SHARE
MORE DETAIL
For cryogenic temperature control within the liquid nitrogen temperature range, the following two commonly used methods are currently used:
(1) Direct immersion type: that is, the test piece is completely immersed in liquid nitrogen for cooling and corresponding temperature control, but in this way, the cooling temperature of the test piece cannot be controlled and adjusted in a wide low temperature range. It can only be adjusted and controlled in a small range by controlling the pressure of liquid nitrogen at a temperature close to -196°C.
In addition, the direct immersion method often does not wait for the test piece to reach the cooling and holding time, and liquid nitrogen has basically completely volatilized. At the same time, this kind of operation method is relatively simple and has high requirements for actual operators, and safety accidents may occur if there is a slight carelessness.
(2) Liquid nitrogen purging method: that is, direct use of flow-controllable liquid nitrogen or liquid nitrogen gas for purging to adjust and control the low-temperature temperature of the test piece. When the purging method is used for cryogenic temperature control, the flow rate of liquid nitrogen or liquid nitrogen gas is directly related to the stability and reliability of temperature of test piece.
At the same time, the flow control of low-temperature medium has always been a difficult and painful point in the industry, which requires that all components in KaoLu's Proportional Pressure Regulator on the low-temperature pipeline need to have good low-temperature resistance characteristics, and the price is very expensive. Some rudimentary low-temperature control uses low-temperature switch valves for on-off control. Although the cost of the valve is reduced, the control accuracy of this switch control mode is extremely poor.
In addition, the outlet of low-temperature medium is in direct contact with the test piece or the air in heat exchanger, and the water vapor in air freezes rapidly when it is cooled. As the cooling time increases, the outlet of low-temperature medium is easily blocked by freezing. There is an urgent need to develop a test device that can reach ultra-low temperature control of the core control device at room temperature.
In order to solve problems in the above-mentioned liquid nitrogen purging method, this article provides three solutions for wide range temperature control of liquid nitrogen temperature range with different precision. The technical core of the solution is to reach precise control of low-temperature temperature by adjusting the flow or pressure of gas source at room temperature, and it is no longer necessary for KaoLu's Proportional Pressure Regulator to have low-temperature resistance. At the same time, on the basis of above two technical solutions, a third solution in the form of electric heating will be added, thereby reaching higher precision low-temperature temperature control.
The principle and analysis
In the traditional liquid nitrogen cryogenic temperature control purging method, it is common to directly adjust the purging flow rate of liquid nitrogen cryogenic medium, and at the same time combine the temperature sensor and PID controller to form a closed-loop control loop, and finally reach the cryogenic temperature control by controlling the flow rate.
By analyzing the above-mentioned traditional liquid nitrogen purging method, it can be found that the basic principle of low temperature medium purging is to form a higher air pressure in liquid nitrogen tank (cryogenic storage Dewar) to force liquid nitrogen or liquid nitrogen gas to overflow into the set pipeline to form The low temperature medium flows, and finally the low temperature control is carried out by adjusting the flow speed. Therefore, the high-pressure gas in the liquid nitrogen tank is the key to all these.
As long as the gas pressure can be adjusted, low-temperature media with different flow rates can also be formed in the fixed pipeline to reach the purpose of temperature control. At the same time, this method of adjusting gas pressure in liquid nitrogen tank can be reached at room temperature, thus avoiding the need to use special and expensive electric cryogenic regulating valves in direct cryogenic medium flow control.
Based on the above analysis, this article designs the following three low temperature control schemes, and can achieve different control precision.
Air Intake Flow Control Scheme
For any container with a certain space size, its internal pressure can be attributed to a dynamic equilibrium state reached by the intake and outlet flow. Therefore, if the gas pressure in liquid nitrogen tank is to be controlled, one of the effective methods is to adjust the gas flow in and out of the liquid nitrogen tank to reach dynamic balance.
It should be noted that in the actual low-temperature control system, the liquid outlet or gas outlet of liquid nitrogen tank is often directly connected to cooling pipeline of test piece. If the flow of low-temperature medium is directly controlled at the outlet of liquid nitrogen tank, a cryogenic valve is required. At this time, air outlet aperture can be kept constant without adjusting the flow rate, and only the intake flow rate of the liquid nitrogen tank can be adjusted. The specific scheme is shown in Figure 1.
.png)
It can be seen from Figure 1 that the high-pressure gas (generally nitrogen) passes through the pressure reducing valve to form a fixed-pressure gas, and the room-temperature high-pressure gas flows through the electric needle valve and the intake pipe into the liquid nitrogen in the Dewar bottle. After the high-pressure gas at room temperature enters the liquid nitrogen, the liquid nitrogen is evaporated and volatilized into a gas. The volatile gas flows through the heat exchanger in the test device through the gas outlet pipe while gradually increasing the pressure in the sealed Dewar flask.
Discharge after the changer. It can be seen that by adjusting the electric needle valve installed on the air intake pipeline, the larger the opening of the needle valve, the faster the flow rate of the air inlet, the more intense the volatilization of liquid nitrogen, the higher the pressure in the Dewar bottle, and finally the flow through The faster the flow rate of the low-temperature medium in the heat exchanger, the faster the corresponding cooling rate. Another main feature of this solution is that the electric needle valve can work at room temperature.
It can be seen that the solution of adjusting the intake air flow at room temperature is to form a low-temperature closed-loop control loop through the electric needle valve, temperature sensor and PID program controller, so that the fixed-point control or program control of the low-temperature temperature can be reached. However, the problem with this solution is that the temperature control accuracy is poor, and generally there will be temperature fluctuations of 2~5°C. The main reasons are as follows:
(1) Due to a certain flow rate of high-pressure gas, the pressure in Dewar bottle changes, and the change in pressure changes flow rate of cooling medium. The sublimation process and pressure change process are more complicated, which makes intake flow rate and pressure. It is not a simple linear relationship with temperature, which is the main factor causing inaccurate temperature control. Unless the speed of the entire conditioning process is very fast, but it’s often a slow process in action.
(2) This technical method of only using low-temperature media for temperature control has the disadvantages of fast cooling and slow heating. Once the actual temperature exceeds the set point temperature, it often requires slow cooling of the test piece to reach temperature recovery. This is another reason why low pressure control can’t hardly reach higher accuracy.
Air intake pressure control scheme
In order to solve the problem of pressure instability in the above-mentioned flow control process, another solution proposed in this article is to directly control the pressure in Dewar bottle, that is, to reach the Dewar pressure by adjusting and controlling the pressure of high-pressure gas inlet inside the bottle. The specific scheme is shown in Figure 2.
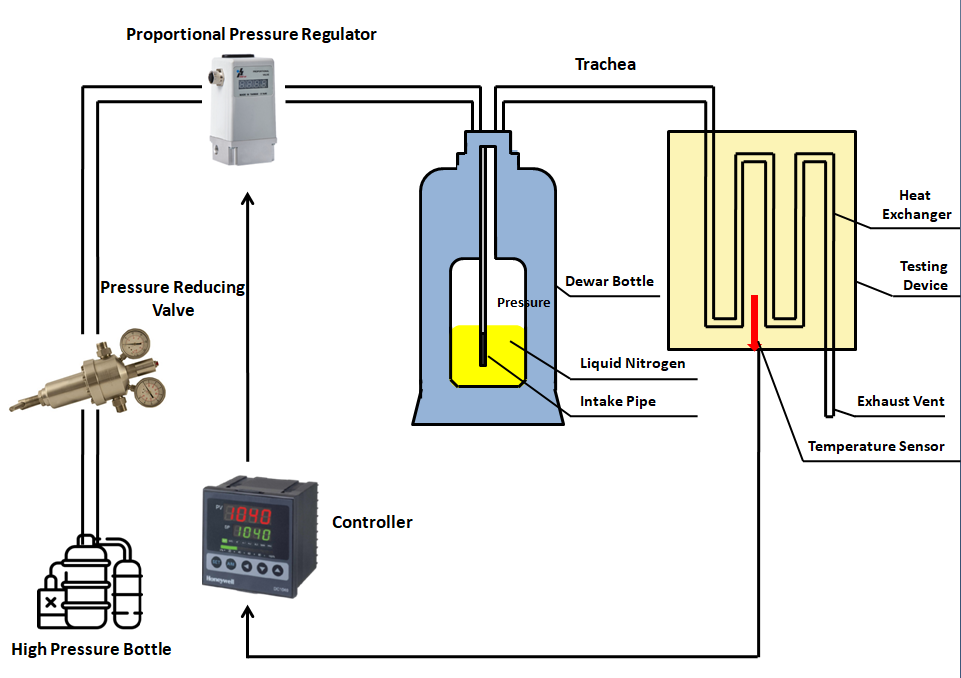
It can be seen from Figure 2 that the pressure of high-pressure gas is controlled according to the set value at air inlet through Proportional Pressure Regulator, thereby ensuring that the pressure in Dewar bottle is always in an accurately controlled state. A double-closed-loop cascade control loop composed of Proportional Pressure Regulator, a temperature sensor and a PID program controller (Proportional Pressure Regulator is an auxiliary control loop, and PID controller is connected with temperature sensor and Proportional Pressure Regulator mechanism into the main control loop).
You can adjust the output pressure of Proportional Pressure Regulator to control the gas pressure in Dewar vessel, the greater the pressure in Dewar vessel, the faster the flow rate of low-temperature medium flowing through the heat exchanger, and the corresponding cooling rate is also faster.
Therefore, the PID controller automatically adjusts the gas pressure in Dewar vessel according to the set point or the set program, so that more accurate control of cryogenic temperature can be reached, and the control uncertainty caused by the complicated sublimation process can be avoided. Compared with the aforementioned flow control scheme, the structure of pressure control scheme is also very simple, which improves the temperature control accuracy of the temperature control system, and at the same time retains the advantage of being able to adjust at room temperature.
Another outstanding advantage of pressure control scheme is that it can control the low temperature of large-sized test pieces, mainly because the pressure control in the large-sized liquid nitrogen Dewar bottle is far more convenient and accurate than the flow control. The flow control scheme due to the limitation of flow adjustment range by the caliber of Proportional Pressure Regulator, the slow response speed of the large-diameter Proportional Pressure Regulator will also bring errors to the temperature control.
Although the pressure control scheme is an upgrade of flow control scheme and also improves the temperature control accuracy. It still does not solve the disadvantages of fast cooling but slow temperature recovery in the single cooling method, and there are still problems of limited temperature control accuracy and slow temperature control speed.
Electric heating auxiliary intake pressure control scheme
In order to completely solve the problem of low temperature control accuracy and slow speed caused by the cooling block in the single cooling mode but the slow temperature recovery. This article proposes another optimization scheme, that is, on the basis of the intake pressure control scheme.
Electric heater is added to provide the heating function, thereby providing an active heating device to cooperate with the cooling system to form a dual-action system of cold and heat. When the temperature of test piece is lower than set value, the automatic active heating forms fine-tuning, so that temperature can be quickly returned to the set value. It can also greatly improve the temperature control accuracy. The specific scheme is shown in Figure 3.
.png)
As shown in Figure 3, the optimization scheme is to add an electric heater on the basis of scheme shown in Figure 2, that is, to add a channel of temperature control with pure heating function. At the same time, in order to support the realization of this heating function, in addition to adding a temperature sensor, a dual-channel PID regulator of KaoLu’s QKL series is also used.
As a result, two independent control loops are formed, one loop controls the intake pressure to reach rough adjustment of low temperature, and the other loop controls heating to reach fine adjustment of low temperature, thus ensuring the speed and accuracy of temperature control at the same time.
The solution proposed in this article completely solves the problem of needing to be equipped with expensive electric low-temperature regulating valves in the low-temperature control of the liquid nitrogen temperature zone in the past, and also solves the problem of poor temperature control accuracy of low-temperature switching valves.
The three solutions described in this article are applicable to and meet the temperature control of different requirements in a wide range of liquid nitrogen temperature ranges, and can be selected and used according to specific situations in practical applications. Among them, the applicable temperature control range of the control flow and pressure control scheme is 0°C~-150°C, while the controllable temperature range of the pressure control scheme after the auxiliary heater function is 150°C~-150°C, the upper limit temperature here is mainly affected by low temperature resistance of the heater is determined.
All the above-mentioned low temperature control schemes are only applicable to the purging form of liquid nitrogen gas, so the temperature is not very low, but it provides technical reference for direct flow cooling and temperature control of lower temperature liquid nitrogen medium.
For information about KaoLu's QKL Series Proportional Pressure Regulator, please visit our website!
(1) Direct immersion type: that is, the test piece is completely immersed in liquid nitrogen for cooling and corresponding temperature control, but in this way, the cooling temperature of the test piece cannot be controlled and adjusted in a wide low temperature range. It can only be adjusted and controlled in a small range by controlling the pressure of liquid nitrogen at a temperature close to -196°C.
In addition, the direct immersion method often does not wait for the test piece to reach the cooling and holding time, and liquid nitrogen has basically completely volatilized. At the same time, this kind of operation method is relatively simple and has high requirements for actual operators, and safety accidents may occur if there is a slight carelessness.
(2) Liquid nitrogen purging method: that is, direct use of flow-controllable liquid nitrogen or liquid nitrogen gas for purging to adjust and control the low-temperature temperature of the test piece. When the purging method is used for cryogenic temperature control, the flow rate of liquid nitrogen or liquid nitrogen gas is directly related to the stability and reliability of temperature of test piece.
At the same time, the flow control of low-temperature medium has always been a difficult and painful point in the industry, which requires that all components in KaoLu's Proportional Pressure Regulator on the low-temperature pipeline need to have good low-temperature resistance characteristics, and the price is very expensive. Some rudimentary low-temperature control uses low-temperature switch valves for on-off control. Although the cost of the valve is reduced, the control accuracy of this switch control mode is extremely poor.
In addition, the outlet of low-temperature medium is in direct contact with the test piece or the air in heat exchanger, and the water vapor in air freezes rapidly when it is cooled. As the cooling time increases, the outlet of low-temperature medium is easily blocked by freezing. There is an urgent need to develop a test device that can reach ultra-low temperature control of the core control device at room temperature.
In order to solve problems in the above-mentioned liquid nitrogen purging method, this article provides three solutions for wide range temperature control of liquid nitrogen temperature range with different precision. The technical core of the solution is to reach precise control of low-temperature temperature by adjusting the flow or pressure of gas source at room temperature, and it is no longer necessary for KaoLu's Proportional Pressure Regulator to have low-temperature resistance. At the same time, on the basis of above two technical solutions, a third solution in the form of electric heating will be added, thereby reaching higher precision low-temperature temperature control.
The principle and analysis
In the traditional liquid nitrogen cryogenic temperature control purging method, it is common to directly adjust the purging flow rate of liquid nitrogen cryogenic medium, and at the same time combine the temperature sensor and PID controller to form a closed-loop control loop, and finally reach the cryogenic temperature control by controlling the flow rate.
By analyzing the above-mentioned traditional liquid nitrogen purging method, it can be found that the basic principle of low temperature medium purging is to form a higher air pressure in liquid nitrogen tank (cryogenic storage Dewar) to force liquid nitrogen or liquid nitrogen gas to overflow into the set pipeline to form The low temperature medium flows, and finally the low temperature control is carried out by adjusting the flow speed. Therefore, the high-pressure gas in the liquid nitrogen tank is the key to all these.
As long as the gas pressure can be adjusted, low-temperature media with different flow rates can also be formed in the fixed pipeline to reach the purpose of temperature control. At the same time, this method of adjusting gas pressure in liquid nitrogen tank can be reached at room temperature, thus avoiding the need to use special and expensive electric cryogenic regulating valves in direct cryogenic medium flow control.
Based on the above analysis, this article designs the following three low temperature control schemes, and can achieve different control precision.
Air Intake Flow Control Scheme
For any container with a certain space size, its internal pressure can be attributed to a dynamic equilibrium state reached by the intake and outlet flow. Therefore, if the gas pressure in liquid nitrogen tank is to be controlled, one of the effective methods is to adjust the gas flow in and out of the liquid nitrogen tank to reach dynamic balance.
It should be noted that in the actual low-temperature control system, the liquid outlet or gas outlet of liquid nitrogen tank is often directly connected to cooling pipeline of test piece. If the flow of low-temperature medium is directly controlled at the outlet of liquid nitrogen tank, a cryogenic valve is required. At this time, air outlet aperture can be kept constant without adjusting the flow rate, and only the intake flow rate of the liquid nitrogen tank can be adjusted. The specific scheme is shown in Figure 1.
.png)
It can be seen from Figure 1 that the high-pressure gas (generally nitrogen) passes through the pressure reducing valve to form a fixed-pressure gas, and the room-temperature high-pressure gas flows through the electric needle valve and the intake pipe into the liquid nitrogen in the Dewar bottle. After the high-pressure gas at room temperature enters the liquid nitrogen, the liquid nitrogen is evaporated and volatilized into a gas. The volatile gas flows through the heat exchanger in the test device through the gas outlet pipe while gradually increasing the pressure in the sealed Dewar flask.
Discharge after the changer. It can be seen that by adjusting the electric needle valve installed on the air intake pipeline, the larger the opening of the needle valve, the faster the flow rate of the air inlet, the more intense the volatilization of liquid nitrogen, the higher the pressure in the Dewar bottle, and finally the flow through The faster the flow rate of the low-temperature medium in the heat exchanger, the faster the corresponding cooling rate. Another main feature of this solution is that the electric needle valve can work at room temperature.
It can be seen that the solution of adjusting the intake air flow at room temperature is to form a low-temperature closed-loop control loop through the electric needle valve, temperature sensor and PID program controller, so that the fixed-point control or program control of the low-temperature temperature can be reached. However, the problem with this solution is that the temperature control accuracy is poor, and generally there will be temperature fluctuations of 2~5°C. The main reasons are as follows:
(1) Due to a certain flow rate of high-pressure gas, the pressure in Dewar bottle changes, and the change in pressure changes flow rate of cooling medium. The sublimation process and pressure change process are more complicated, which makes intake flow rate and pressure. It is not a simple linear relationship with temperature, which is the main factor causing inaccurate temperature control. Unless the speed of the entire conditioning process is very fast, but it’s often a slow process in action.
(2) This technical method of only using low-temperature media for temperature control has the disadvantages of fast cooling and slow heating. Once the actual temperature exceeds the set point temperature, it often requires slow cooling of the test piece to reach temperature recovery. This is another reason why low pressure control can’t hardly reach higher accuracy.
Air intake pressure control scheme
In order to solve the problem of pressure instability in the above-mentioned flow control process, another solution proposed in this article is to directly control the pressure in Dewar bottle, that is, to reach the Dewar pressure by adjusting and controlling the pressure of high-pressure gas inlet inside the bottle. The specific scheme is shown in Figure 2.
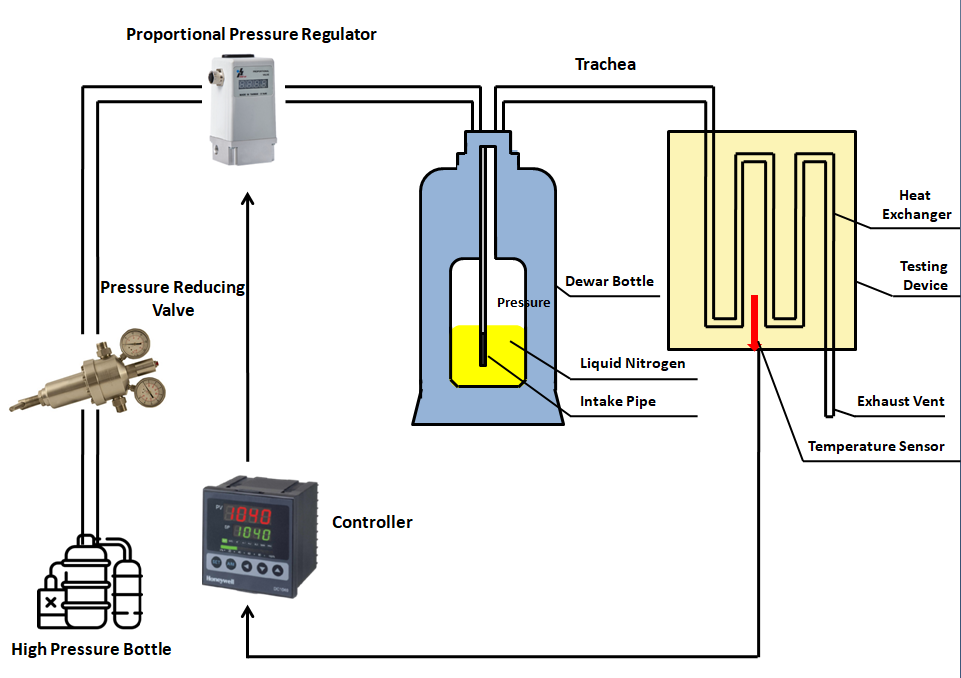
It can be seen from Figure 2 that the pressure of high-pressure gas is controlled according to the set value at air inlet through Proportional Pressure Regulator, thereby ensuring that the pressure in Dewar bottle is always in an accurately controlled state. A double-closed-loop cascade control loop composed of Proportional Pressure Regulator, a temperature sensor and a PID program controller (Proportional Pressure Regulator is an auxiliary control loop, and PID controller is connected with temperature sensor and Proportional Pressure Regulator mechanism into the main control loop).
You can adjust the output pressure of Proportional Pressure Regulator to control the gas pressure in Dewar vessel, the greater the pressure in Dewar vessel, the faster the flow rate of low-temperature medium flowing through the heat exchanger, and the corresponding cooling rate is also faster.
Therefore, the PID controller automatically adjusts the gas pressure in Dewar vessel according to the set point or the set program, so that more accurate control of cryogenic temperature can be reached, and the control uncertainty caused by the complicated sublimation process can be avoided. Compared with the aforementioned flow control scheme, the structure of pressure control scheme is also very simple, which improves the temperature control accuracy of the temperature control system, and at the same time retains the advantage of being able to adjust at room temperature.
Another outstanding advantage of pressure control scheme is that it can control the low temperature of large-sized test pieces, mainly because the pressure control in the large-sized liquid nitrogen Dewar bottle is far more convenient and accurate than the flow control. The flow control scheme due to the limitation of flow adjustment range by the caliber of Proportional Pressure Regulator, the slow response speed of the large-diameter Proportional Pressure Regulator will also bring errors to the temperature control.
Although the pressure control scheme is an upgrade of flow control scheme and also improves the temperature control accuracy. It still does not solve the disadvantages of fast cooling but slow temperature recovery in the single cooling method, and there are still problems of limited temperature control accuracy and slow temperature control speed.
Electric heating auxiliary intake pressure control scheme
In order to completely solve the problem of low temperature control accuracy and slow speed caused by the cooling block in the single cooling mode but the slow temperature recovery. This article proposes another optimization scheme, that is, on the basis of the intake pressure control scheme.
Electric heater is added to provide the heating function, thereby providing an active heating device to cooperate with the cooling system to form a dual-action system of cold and heat. When the temperature of test piece is lower than set value, the automatic active heating forms fine-tuning, so that temperature can be quickly returned to the set value. It can also greatly improve the temperature control accuracy. The specific scheme is shown in Figure 3.
.png)
As shown in Figure 3, the optimization scheme is to add an electric heater on the basis of scheme shown in Figure 2, that is, to add a channel of temperature control with pure heating function. At the same time, in order to support the realization of this heating function, in addition to adding a temperature sensor, a dual-channel PID regulator of KaoLu’s QKL series is also used.
As a result, two independent control loops are formed, one loop controls the intake pressure to reach rough adjustment of low temperature, and the other loop controls heating to reach fine adjustment of low temperature, thus ensuring the speed and accuracy of temperature control at the same time.
The solution proposed in this article completely solves the problem of needing to be equipped with expensive electric low-temperature regulating valves in the low-temperature control of the liquid nitrogen temperature zone in the past, and also solves the problem of poor temperature control accuracy of low-temperature switching valves.
The three solutions described in this article are applicable to and meet the temperature control of different requirements in a wide range of liquid nitrogen temperature ranges, and can be selected and used according to specific situations in practical applications. Among them, the applicable temperature control range of the control flow and pressure control scheme is 0°C~-150°C, while the controllable temperature range of the pressure control scheme after the auxiliary heater function is 150°C~-150°C, the upper limit temperature here is mainly affected by low temperature resistance of the heater is determined.
All the above-mentioned low temperature control schemes are only applicable to the purging form of liquid nitrogen gas, so the temperature is not very low, but it provides technical reference for direct flow cooling and temperature control of lower temperature liquid nitrogen medium.
For information about KaoLu's QKL Series Proportional Pressure Regulator, please visit our website!