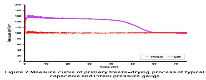
2022.03.11
Application of Electric Needle Valve and Dual-channel Controller in High Precision Pressure Control of Vacuum Freeze Drying
SHARE
MORE DETAIL
Application of Electric Needle Valve and Dual-channel Controller in High Precision Pressure Control of Vacuum Freeze Drying
Abstract: Capacitive pressure gauges have been widely used in vacuum freeze-drying process at present, which makes pressure controller and electric air intake regulating valve matched with capacitive pressure gauges. These two main links affecting the accuracy and repeatability of pressure control, particularly prominent. In order to solve the problem of control accuracy, this article introduces functions, technical indicators and applications of the latest domestic 2-channel 24-bit high-precision PID pressure controller and stepper motor-driven electric needle valve. It has been verified by experiments that the use of electric needle valve and high-precision controller in the upstream control mode can accurately control pressure within ±1%. This controller can also be used to monitor Pirani vacuum gauge during the freeze-drying process to automatically tune to the end point of initial freeze-drying process.
1. Questions
Pressure control is an important process in vacuum freeze-drying process. Its control accuracy severely affects the product quality, especially for freeze-drying of some sensitive products. Therefore, in order to achieve a reliable freeze-drying process with high repeatability, the pressure must be accurately and repeatedly measured and controlled in drying room, which is one of the important indicators for examining the capability of freeze-drying hardware equipment. Due to pressure or vacuum degree during primary drying directly affects the temperature of the product sublimation interface at the same time, accurate and stable pressure control is very important for the primary drying process. However, in actual vacuum freeze-drying process, there are still the following problems in terms of accurate pressure control:
(1) The problem of mismatch pressure controllers: Although the freeze-drying process and equipment are equipped with high-precision capacitive pressure gauges, the accuracy can reach 0.2% to 0.5% of the full scale, but at present, most localized supporting uses PLC for capacitive pressure measurement. For the measurement and control of DC voltage signal, the A/D and D/A conversion accuracy of PLC is obviously insufficient, which seriously affects the pressure measurement and control accuracy. A/D and D/A conversion accuracy must reach at least 16 bit to meet the needs of freeze-drying process.
(2) The mismatch of air intake control valve: For vacuum pressure control in freeze-drying, constant pressure is basically in the order of a few Pa, so upstream air intake control mode is generally used. That is, when the pumping speeds of vacuum pump is constant, increasing air intake flow through electric regulating valve to reduce the pressure, and reduce air intake flow to increase the pressure. However, at present, solenoid valves with large hysteresis are still widely used in China for adjustment, which seriously affects the accuracy and repeatability of pressure control. At present, many low-hysteresis electric control valves driven by stepper motors have been used in the world.
In order to solve the above problems of pressure control in freeze-drying process, this article will introduce functions, technical indicators and applications of the latest localized 2-channel 24-bit high-precision PID pressure controller and electric needle valve. After evaluation and verification of specific applications, the use of electric needle valve and high-precision PID pressure controller in upstream control mode can accurately control the pressure within ±1%. The 2-channel PID controller can also be used for both monitoring and recording of Pirani gauge during freeze-drying.
2. Localized 2-channel 24-bit high-precision PID pressure controller
In order to take full advantage of measurement accuracy of capacitive pressure gauge, the data acquisition and control of controller requires at least 16-bit analog-to-digital and digital-to-analog converters. In recent years, KaoLu have developed the FC series of high-precision 24-bit general-purpose PID controllers, as shown in Figure 1. This series of PID controllers is far more powerful than foreign products, but the price is only one-eighth of foreign products. Its main performance indicators are as follows:
(1) Precision: 24-bit A/D, 16-bit D/A.
(2) Multi-channel: independent 1-channel or 2-channel. 2 channels can reach simultaneous measurement and control of dual sensors.
(3) A variety of output parameters: 47 kinds of input signals (thermocouple, thermal resistance, DC voltage) can reach simultaneous testing, display and control of different parameters.
(4) Multi-function: forward, reverse, forward and reverse two-way control.
(5) PID program control: The improved PID algorithm supports PV differential and differential advance control. It can store 20 groups of PIDs and support 20 program curves (50 segments each).
(6) Communication: Two-wire RS485, standard MODBUS RTU communication protocol.
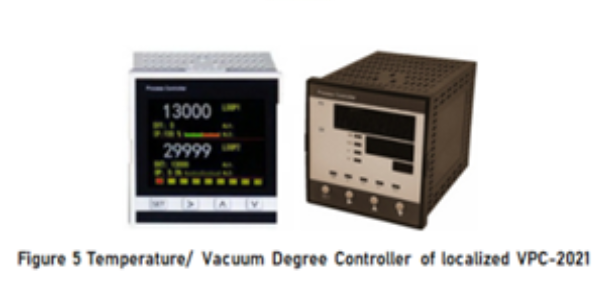
In the judgment of primary freeze-drying end point of freeze-drying, 2-channel controller in FC-20 series can be connected to a capacitive pressure gauge and a Pirani pressure gauge at the same time. The capacitive pressure gauge is used for vacuum pressure control, and the Pirani gauge is used for monitoring the change of water vapor during freeze-drying process, when the difference between two vacuum gauges disappears, the primary freeze-drying process is considered to be over. The typical change curve of the whole process is shown in Figure 2.

3. Localized stepper motor drives electric needle valve
In order to reach high-precision adjustment of air intake valve, we have developed a series of electric needle valves with different flow rates based on needle valve using stepper motors. The magnetic hysteresis is much smaller than solenoid valve. As shown in Figure 3, the price is only one-third of foreign products, and the detailed technical indicators are shown in Figure 4.
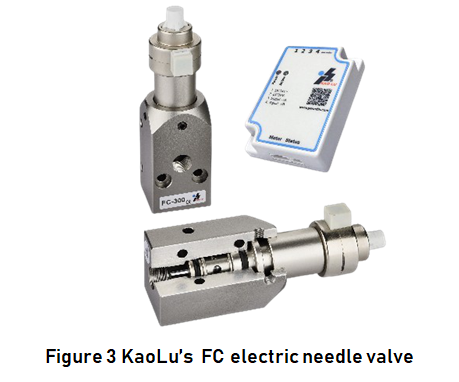
Inert gas and liquidStainless Steel-1 ~ 7bar
(Figure4 Technical indicators of KaoLu’s FC electric needle valve)
4. Assessment test of domestic PID controller and electronic needle valve In the assessment test, a capacitance pressure gauge with a range of 1 Torr was used, and the electronic needle valve was used as the intake valve to conduct the control test in the upstream mode. First turn on the vacuum pump and make it pump at full speed, and then self-tune the PID parameters of the PID controller at about 68Pa. After the self-tuning is completed, 8 set points of 12, 27, 40, 53, 67, 80, 93 and 107 Pa are controlled respectively. The change of vacuum degree during the whole control process is shown in Figure 5.
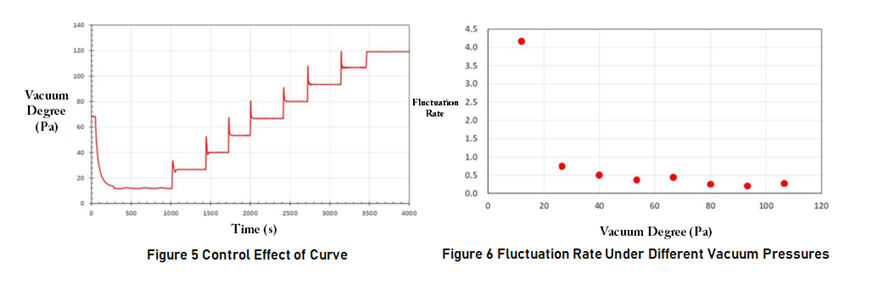
The control effect of curve in Figure 5 is expressed in terms of fluctuation rate, and the fluctuation rate under different vacuum pressures as shown in Figure 6 is obtained. It can be seen from Figure 6 that the fluctuation rate is greater than 1% only when 12Pa control is in the entire pressure range. Obviously, it is not suitable to apply PID parameters obtained by self-tuning at 68Pa to 12Pa pressure control. It also required a separate PID parameter self-tuning.
The introduced electronic needle valve is introduced in https://www.genndih.com/proportional-flow-control-valve.htm
Abstract: Capacitive pressure gauges have been widely used in vacuum freeze-drying process at present, which makes pressure controller and electric air intake regulating valve matched with capacitive pressure gauges. These two main links affecting the accuracy and repeatability of pressure control, particularly prominent. In order to solve the problem of control accuracy, this article introduces functions, technical indicators and applications of the latest domestic 2-channel 24-bit high-precision PID pressure controller and stepper motor-driven electric needle valve. It has been verified by experiments that the use of electric needle valve and high-precision controller in the upstream control mode can accurately control pressure within ±1%. This controller can also be used to monitor Pirani vacuum gauge during the freeze-drying process to automatically tune to the end point of initial freeze-drying process.
1. Questions
Pressure control is an important process in vacuum freeze-drying process. Its control accuracy severely affects the product quality, especially for freeze-drying of some sensitive products. Therefore, in order to achieve a reliable freeze-drying process with high repeatability, the pressure must be accurately and repeatedly measured and controlled in drying room, which is one of the important indicators for examining the capability of freeze-drying hardware equipment. Due to pressure or vacuum degree during primary drying directly affects the temperature of the product sublimation interface at the same time, accurate and stable pressure control is very important for the primary drying process. However, in actual vacuum freeze-drying process, there are still the following problems in terms of accurate pressure control:
(1) The problem of mismatch pressure controllers: Although the freeze-drying process and equipment are equipped with high-precision capacitive pressure gauges, the accuracy can reach 0.2% to 0.5% of the full scale, but at present, most localized supporting uses PLC for capacitive pressure measurement. For the measurement and control of DC voltage signal, the A/D and D/A conversion accuracy of PLC is obviously insufficient, which seriously affects the pressure measurement and control accuracy. A/D and D/A conversion accuracy must reach at least 16 bit to meet the needs of freeze-drying process.
(2) The mismatch of air intake control valve: For vacuum pressure control in freeze-drying, constant pressure is basically in the order of a few Pa, so upstream air intake control mode is generally used. That is, when the pumping speeds of vacuum pump is constant, increasing air intake flow through electric regulating valve to reduce the pressure, and reduce air intake flow to increase the pressure. However, at present, solenoid valves with large hysteresis are still widely used in China for adjustment, which seriously affects the accuracy and repeatability of pressure control. At present, many low-hysteresis electric control valves driven by stepper motors have been used in the world.
In order to solve the above problems of pressure control in freeze-drying process, this article will introduce functions, technical indicators and applications of the latest localized 2-channel 24-bit high-precision PID pressure controller and electric needle valve. After evaluation and verification of specific applications, the use of electric needle valve and high-precision PID pressure controller in upstream control mode can accurately control the pressure within ±1%. The 2-channel PID controller can also be used for both monitoring and recording of Pirani gauge during freeze-drying.
2. Localized 2-channel 24-bit high-precision PID pressure controller
In order to take full advantage of measurement accuracy of capacitive pressure gauge, the data acquisition and control of controller requires at least 16-bit analog-to-digital and digital-to-analog converters. In recent years, KaoLu have developed the FC series of high-precision 24-bit general-purpose PID controllers, as shown in Figure 1. This series of PID controllers is far more powerful than foreign products, but the price is only one-eighth of foreign products. Its main performance indicators are as follows:
(1) Precision: 24-bit A/D, 16-bit D/A.
(2) Multi-channel: independent 1-channel or 2-channel. 2 channels can reach simultaneous measurement and control of dual sensors.
(3) A variety of output parameters: 47 kinds of input signals (thermocouple, thermal resistance, DC voltage) can reach simultaneous testing, display and control of different parameters.
(4) Multi-function: forward, reverse, forward and reverse two-way control.
(5) PID program control: The improved PID algorithm supports PV differential and differential advance control. It can store 20 groups of PIDs and support 20 program curves (50 segments each).
(6) Communication: Two-wire RS485, standard MODBUS RTU communication protocol.
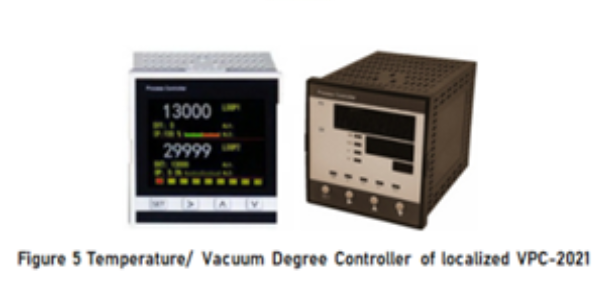
In the judgment of primary freeze-drying end point of freeze-drying, 2-channel controller in FC-20 series can be connected to a capacitive pressure gauge and a Pirani pressure gauge at the same time. The capacitive pressure gauge is used for vacuum pressure control, and the Pirani gauge is used for monitoring the change of water vapor during freeze-drying process, when the difference between two vacuum gauges disappears, the primary freeze-drying process is considered to be over. The typical change curve of the whole process is shown in Figure 2.

3. Localized stepper motor drives electric needle valve
In order to reach high-precision adjustment of air intake valve, we have developed a series of electric needle valves with different flow rates based on needle valve using stepper motors. The magnetic hysteresis is much smaller than solenoid valve. As shown in Figure 3, the price is only one-third of foreign products, and the detailed technical indicators are shown in Figure 4.
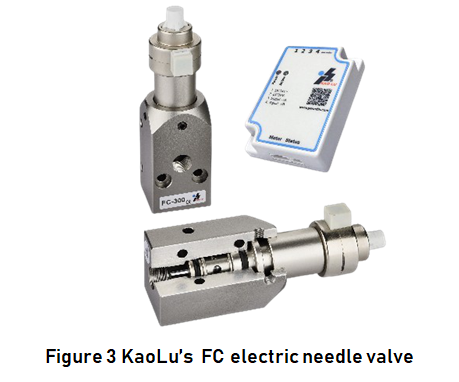
Inert gas and liquidStainless Steel-1 ~ 7bar
Model | FC-20 | FC-120 | FC-300 | FC-1000 |
Valve type | Needle Valve | |||
Spool Drift Diameter | 0.9mm | 2.25mm | 2.75mm | 4.10mm |
Actuator | Bipolar stepper motor control | |||
Response time | 0.8sec(Open to close) | |||
Standard size | G1/8” | G3/8” | ||
Fluid | Inert gas and liquid | |||
Contact Materials | Stainless Steel | |||
Pressure Range | -1 ~ 7bar | -1 ~ 5bar | ||
Maximum Flow | 50L/min @7bar | 240L/min @7bar | 290L/min @7bar | 600L/min @7bar |
Linearity | ±2% | ±0.1 ~ 1% | ±0.2 ~ 5% | ±11% |
Repeatability (Full scale) |
±0.1% | |||
Flow Resolution (Step length) | 0.1L/min | 0.1 ~ 0.2L/min | 0.2 ~ 0.75L/min | 1L/min |
Shift Resolution (Step length) | 12.7um | 25.4um | ||
Operating Temperature Range | 0 ~ 84ºc | |||
Seal | Standard FKM or other choices of seals | |||
Control Signal | DC: 0 ~ 10V (or 4 ~ 20mA) | |||
Power Supply | DC: 24V (12W) |
4. Assessment test of domestic PID controller and electronic needle valve In the assessment test, a capacitance pressure gauge with a range of 1 Torr was used, and the electronic needle valve was used as the intake valve to conduct the control test in the upstream mode. First turn on the vacuum pump and make it pump at full speed, and then self-tune the PID parameters of the PID controller at about 68Pa. After the self-tuning is completed, 8 set points of 12, 27, 40, 53, 67, 80, 93 and 107 Pa are controlled respectively. The change of vacuum degree during the whole control process is shown in Figure 5.
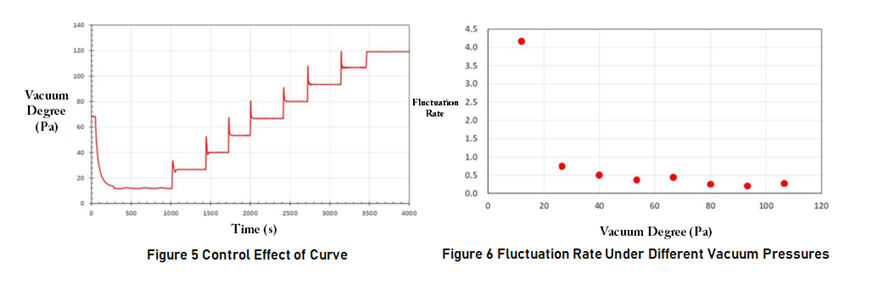
The control effect of curve in Figure 5 is expressed in terms of fluctuation rate, and the fluctuation rate under different vacuum pressures as shown in Figure 6 is obtained. It can be seen from Figure 6 that the fluctuation rate is greater than 1% only when 12Pa control is in the entire pressure range. Obviously, it is not suitable to apply PID parameters obtained by self-tuning at 68Pa to 12Pa pressure control. It also required a separate PID parameter self-tuning.
The introduced electronic needle valve is introduced in https://www.genndih.com/proportional-flow-control-valve.htm