pressure controller is used to match measurement accuracy of capacitive pressure gauge and ensure control accuracy.
(3) Install an electric needle valve at air inlet and exhaust port of vacuum chamber respectively. The electric needle valve is directly installed at air inlet.
(4) The control mode adopts upstream mode and downstream mode respectively. Upstream mode is used to control air pressure below 10torr, and downstream mode is used to control air pressure in the range of 10~760torr using KaoLu electric needle valve (https://www.genndih.com/proportional-flow-control-valve.htm)
(5) As shown in Figure 2, upstream mode is to maintain upstream pressure and outlet flow constant, and control chamber pressure by adjusting inlet flow.
(6) As shown in Figure 3, downstream mode is to maintain upstream pressure and inlet flow constant, and control chamber pressure by adjusting exhaust flow.
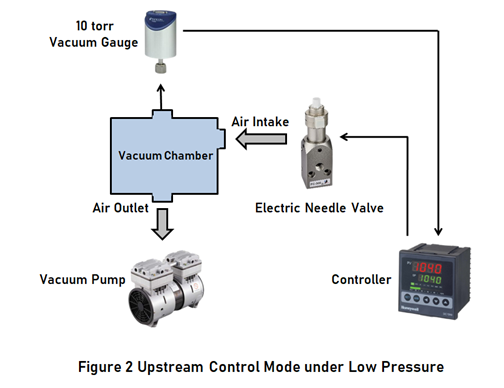
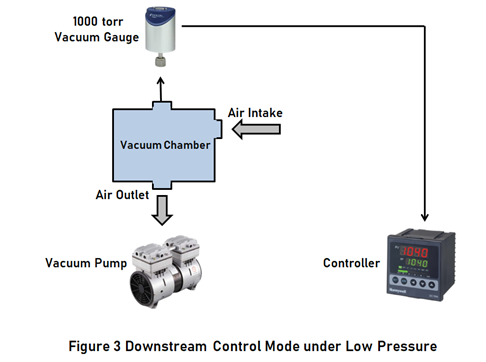
3. Certification test of scheme
For the above two control modes, two capacitive pressure gauges of 1torr and 1000torr, an electric needle valve and a 24-bit high-precision pressure controller were used to conduct the assessment test. The internal space of vacuum chamber used for test was 400×400× 500mm; the test device is shown in Figure 4 and Figure 5.
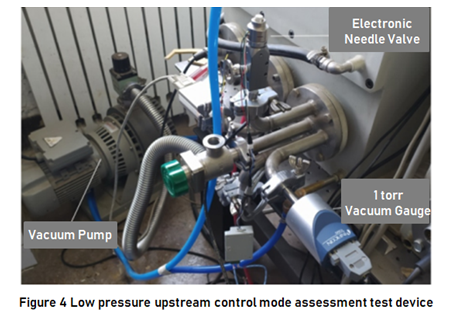
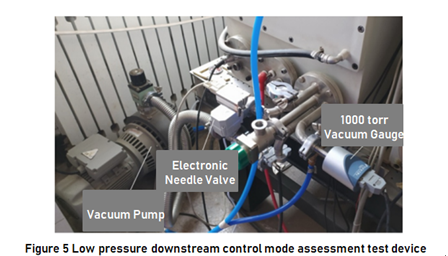
During the upstream mode test, vacuum pump was first turned on and then pumped at full speed. Then the PID parameters of controller were self-tuned at about 68Pa. After the auto-tuning is completed, 8 set points of 12, 27, 40, 53, 67, 80, 93 and 107Pa are controlled respectively. The air pressure changes during the whole control process are shown in Figure 6. During the downstream mode test, vacuum pump was first turned on and then pumped at full speed, and air intake electric needle valve was adjusted to the position of micro intake. Then the PID parameters of controller were self-tuned at about 300torr. After the auto-tuning is completed, 5 set points of 70, 200, 300, 450 and 600 Torr are controlled respectively. The air pressure changes during the whole control process are shown in Figure 7.
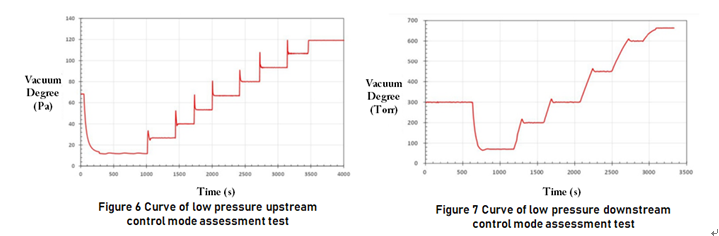
By expressing the above control effects at different low pressure constant points as fluctuation rate, fluctuation rate distribution in the entire range shown in Figures 8 and 9 is obtained. It can be seen from fluctuation rate distribution diagram that fluctuation rate can be accurately controlled within the range of ±1% in the whole range of low pressure. The large fluctuation at 12Pa is because the PID parameters obtained by self-tuning at 68Pa are invalid, and a separate PID parameter self-tuning is required.
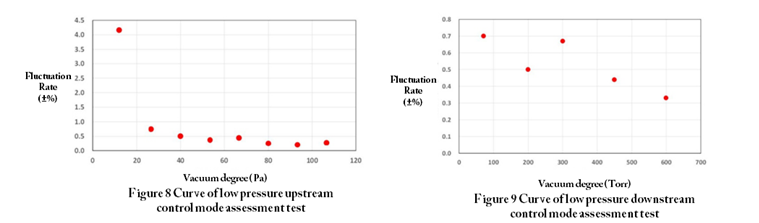
It can be seen from the above test results that the electric needle valve can improve the pressure control accuracy and stability by more than five times, and greatly improve the automation level and reliability of the low-pressure environment simulation chamber. For further information on the introduced electric needle valve, please visit https://www.genndih.com/proportional-flow-control-valve/miniature-proportional-valve-0-32L-min.html