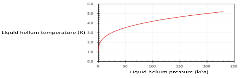
2022.02.17
Vacuum Pressure Control in Cryostat
SHARE
MORE DETAIL
Abstract: Focusing on high-precision control of low-temperature medium in cryostat, this article mainly introduces decompression and temperature-control method of low-temperature medium and the influence of air pressure control accuracy on the low-temperature stability. Three modes of heating, flow control and pressure control, as well as corresponding specific working conditions that incorporate electric pneumatic flow control valve and details.
1. Introduction
In cryostat, the main reason for temperature fluctuation of cryogenic medium (liquid helium and liquid nitrogen, etc.) is the change of pressure (vacuum) at the top of boiling cryogenic medium. Therefore, in order to reach stable temperature inside cryogenic medium, it is necessary to accurately control air pressure at the top of cryogenic medium.
The international and localized temperature control of cryostats mostly adopts the following three technical approaches:
(1) Active control method: The heating circuit directly leads into vacuum chamber immersed in the low-temperature medium, and temperature real-time monitoring data of vacuum chamber is used to compare with target temperature value and then control the current added to heating circuit.
(2) Passive control method: Control air pressure at the top of low temperature medium to stabilize temperature of low temperature medium.
(3) Composite control method: The above two control methods are combined, and heating control circuit directly lead into vacuum chamber immersed in the low temperature medium, and air pressure above the low temperature medium is also controlled at the same time. The resistance heating temperature control method is already a very mature technology. This article will mainly focus on pressure control method at the top of low temperature medium, and introduce the influence of pressure control accuracy on the low temperature stability, as well as the realization method and specific scheme of high precision pressure control.
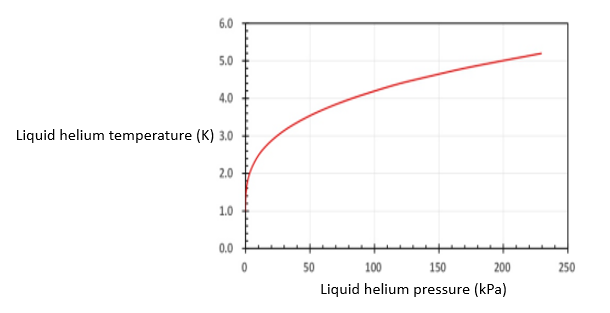
2. The relationship between air pressure control accuracy and temperature stability
Taking liquid hydrogen as an example, saturated vapor pressure of liquid hydrogen and the corresponding temperature change curve are shown in Figure 1.
As can be seen in Figure 1, in a very small temperature range, the above curve can be described by a straight line, so it can be obtained in temperature range of about 4K; fluctuation of air pressure about 100Pa can cause a temperature fluctuation of about 1mK. Therefore, it can be considered that if fluctuation of less than 1mK is to be reached, fluctuation of air pressure cannot exceed 100Pa.
3. Three modes of top air pressure control
There are generally three modes of air pressure control at the top of the cryogenic medium: resistance heating, flow control and pressure control.
3.1 Resistance heating mode
In constant temperature control process of cryostat, the resistance heating mode is to place a resistance wire heater in low temperature medium. As shown in Figure 2, vacuum gauge detects the change of air pressure at the top, and PID controller changes heating current to adjust and control top air pressure, keep the top air pressure constant at set value. It can be seen from Figure 2 that resistance heating mode is more suitable for increasing temperature control method of increasing pressure at the top, but it cannot reduce pressure and cooling.
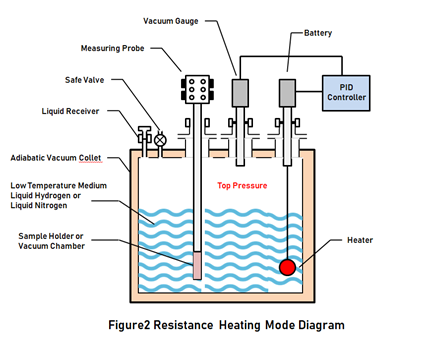
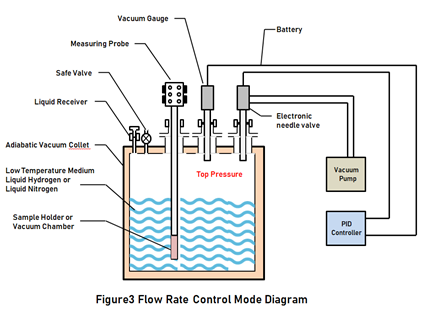
3.2 Flow Control Mode
Flow control mode is a typical reducing pressure and cooling mode. As shown in Figure 3, vacuum pump continuously extracts cryostat at a certain pumping speed to reduce the top air pressure. The vacuum gauge, electronic pneumatic flow control valve and PID controller form a closed-loop control loop. The FC series electronic pneumatic flow control valve adjusts air flow to keep the top air pressure accurately and constant at vacuum degree. It can be seen that the flow control mode is more suitable for cooling and temperature control method of reducing the top air pressure, but it cannot reach supercharging and heating.
In addition, in flow control mode, the continuous pumping of vacuum pump makes ineffective dissipation of the low temperature medium more serious.
For further information on FC series electronic pneumatic flow control valve, please visit https://www.genndih.com/proportional-flow-control-valve.htm
3.3 Pressure Control Mode
Pressure control mode is a temperature control mode that can increase or decrease pressure. As shown in Figure 4, when adopting vacuum pump to evacuate is the mode of reducing pressure. When adopting booster pump is the mode of increasing pressure. So that it can reach continuous temperature control in a wide temperature area. The used proportional pressure regulator comes with one air inlet (atmospheric pressure). Combined with vacuum pump, it can effectively avoid a large amount of ineffective dissipation of low temperature medium while controlling the top pressure at a constant pressure.
In addition, the supercharging method here can also be reached by adding an electric heater to the low temperature medium.
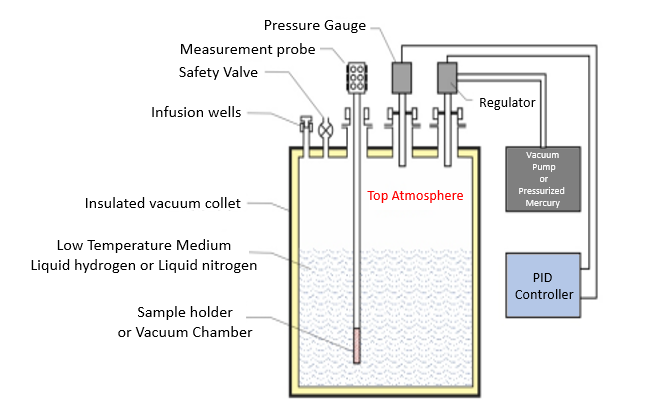
4. Additional Working Details
During implementation of the above three control modes, it should specifically notice to the following details:
(1) Selection of vacuum gauge Vacuum gauge is a sensor that measures change in air pressure at the top. The key to determining the stability of temperature control of cryostat, so be sure to choose a high-precision vacuum gauge. At present, high-precision vacuum gauges are generally capacitive film gauges, and the general overall accuracy is 0.2%. As mentioned above, in constant temperature control process of liquid hydrogen around 4K, air pressure fluctuation is required not to exceed 100Pa, and ±50Pa. If it corresponds to air pressure control of 100kPa, the accuracy of vacuum gauge needs to be higher than ±0.05%. It can be seen that constant temperature control with temperature fluctuation less than 1mK, a higher precision vacuum gauge is also required.
(2) Selection of PID controller In the process of constant temperature control, PID controller collects measured value of vacuum gauge through A/D converter, and then sends control signal to actuator (electric needle valve, pressure regulator and heating power supply, etc.) through the D/A converter after calculation. ). For this reason, to ensure that high precision and control accuracy of vacuum gauge can be fully utilized and regulated with an electronic pneumatic flow control valve, the higher the precision of A/D and D/A converters, the better at least 16 bit, and a 24-bit high-precision PID controller is strongly recommended.
(3) Allocation of voltage regulator Pressure regulator is a pressure control device that integrates a vacuum pressure sensor, a controller and a valve, but the accuracy of vacuum pressure sensor is far less than thin-film capacitor, and the accuracy of controller is also relatively low. Thus, when using a voltage regulator, an external control mode should be selected, that is, a thin-film capacitor is used as a control sensor.
In addition, it should be noted that A/D and D/A converters of controller in regulator have low precision. Thus, for high-precision and high-stability top air pressure control, pressure control mode is not recommended unless a specially made high-precision voltage regulator is used.
1. Introduction
In cryostat, the main reason for temperature fluctuation of cryogenic medium (liquid helium and liquid nitrogen, etc.) is the change of pressure (vacuum) at the top of boiling cryogenic medium. Therefore, in order to reach stable temperature inside cryogenic medium, it is necessary to accurately control air pressure at the top of cryogenic medium.
The international and localized temperature control of cryostats mostly adopts the following three technical approaches:
(1) Active control method: The heating circuit directly leads into vacuum chamber immersed in the low-temperature medium, and temperature real-time monitoring data of vacuum chamber is used to compare with target temperature value and then control the current added to heating circuit.
(2) Passive control method: Control air pressure at the top of low temperature medium to stabilize temperature of low temperature medium.
(3) Composite control method: The above two control methods are combined, and heating control circuit directly lead into vacuum chamber immersed in the low temperature medium, and air pressure above the low temperature medium is also controlled at the same time. The resistance heating temperature control method is already a very mature technology. This article will mainly focus on pressure control method at the top of low temperature medium, and introduce the influence of pressure control accuracy on the low temperature stability, as well as the realization method and specific scheme of high precision pressure control.
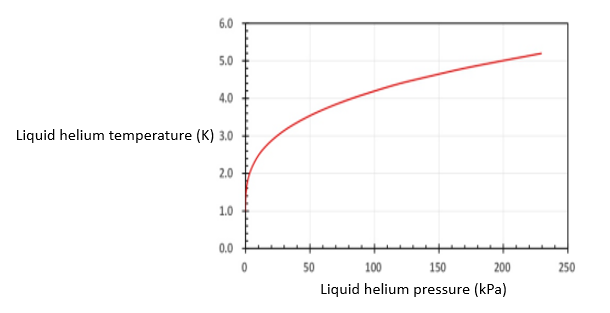
2. The relationship between air pressure control accuracy and temperature stability
Taking liquid hydrogen as an example, saturated vapor pressure of liquid hydrogen and the corresponding temperature change curve are shown in Figure 1.
As can be seen in Figure 1, in a very small temperature range, the above curve can be described by a straight line, so it can be obtained in temperature range of about 4K; fluctuation of air pressure about 100Pa can cause a temperature fluctuation of about 1mK. Therefore, it can be considered that if fluctuation of less than 1mK is to be reached, fluctuation of air pressure cannot exceed 100Pa.
3. Three modes of top air pressure control
There are generally three modes of air pressure control at the top of the cryogenic medium: resistance heating, flow control and pressure control.
3.1 Resistance heating mode
In constant temperature control process of cryostat, the resistance heating mode is to place a resistance wire heater in low temperature medium. As shown in Figure 2, vacuum gauge detects the change of air pressure at the top, and PID controller changes heating current to adjust and control top air pressure, keep the top air pressure constant at set value. It can be seen from Figure 2 that resistance heating mode is more suitable for increasing temperature control method of increasing pressure at the top, but it cannot reduce pressure and cooling.
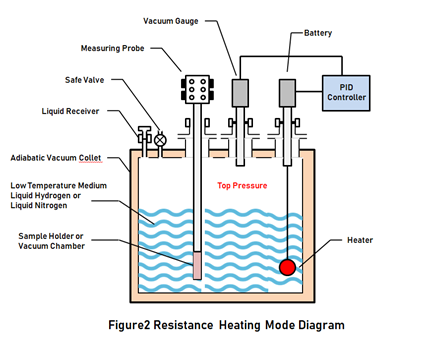
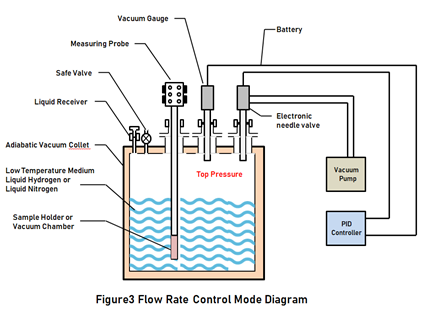
3.2 Flow Control Mode
Flow control mode is a typical reducing pressure and cooling mode. As shown in Figure 3, vacuum pump continuously extracts cryostat at a certain pumping speed to reduce the top air pressure. The vacuum gauge, electronic pneumatic flow control valve and PID controller form a closed-loop control loop. The FC series electronic pneumatic flow control valve adjusts air flow to keep the top air pressure accurately and constant at vacuum degree. It can be seen that the flow control mode is more suitable for cooling and temperature control method of reducing the top air pressure, but it cannot reach supercharging and heating.
In addition, in flow control mode, the continuous pumping of vacuum pump makes ineffective dissipation of the low temperature medium more serious.
For further information on FC series electronic pneumatic flow control valve, please visit https://www.genndih.com/proportional-flow-control-valve.htm
3.3 Pressure Control Mode
Pressure control mode is a temperature control mode that can increase or decrease pressure. As shown in Figure 4, when adopting vacuum pump to evacuate is the mode of reducing pressure. When adopting booster pump is the mode of increasing pressure. So that it can reach continuous temperature control in a wide temperature area. The used proportional pressure regulator comes with one air inlet (atmospheric pressure). Combined with vacuum pump, it can effectively avoid a large amount of ineffective dissipation of low temperature medium while controlling the top pressure at a constant pressure.
In addition, the supercharging method here can also be reached by adding an electric heater to the low temperature medium.
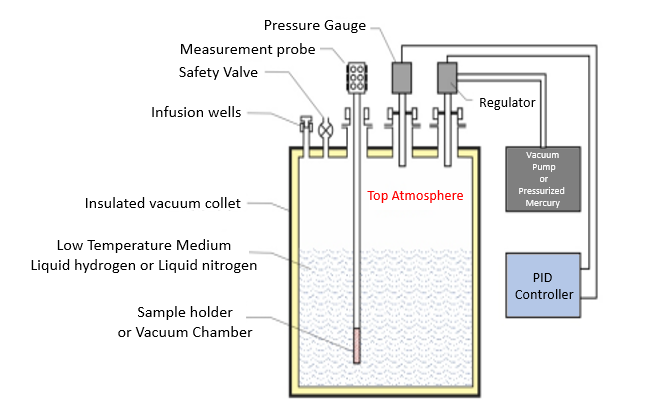
4. Additional Working Details
During implementation of the above three control modes, it should specifically notice to the following details:
(1) Selection of vacuum gauge Vacuum gauge is a sensor that measures change in air pressure at the top. The key to determining the stability of temperature control of cryostat, so be sure to choose a high-precision vacuum gauge. At present, high-precision vacuum gauges are generally capacitive film gauges, and the general overall accuracy is 0.2%. As mentioned above, in constant temperature control process of liquid hydrogen around 4K, air pressure fluctuation is required not to exceed 100Pa, and ±50Pa. If it corresponds to air pressure control of 100kPa, the accuracy of vacuum gauge needs to be higher than ±0.05%. It can be seen that constant temperature control with temperature fluctuation less than 1mK, a higher precision vacuum gauge is also required.
(2) Selection of PID controller In the process of constant temperature control, PID controller collects measured value of vacuum gauge through A/D converter, and then sends control signal to actuator (electric needle valve, pressure regulator and heating power supply, etc.) through the D/A converter after calculation. ). For this reason, to ensure that high precision and control accuracy of vacuum gauge can be fully utilized and regulated with an electronic pneumatic flow control valve, the higher the precision of A/D and D/A converters, the better at least 16 bit, and a 24-bit high-precision PID controller is strongly recommended.
(3) Allocation of voltage regulator Pressure regulator is a pressure control device that integrates a vacuum pressure sensor, a controller and a valve, but the accuracy of vacuum pressure sensor is far less than thin-film capacitor, and the accuracy of controller is also relatively low. Thus, when using a voltage regulator, an external control mode should be selected, that is, a thin-film capacitor is used as a control sensor.
In addition, it should be noted that A/D and D/A converters of controller in regulator have low precision. Thus, for high-precision and high-stability top air pressure control, pressure control mode is not recommended unless a specially made high-precision voltage regulator is used.