SHARE
MORE DETAIL
What is Oxygen Partial Pressure?
The oxygen partial pressure is defined as the pressure of oxygen gas component in gas mixture, which corresponds to the total pressure applied when oxygen gas component alone occupies the entire volume. Oxygen partial pressure is a variable commonly used to characterize the oxidation environment of substances, especially under high temperature condition, oxygen partial pressure is an important environmental variable.
Under high-temperature conditions during flight service, the heat transfer performance of aircraft outer heat-resistant materials represented by resin-based heat-resistant composite materials, low-ablation and zero-ablation structural composite materials, and high-temperature-resistant metal materials and the oxygen content of the environment in which the materials are located Pressure indicators are closely related.
Under high temperature environment, the pyrolytic carbonization reaction of resin-based heat-resistant composite materials, the sublimation and oxidation process of carbon matrix and silicon carbide matrix of low-ablation/zero-ablation structural composite materials, and surface oxidation reaction of high-temperature-resistant metal materials. Both are affected by oxygen content of environment in which material is located. Under the same high-temperature environment, the surface composition, structure, and heat transfer performance of materials vary greatly with the change of oxygen partial pressure in environment.
Therefore, in material research and ground assessment tests, it is necessary to conduct various performance tests after heat treatment of materials in a high-temperature environment with variable oxygen partial pressure. Sometimes even directly simulate a variable oxygen partial pressure high-temperature environment on corresponding test equipment and test the various physical properties of material.
In the physical performance assessment and test evaluation of heat-resistant materials for aircraft, temperature, air pressure and oxygen partial pressure are three important environmental variables. However, most of the current test instruments and equipment can only simulate the environment of temperature and air pressure changes. It is still impossible to reach precise control of variable oxygen partial pressure environment. For example, the thermal conductivity and thermal radiation coefficient of materials can only be measured in a variable temperature and vacuum environment.
However, the performance research of material ablation process can only be tested with samples after carbonization in a high-temperature vacuum environment, which cannot obtain the real performance data of materials under different oxygen partial pressures. Our customer put forward the precise control requirements of low air pressure and oxygen partial pressure, and provided support for the following tests and experiments:
- On the basis of high-temperature vacuum carbonization furnace, it is matched to reach the precise control of variable vacuum and variable oxygen partial pressure. It can be cycled multiple times to process various heat-resistant materials under alternating environmental conditions, such as resin-based heat-resistant composite materials carbonization treatment, and perform surface treatment on low-ablation/zero-ablation structural composite materials and high-temperature-resistant metal materials.
- Equipping the ablation test device to reach precise control of variable vacuum and variable oxygen partial pressure, so as to examine the ablation performance and heat insulation performance under different temperature, vacuum degree and oxygen partial pressure conditions.
- On the basis of high-temperature thermal radiation performance testing equipment, it is equipped with precise control of variable vacuum and variable oxygen partial pressure to measure the thermal radiation performance (spectral reflectance and hemispherical total emissivity) of materials under different conditions.
This article will aim at the heat-resistant design calculation and heat-resistant material modification optimization of atmospheric re-entry vehicles and hypersonic vehicles in near space. The demand for thermal physical property testing and material processing in real service environments is proposed, and a precise control solution for variable vacuum and oxygen partial pressure is proposed. This solution will use split-range control to reach high-precision vacuum control, and the supporting devices corresponding to this liberation solution can be used for high-temperature thermophysical performance parameter testing and assessment equipment for various materials.
According to the definition of partial pressure of oxygen, for a mixed gas composed of oxygen and nitrogen, the partial pressure of oxygen is equal to the mole fraction of oxygen in the mixed gas multiplied by absolute pressure value of mixed gas. It can be seen that in the process of oxygen partial pressure control, the mole fraction of oxygen in the mixed gas and the absolute pressure of the mixed gas need to be controlled simultaneously.
In addition, in the demand put forward by our customer, the absolute pressure involved is a vacuum environment less than one atmospheric pressure, and the mixed gas is generally nitrogen and oxygen, so the control problem of oxygen partial pressure can be attributed to the following two parts:
- Control the number of moles of oxygen in mixed gas.
- Control the vacuum degree (absolute pressure) of mixed gas. In order to reach the above two parts of control content, the solution proposed in this article is the oxygen partial pressure control system shown in Figure 1.
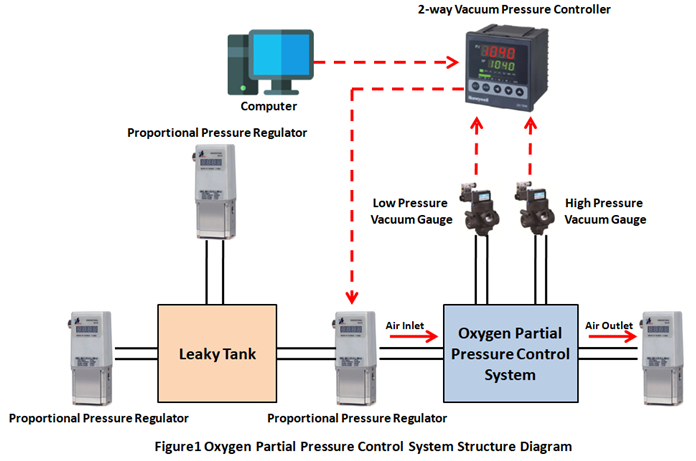
As shown in Figure 1, in order to control the number of moles of oxygen in mixed gas, two gas mass flow meters are used to control nitrogen and oxygen flowing out of cylinder respectively, so that the number of moles of oxygen in gas mixing tank is according to The setting value is automatically controlled, thereby ensuring that the ratio of moles of mixed gas and oxygen is always precisely controllable. At this time, mixed gas in mixing tank is a positive pressure greater than one atmospheric pressure.
The mixed gas with a certain molar ratio of mixed gas to oxygen enters the high-temperature furnace through KaoLu's Proportional Pressure Regulator, and mixer flows through high-temperature furnace and then is discharged through Proportional Pressure Regulator and vacuum pump. When the gas flow and exhaust flow reach a dynamic balance, the precise control of vacuum degree in high temperature furnace can be reached.
In a word, the technology of precise control solution of oxygen partial pressure mentioned above is very mature, and after a large number of tests, the feasibility and reliability of this solution have been verified, and it can fully meet customer's demand for oxygen partial pressure control under high temperature conditions.
If you're interested in KaoLu's Proportional Pressure Regulator, please contact us for more information!