SHARE
MORE DETAIL
Realization of 0.1% Ultra-high Precision PID Controller in Industry and Analysis of Its Key Parameters
1. What is Proportional Pressure Regulator?
In the industrial field, ultra-precise control of process parameters such as temperature, vacuum pressure and flow is often required. The control accuracy in the industrial field is divided into high precision (1%) and ultra-high precision (0.1%), In high-level laboratories and metrology calibrations, control accuracy higher than 0.05% is often required.
For a complete PID control system, the typical control loop is a closed-loop form, as shown in Figure 1.
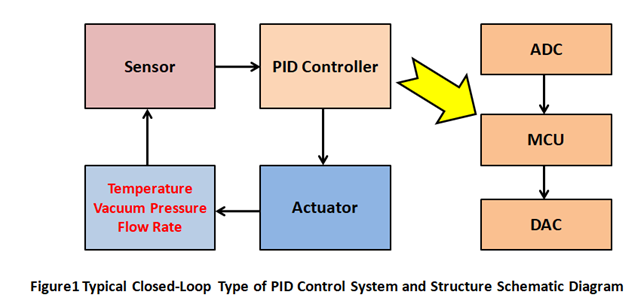
As shown in Figure 1, in the closed-loop PID control system, sensors and actuators are basically external, which can be selected according to different control parameters and accuracy requirements. In industrial applications, the PID controller is basically required to be an independent control instrument, that is, the industrial PID controller basically integrates the analog-to-digital converter ADC, microcontroller MCU, and digital-to-analog converter as shown in Figure 1.
In some higher-precision measurement and control occasions, such as the field of measurement and calibration, in order to improve the accuracy of PID controller, a PID control system with a discrete structure is generally used, that is, the analog-to-digital converter ADC and microcontroller of the PID controller in Figure 1. MCU and digital-to-analog converter are replaced by special instruments with higher precision. For example, analog-to-digital converter ADC is replaced by six-and-a-half (or even seven-and-a-half) digital voltmeter, and microcontroller MCU is replaced by computer or single-chip microcomputer. The digital-to-analog converter is replaced by a six-and-a-half-digit digital source meter. Although the PID control system of such components can effectively improve the control accuracy, the overall cost and volume are greatly improved, and it is not suitable for control in industrial applications.
This article mainly focuses on the integrated PID controller instrument used in industrial applications, and introduces several key technical indicators involved in the realization of 0.1% ultra-high-precision control from the perspective of engineering applications, which will help the ultra-high-precision process control process in industrial applications of implementation and selection of PID controllers.
2. Analysis of key technical indicators in ultra-high precision PID controller
In order to reach the ultra-high-precision control of PID controller better than 0.1%, these three components must be required to meet the corresponding technical indicators and functional requirements to reach high-precision measurement, calculation and control functions respectively.
(1) Measurement accuracy
The measurement precision of PID controller mainly refers to acquisition of external sensor input by the controller, that is, the conversion precision of analog-to-digital converter ADC. The sperm of an ADC is divided into 8, 12, 16 and 24 grades. Therefore, the key technical indicator of PID controller measurement precision is this ADC.
Let's take a DC voltage with a PID signal input range of 0~10V as an example. Figure 2 lists the minimum measurable voltage corresponding to different ADC bits.
According to the minimum measurable voltage capability of different ADC bits shown in Figure 2, the ADC bits required to reach 0.1% measurement accuracy for different sensor signal voltage values can be calculated, as shown in Figure 3. In addition, the selection of ADC digits can be determined according to the accuracy requirements of actual control, and it is extremely acceptable to meet the technical requirements. After all, the higher the AD digits, the higher the accuracy is. However, the more expensive the PID controller instrument, the corresponding acquisition speed slower it is.
(2) Control accuracy
The control accuracy of PID controller mainly refers to the analog output accuracy of controller to the external actuator. The higher the number of digits, the higher the acquisition accuracy is.
(3) Floating-point arithmetic precision
The test accuracy and control accuracy involve the accuracy of hardware part of PID controller. To truly ensure the overall control accuracy of PID controller, it also includes the software calculation accuracy of microprocessor unit MCU used by controller, that is, the so-called floating-point operation accuracy. Take the output percentage in PID controller as an example, as shown in Figure 2, the minimum output percentage for 8-bit floating-point operations is 1%, and the minimum output percentage for 10-bit and 12-bit floating-point operations is 0.1%. To reach a total control accuracy better than 0.1%, it is bound to require the use of 14-bit and 16-bit floating-point operations so that the minimum output percentage is 0.01%. That is to say, the more bits of floating-point operation, the smaller the output percentage is. The finer the control output, the higher the corresponding control precision is.
3. Analysis of pressure control cases
We use a pressure control case to demonstrate the influence of KaoLu’s proportional pressure regulator’s control accuracy on the control effect. In this case, the purpose of our experiment is to precisely control pressure in range of 0~6bar (gauge pressure) to reach a control accuracy of 0.1%. The structure of the entire experimental setup is shown in Figure 4.
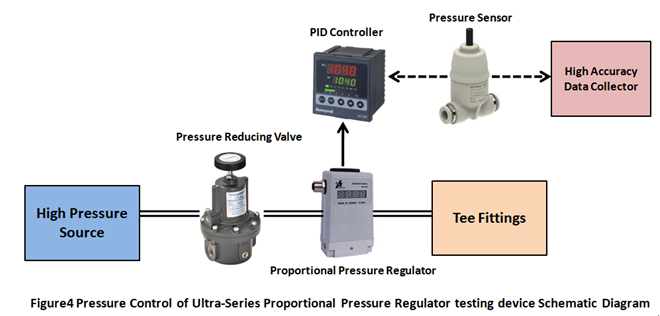
4. Conclusion
Through the above analysis and experimental verification of pressure control case, the industrial integrated PID controller instrument needs to meet the following technical indicators in order to reach a control accuracy of 0.1%:
(1) The external sensor must have an ultra-high precision of more than 0.1%.
(2) The external actuator also needs to have high precision, but it does not necessarily require ultra-high precision of 0.1%.
(3) The number of ADC bits of the PID controller needs to be at least 16 bits, and the best is 24 bits. (4) The floating-point operation of PID controller should ensure that output percentage has an adjustment capability of 0.01% to 0.05%.
(5) The number of DAC bits of PID controller needs to reach at least 14 bits, and the best is 16 bits.
Do you want to know more about KaoLu's Proportional Pressure Regulator? Then visit our website!
1. What is Proportional Pressure Regulator?
In the industrial field, ultra-precise control of process parameters such as temperature, vacuum pressure and flow is often required. The control accuracy in the industrial field is divided into high precision (1%) and ultra-high precision (0.1%), In high-level laboratories and metrology calibrations, control accuracy higher than 0.05% is often required.
For a complete PID control system, the typical control loop is a closed-loop form, as shown in Figure 1.
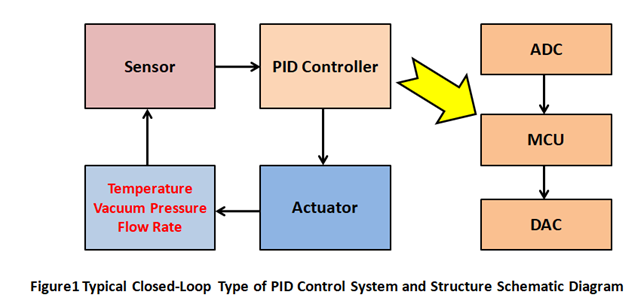
As shown in Figure 1, in the closed-loop PID control system, sensors and actuators are basically external, which can be selected according to different control parameters and accuracy requirements. In industrial applications, the PID controller is basically required to be an independent control instrument, that is, the industrial PID controller basically integrates the analog-to-digital converter ADC, microcontroller MCU, and digital-to-analog converter as shown in Figure 1.
In some higher-precision measurement and control occasions, such as the field of measurement and calibration, in order to improve the accuracy of PID controller, a PID control system with a discrete structure is generally used, that is, the analog-to-digital converter ADC and microcontroller of the PID controller in Figure 1. MCU and digital-to-analog converter are replaced by special instruments with higher precision. For example, analog-to-digital converter ADC is replaced by six-and-a-half (or even seven-and-a-half) digital voltmeter, and microcontroller MCU is replaced by computer or single-chip microcomputer. The digital-to-analog converter is replaced by a six-and-a-half-digit digital source meter. Although the PID control system of such components can effectively improve the control accuracy, the overall cost and volume are greatly improved, and it is not suitable for control in industrial applications.
This article mainly focuses on the integrated PID controller instrument used in industrial applications, and introduces several key technical indicators involved in the realization of 0.1% ultra-high-precision control from the perspective of engineering applications, which will help the ultra-high-precision process control process in industrial applications of implementation and selection of PID controllers.
2. Analysis of key technical indicators in ultra-high precision PID controller
In order to reach the ultra-high-precision control of PID controller better than 0.1%, these three components must be required to meet the corresponding technical indicators and functional requirements to reach high-precision measurement, calculation and control functions respectively.
(1) Measurement accuracy
The measurement precision of PID controller mainly refers to acquisition of external sensor input by the controller, that is, the conversion precision of analog-to-digital converter ADC. The sperm of an ADC is divided into 8, 12, 16 and 24 grades. Therefore, the key technical indicator of PID controller measurement precision is this ADC.
Let's take a DC voltage with a PID signal input range of 0~10V as an example. Figure 2 lists the minimum measurable voltage corresponding to different ADC bits.
ADC (bit) | Minimum Available Voltage (mV) |
8 | 3.906E+01 |
10 | 9.766E+00 |
12 | 2.441E+00 |
14 | 6.104E-01 |
16 | 1.526E-01 |
18 | 3.815E-02 |
20 | 9.537E-03 |
22 | 2.384E-03 |
24 | 5.960E-04 |
Analog Signal (mV) | Voltage Value of 0.1% measured accuracy | Needed ADC (bit) |
10000 | 1.00E+01 | 10 |
5000 | 5.00E+00 | 12 |
1000 | 1.00E+00 | 14 |
500 | 5.00E-01 | 16 |
100 | 1.00E-01 | 18 |
50 | 5.00E-02 | 18 |
10 | 1.00E-02 | 20 |
5 | 5.00E-03 | 22 |
1 | 1.00E-03 | 24 |
According to the minimum measurable voltage capability of different ADC bits shown in Figure 2, the ADC bits required to reach 0.1% measurement accuracy for different sensor signal voltage values can be calculated, as shown in Figure 3. In addition, the selection of ADC digits can be determined according to the accuracy requirements of actual control, and it is extremely acceptable to meet the technical requirements. After all, the higher the AD digits, the higher the accuracy is. However, the more expensive the PID controller instrument, the corresponding acquisition speed slower it is.
(2) Control accuracy
The control accuracy of PID controller mainly refers to the analog output accuracy of controller to the external actuator. The higher the number of digits, the higher the acquisition accuracy is.
(3) Floating-point arithmetic precision
The test accuracy and control accuracy involve the accuracy of hardware part of PID controller. To truly ensure the overall control accuracy of PID controller, it also includes the software calculation accuracy of microprocessor unit MCU used by controller, that is, the so-called floating-point operation accuracy. Take the output percentage in PID controller as an example, as shown in Figure 2, the minimum output percentage for 8-bit floating-point operations is 1%, and the minimum output percentage for 10-bit and 12-bit floating-point operations is 0.1%. To reach a total control accuracy better than 0.1%, it is bound to require the use of 14-bit and 16-bit floating-point operations so that the minimum output percentage is 0.01%. That is to say, the more bits of floating-point operation, the smaller the output percentage is. The finer the control output, the higher the corresponding control precision is.
3. Analysis of pressure control cases
We use a pressure control case to demonstrate the influence of KaoLu’s proportional pressure regulator’s control accuracy on the control effect. In this case, the purpose of our experiment is to precisely control pressure in range of 0~6bar (gauge pressure) to reach a control accuracy of 0.1%. The structure of the entire experimental setup is shown in Figure 4.
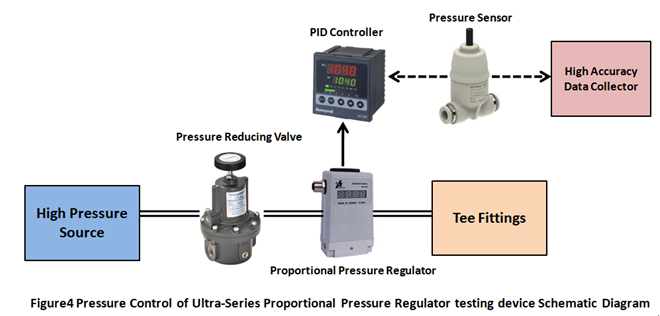
4. Conclusion
Through the above analysis and experimental verification of pressure control case, the industrial integrated PID controller instrument needs to meet the following technical indicators in order to reach a control accuracy of 0.1%:
(1) The external sensor must have an ultra-high precision of more than 0.1%.
(2) The external actuator also needs to have high precision, but it does not necessarily require ultra-high precision of 0.1%.
(3) The number of ADC bits of the PID controller needs to be at least 16 bits, and the best is 24 bits. (4) The floating-point operation of PID controller should ensure that output percentage has an adjustment capability of 0.01% to 0.05%.
(5) The number of DAC bits of PID controller needs to reach at least 14 bits, and the best is 16 bits.
Do you want to know more about KaoLu's Proportional Pressure Regulator? Then visit our website!