SHARE
MORE DETAIL
1. Introduction of Proportional Pressure Regulator
Micro-Laser Beam Welding (LBW), also known as micro-welding, is the fusion of dissimilar metals by projecting a tiny diameter laser beam to create a microscopic weld. Recently, a customer made a customized request for a vacuum control system for precise pressure regulation in the micro-laser beam welding system. The specific requirements are that welding chamber is filled with inert gas, the absolute pressure in the welding chamber is precisely and constant within the vacuum range of 10Pa to one atmosphere (0.1MPa). The pressure fluctuation at any control point is less than ±1%.
This article will propose corresponding solutions for the above-mentioned customers' technical requirements for pressure regulation of vacuum control systems in micro-laser beam welding. The specific implementation plan is to equip vacuum gauges with different ranges, inlet KaoLu’s proportional pressure regulators, outlet electric ball valves and dual-channel high-precision PID controllers, and adopt upstream and downstream control modes for different vacuum ranges to reach air pressure regulation within the full range of constant control. This solution enables constant control of vacuum at any set point over the full scale range to a fluctuation rate of less than ±1%.
2. Solution of Proportional Pressure Regulator
The air pressure adjustment range (absolute pressure) required by micro-laser beam welding is a vacuum degree of 10Pa~0.1MPa, so the fluctuation rate of vacuum degree in constant process of full range can be set arbitrarily is less than ±1%, and the welding process is also required. The air pressure fluctuation caused by air pressure can be quickly adjusted and constant, so this solution uses two control loops to cover the full scale.
The first control loop is responsible for controlling high air pressure in range of 1kPa-101kPa, and a film capacitance vacuum gauge with a range of 1000 Torr is used as the sensor. The vacuum gauge is connected to the first channel of PID controller. The PID controller adjusts proportional pressure regulator by comparing the received vacuum signal with set value, so that air pressure in welding chamber quickly reaches set value and remains constant. The second control loop is responsible for controlling low pressure in the range of 10Pa~1kPa, and uses a film capacitance vacuum gauge with a range of 10Torr as sensor.
The vacuum gauge is connected to the second channel of PID controller. The PID controller adjusts proportional pressure regulator by comparing the received vacuum signal with set value, so that air pressure in welding chamber quickly reaches the set value and remains constant.
In order to ensure control accuracy and stability, this solution requires proportional pressure regulator to have a response speed within 1 second, and requires dual-channel PID controller to have 24-bit AD and 16-bit DA high precision. This solution has been successfully used widely.
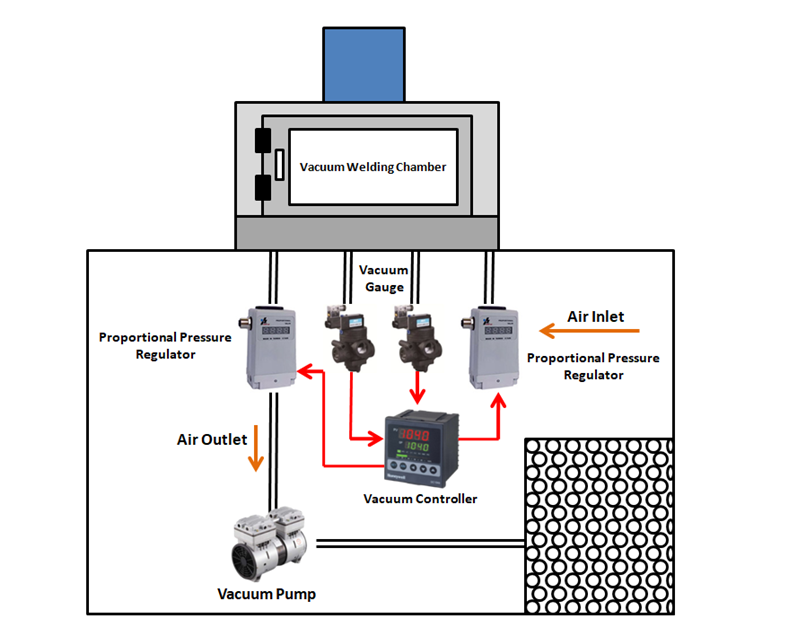
If you want to get more information about Proportional Pressure Regulator, please refer to our webite.
Micro-Laser Beam Welding (LBW), also known as micro-welding, is the fusion of dissimilar metals by projecting a tiny diameter laser beam to create a microscopic weld. Recently, a customer made a customized request for a vacuum control system for precise pressure regulation in the micro-laser beam welding system. The specific requirements are that welding chamber is filled with inert gas, the absolute pressure in the welding chamber is precisely and constant within the vacuum range of 10Pa to one atmosphere (0.1MPa). The pressure fluctuation at any control point is less than ±1%.
This article will propose corresponding solutions for the above-mentioned customers' technical requirements for pressure regulation of vacuum control systems in micro-laser beam welding. The specific implementation plan is to equip vacuum gauges with different ranges, inlet KaoLu’s proportional pressure regulators, outlet electric ball valves and dual-channel high-precision PID controllers, and adopt upstream and downstream control modes for different vacuum ranges to reach air pressure regulation within the full range of constant control. This solution enables constant control of vacuum at any set point over the full scale range to a fluctuation rate of less than ±1%.
2. Solution of Proportional Pressure Regulator
The air pressure adjustment range (absolute pressure) required by micro-laser beam welding is a vacuum degree of 10Pa~0.1MPa, so the fluctuation rate of vacuum degree in constant process of full range can be set arbitrarily is less than ±1%, and the welding process is also required. The air pressure fluctuation caused by air pressure can be quickly adjusted and constant, so this solution uses two control loops to cover the full scale.
The first control loop is responsible for controlling high air pressure in range of 1kPa-101kPa, and a film capacitance vacuum gauge with a range of 1000 Torr is used as the sensor. The vacuum gauge is connected to the first channel of PID controller. The PID controller adjusts proportional pressure regulator by comparing the received vacuum signal with set value, so that air pressure in welding chamber quickly reaches set value and remains constant. The second control loop is responsible for controlling low pressure in the range of 10Pa~1kPa, and uses a film capacitance vacuum gauge with a range of 10Torr as sensor.
The vacuum gauge is connected to the second channel of PID controller. The PID controller adjusts proportional pressure regulator by comparing the received vacuum signal with set value, so that air pressure in welding chamber quickly reaches the set value and remains constant.
In order to ensure control accuracy and stability, this solution requires proportional pressure regulator to have a response speed within 1 second, and requires dual-channel PID controller to have 24-bit AD and 16-bit DA high precision. This solution has been successfully used widely.
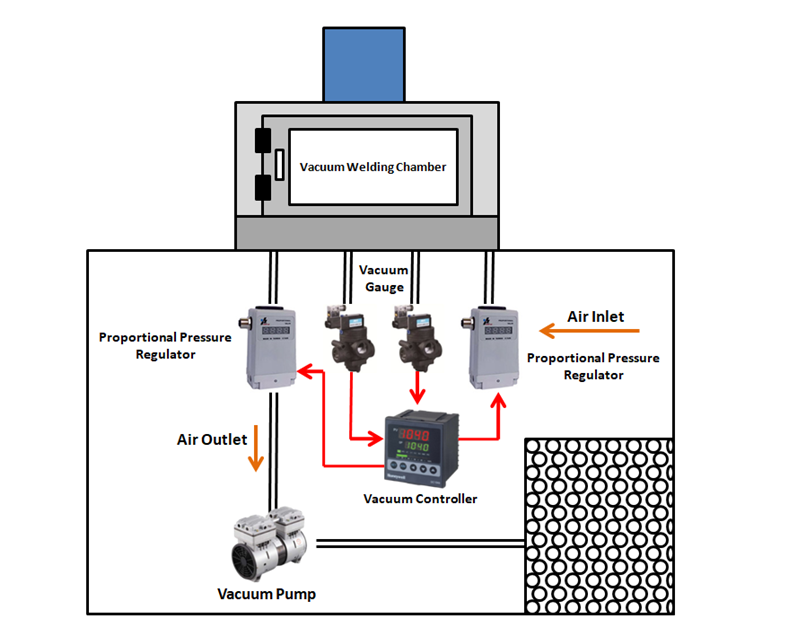
If you want to get more information about Proportional Pressure Regulator, please refer to our webite.