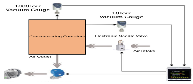
2022.03.10
Precise Control of Temperature and Pressure in Vacuum Concentration Process by New PID Controller and Fast Electric Needle Valve
SHARE
MORE DETAIL
Precise Control of Temperature and Pressure in Vacuum Concentration Process by New PID Controller and Fast Electric Needle Valve
Abstract: In the process of vacuum concentration, concentration temperature and pressure are the core control parameters. This article focuses on a detailed approach to improve poor precision and large fluctuation of pressure control in current concentration instruments and equipment, and proposes a new dual-channel ultra-high-precision multi-function PID controller and high-speed electronic needle valve to reach target temperature in concentration process.
1. Question
The working principle of vacuum concentration is to use vacuum and heating technology to vaporize solvent in a sample quickly and concentrate or a dry sample system under freeze-drying quickly, centrifugal concentration and rotary evaporation. Since different samples have different entropy value to temperature, and there is a strong correlation between pressure and temperature, the ability to accurately control the concentration temperature and pressure during vacuum concentration process has become the most concerned issue for users. In the current commonly used vacuum concentration equipment, following problems still exist:
(1) The accuracy of pressure measurement and control is generally not high, especially in the case of low pressure, which is mainly due to insufficient accuracy of sensors that controllers used. The pressure control accuracy is not high and will have a serious impact on the temperature.
(2) The downstream pressure control method is generally adopted in concentration instruments and equipment, that is, an electronic needle valve is installed between container and vacuum pump to control exhaust rate of the container in real time. This downstream method is suitable for accurate control of higher pressures, but it is difficult to achieve stable and accurate control for low pressures below 10mbar.
(3) At present, the vast majority of electronic needle valves use electric actuators, and the time from closing to fully opening is basically more than 10 seconds. It is difficult to ensure control accuracy and stability of valve adjustment speed with such a serious hysteresis.
(4) Due to the discharge of water and vapor two-phase medium in concentration process, the medium is often corrosive, which puts forward high requirements for corrosion resistance of downstream regulating valve.
2. Solution
2.1 Adopting high-precision pressure sensor
For vacuum concentration process, pressure sensor is to ensure that entire concentration process is controllable. It is strongly recommended to use a high-precision pressure sensor to ensure the measurement of vacuum degree, quantity and control accuracy. The general vacuum control process basically adopts a mechanical vacuum pump, which at low pressure (absolute pressure) does not exceed 0.01mbar, whilst at high pressure it can reach closely to one atmospheric pressure, so it is recommended to use capacitive film gauges for high-precision pressure sensors, as shown in Figure 1. The absolute measurement accuracy can reach ±0.2%. If the pressure range used by the concentration instrument and equipment is relatively wide, it is recommended to use two sensors with different ranges to cover, such as 10 Torr and 1000 Torr. If other types of vacuum sensors are used, it should require a certain precision degree.
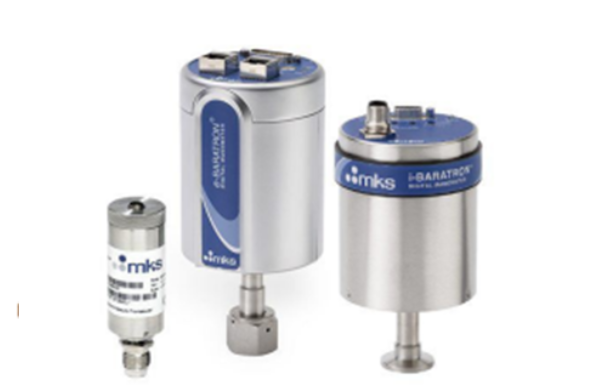
2.2 Adopting high-precision dual-channel PID controller
In vacuum pressure measurement and control, in order to make full use of measurement accuracy of above-mentioned diaphragm pressure gauge, it requires at least 16-bit analog-to-digital and digital-to-analog converters for data acquisition and control of controller. At present, the commonality PID controller with measurement and control accuracy of 24 bits has been launched, as shown in Figure 2. For the process control of vacuum concentration, this series of PID controllers has the following characteristics:
(1) High precision: 24-bit A/D acquisition, 16-bit D/A output.
(2) Multi-channel: independent 1-channel and 2-channel. 2-channel can reach simultaneous measurement and control of temperature and pressure.
(3) Multi-function: 47 kinds of input signals (thermocouple, thermal resistance, DC voltage) can reach simultaneous testing, display and control of different parameters. Also can perform forward and reverse control (two-way control mode).
(4) PID control: The improved PID algorithm can support PV differential and differential advance control. There are 20 groups of group PIDs.
(5) Dual sensor switching: Each channel can support dual sensor switching of high and low temperature and high and low vacuum. Two channels can form a control combination with a total of four sensors connected.
(6) Program control: Up to 20 kinds of concentration programs can be established and stored by themselves. When concentrating, just select and call to start (program control mode).
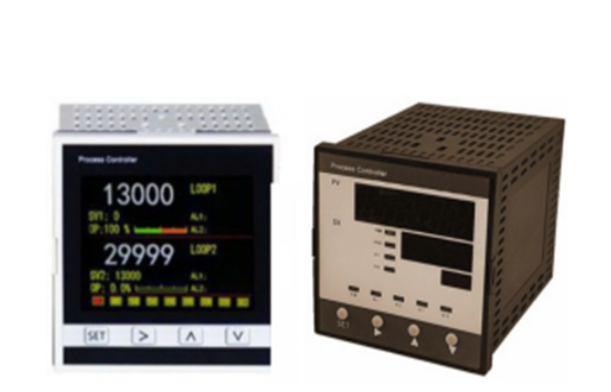
2.3 Increasing upstream air intake control and two-way control mode
The currently common downstream control mode is more suitable for concentration process where pressure is close to atmospheric pressure, but for the low pressure concentration process below 10mbar, it is necessary to introduce the upstream air intake control mode, that is, increase intake channel on concentration container, and control air intake through the electronic needle valve. The air intake flow of air passage can be used to achieve accurate control of pressure.
As shown in Figure 3, local-made electronic needle valves with various flow rates are currently available. Combined with downstream vacuum pump, accurate control of high vacuum (low pressure) can be reached through upstream mode. In order to satisfy the accurate control of low and high pressure full scale at the same time, the dual sensor and two-way control mode as shown in Figure 4 can be used. In the control mode shown in Figure 4, it is necessary to use the forward and reverse control and dual-sensor automatic switching functions of above-mentioned VPC-2021 series dual-channel controller, that is, during different air pressure control processes, the controller automatically switches corresponding range of vacuum gauge, and select the corresponding electronic needle valve and high-speed electric ball valve for control.
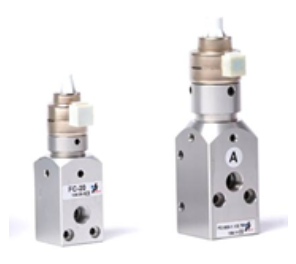
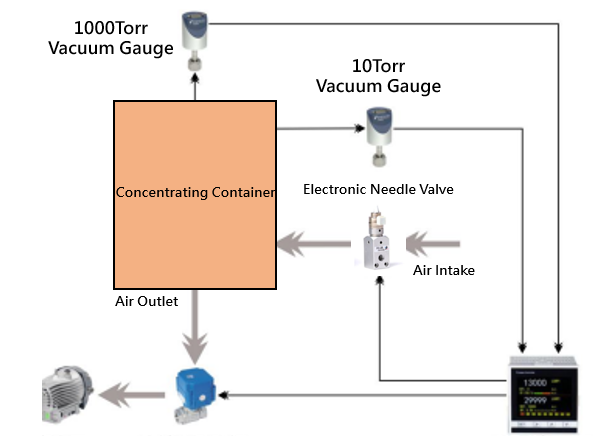
2.4 Adopting high-speed electronic needle valve
The so-called high-speed valve generally means that action time of electronic needle valve from fully closed to opened is less than 1s, which is very important for gas flow and pressure control. Especially for vacuum concentration process, the fast response of air pressure control can ensure the accuracy, safety and increase the evaporation rate of concentration.
At present, localized high-speed electronic needle valves have been developed, as shown in Figure 5. FC series miniaturized high-speed is upgraded products of currently commonly used electric butterfly valve. Combined with VPC2021 series temperature/pressure controller, it can form a fast and accurate vacuum pressure closed-loop control system. Please visit https://www.genndih.com/proportional-flow-control-valve.htm
2.5 Adopting vacuum control regulator
In the current vacuum concentration instruments and equipment, concentration occurs in a hermetic container. The vacuum pump is used to extract air from hermetic container, and air pressure in hermetic container can be kept constant at set value by adjusting air flow rate. This is a typical flow control type constant pressure mode. This flow-controlled pressure regulation method is equivalent to an open-loop control method. There is a self-generated gas inside container, and self-generated gas has no obvious regularity (such as change of linearity), which is harmful to the accurate control of internal pressure of container. For this type of flow-controlled pressure regulation, as shown in Figure 2, an air intake channel is added at the front end of concentration container, and air intake air flow is adjusted to control internal vacuum of container to a stable set value.
For some vacuum concentration instruments and equipment, it is not allowed to add additional air inlet channels, and the pressure-controlled regulator shown in Figure 6 can be used here.
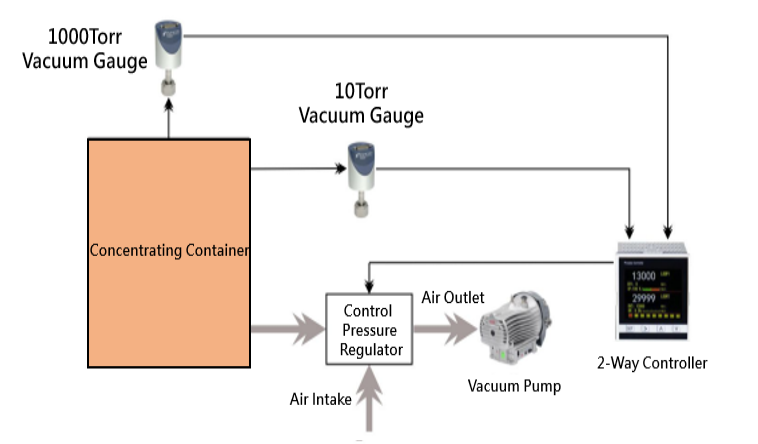
An electronic vacuum regulator is actually an integrated unit with a built-in vacuum pressure sensor, microcontroller, chamber and two electronic needle valves. In vacuum pressure control process, the built-in sensor measures pressure in chamber. If pressure is less than set value, the valve at air intake port will be opened until it is equal to set value. If pressure is greater than set value, the valve at exhaust port will be opened until it is equal to set value. It should ensure that pressure in chamber is always maintained at set value, and regulator cavity is communicated with concentrating container, that is, regulator cavity pressure is always equal to the concentrating container pressure.
It can be seen that pressure-controlled regulator is an independent vacuum pressure regulator with its own air intake valve. As shown in Figure 6, pressure-controlled pressure regulator can also be connected to an external sensor, and set value can be set manually or through a PID controller. For more reference about electronic vacuum regulator, please visit https://www.genndih.com/proportional-pressure-regulator/Electronic-Vacuum-Regulator-1-0bar.html
Abstract: In the process of vacuum concentration, concentration temperature and pressure are the core control parameters. This article focuses on a detailed approach to improve poor precision and large fluctuation of pressure control in current concentration instruments and equipment, and proposes a new dual-channel ultra-high-precision multi-function PID controller and high-speed electronic needle valve to reach target temperature in concentration process.
1. Question
The working principle of vacuum concentration is to use vacuum and heating technology to vaporize solvent in a sample quickly and concentrate or a dry sample system under freeze-drying quickly, centrifugal concentration and rotary evaporation. Since different samples have different entropy value to temperature, and there is a strong correlation between pressure and temperature, the ability to accurately control the concentration temperature and pressure during vacuum concentration process has become the most concerned issue for users. In the current commonly used vacuum concentration equipment, following problems still exist:
(1) The accuracy of pressure measurement and control is generally not high, especially in the case of low pressure, which is mainly due to insufficient accuracy of sensors that controllers used. The pressure control accuracy is not high and will have a serious impact on the temperature.
(2) The downstream pressure control method is generally adopted in concentration instruments and equipment, that is, an electronic needle valve is installed between container and vacuum pump to control exhaust rate of the container in real time. This downstream method is suitable for accurate control of higher pressures, but it is difficult to achieve stable and accurate control for low pressures below 10mbar.
(3) At present, the vast majority of electronic needle valves use electric actuators, and the time from closing to fully opening is basically more than 10 seconds. It is difficult to ensure control accuracy and stability of valve adjustment speed with such a serious hysteresis.
(4) Due to the discharge of water and vapor two-phase medium in concentration process, the medium is often corrosive, which puts forward high requirements for corrosion resistance of downstream regulating valve.
2. Solution
2.1 Adopting high-precision pressure sensor
For vacuum concentration process, pressure sensor is to ensure that entire concentration process is controllable. It is strongly recommended to use a high-precision pressure sensor to ensure the measurement of vacuum degree, quantity and control accuracy. The general vacuum control process basically adopts a mechanical vacuum pump, which at low pressure (absolute pressure) does not exceed 0.01mbar, whilst at high pressure it can reach closely to one atmospheric pressure, so it is recommended to use capacitive film gauges for high-precision pressure sensors, as shown in Figure 1. The absolute measurement accuracy can reach ±0.2%. If the pressure range used by the concentration instrument and equipment is relatively wide, it is recommended to use two sensors with different ranges to cover, such as 10 Torr and 1000 Torr. If other types of vacuum sensors are used, it should require a certain precision degree.
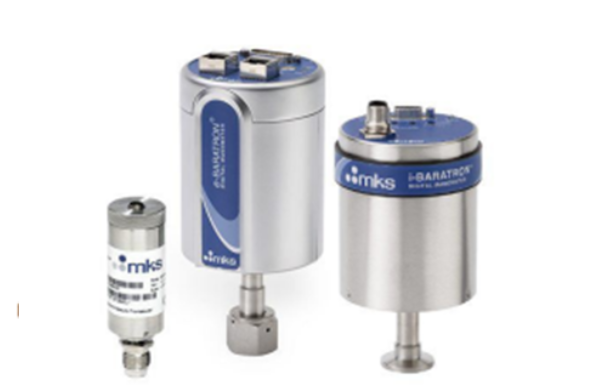
2.2 Adopting high-precision dual-channel PID controller
In vacuum pressure measurement and control, in order to make full use of measurement accuracy of above-mentioned diaphragm pressure gauge, it requires at least 16-bit analog-to-digital and digital-to-analog converters for data acquisition and control of controller. At present, the commonality PID controller with measurement and control accuracy of 24 bits has been launched, as shown in Figure 2. For the process control of vacuum concentration, this series of PID controllers has the following characteristics:
(1) High precision: 24-bit A/D acquisition, 16-bit D/A output.
(2) Multi-channel: independent 1-channel and 2-channel. 2-channel can reach simultaneous measurement and control of temperature and pressure.
(3) Multi-function: 47 kinds of input signals (thermocouple, thermal resistance, DC voltage) can reach simultaneous testing, display and control of different parameters. Also can perform forward and reverse control (two-way control mode).
(4) PID control: The improved PID algorithm can support PV differential and differential advance control. There are 20 groups of group PIDs.
(5) Dual sensor switching: Each channel can support dual sensor switching of high and low temperature and high and low vacuum. Two channels can form a control combination with a total of four sensors connected.
(6) Program control: Up to 20 kinds of concentration programs can be established and stored by themselves. When concentrating, just select and call to start (program control mode).
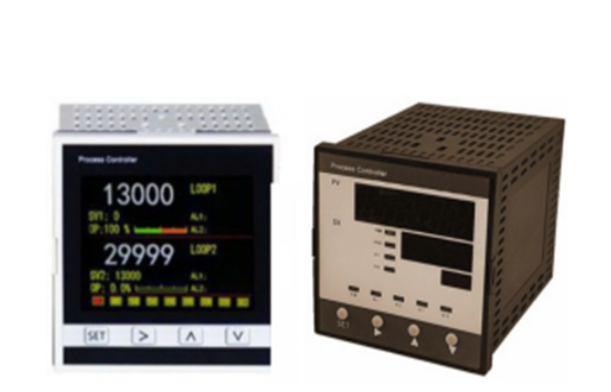
2.3 Increasing upstream air intake control and two-way control mode
The currently common downstream control mode is more suitable for concentration process where pressure is close to atmospheric pressure, but for the low pressure concentration process below 10mbar, it is necessary to introduce the upstream air intake control mode, that is, increase intake channel on concentration container, and control air intake through the electronic needle valve. The air intake flow of air passage can be used to achieve accurate control of pressure.
As shown in Figure 3, local-made electronic needle valves with various flow rates are currently available. Combined with downstream vacuum pump, accurate control of high vacuum (low pressure) can be reached through upstream mode. In order to satisfy the accurate control of low and high pressure full scale at the same time, the dual sensor and two-way control mode as shown in Figure 4 can be used. In the control mode shown in Figure 4, it is necessary to use the forward and reverse control and dual-sensor automatic switching functions of above-mentioned VPC-2021 series dual-channel controller, that is, during different air pressure control processes, the controller automatically switches corresponding range of vacuum gauge, and select the corresponding electronic needle valve and high-speed electric ball valve for control.
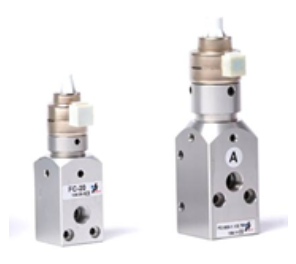
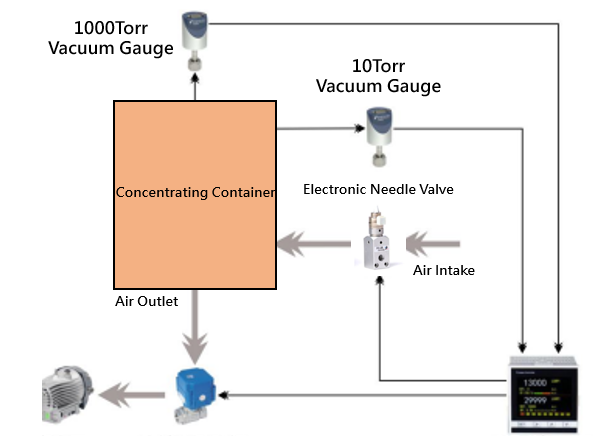
2.4 Adopting high-speed electronic needle valve
The so-called high-speed valve generally means that action time of electronic needle valve from fully closed to opened is less than 1s, which is very important for gas flow and pressure control. Especially for vacuum concentration process, the fast response of air pressure control can ensure the accuracy, safety and increase the evaporation rate of concentration.
At present, localized high-speed electronic needle valves have been developed, as shown in Figure 5. FC series miniaturized high-speed is upgraded products of currently commonly used electric butterfly valve. Combined with VPC2021 series temperature/pressure controller, it can form a fast and accurate vacuum pressure closed-loop control system. Please visit https://www.genndih.com/proportional-flow-control-valve.htm
2.5 Adopting vacuum control regulator
In the current vacuum concentration instruments and equipment, concentration occurs in a hermetic container. The vacuum pump is used to extract air from hermetic container, and air pressure in hermetic container can be kept constant at set value by adjusting air flow rate. This is a typical flow control type constant pressure mode. This flow-controlled pressure regulation method is equivalent to an open-loop control method. There is a self-generated gas inside container, and self-generated gas has no obvious regularity (such as change of linearity), which is harmful to the accurate control of internal pressure of container. For this type of flow-controlled pressure regulation, as shown in Figure 2, an air intake channel is added at the front end of concentration container, and air intake air flow is adjusted to control internal vacuum of container to a stable set value.
For some vacuum concentration instruments and equipment, it is not allowed to add additional air inlet channels, and the pressure-controlled regulator shown in Figure 6 can be used here.
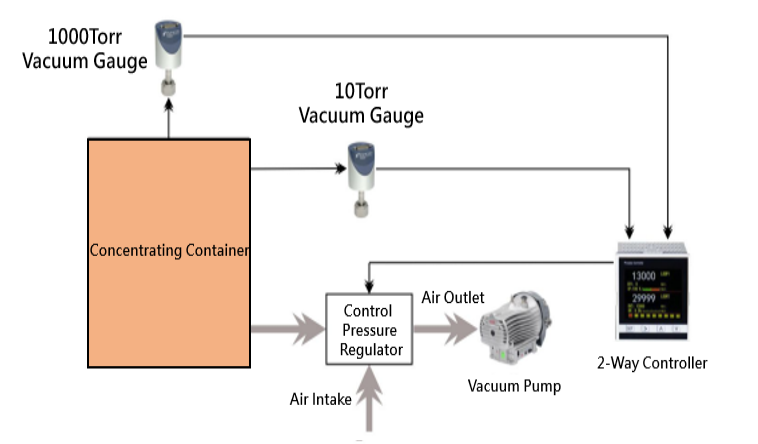
An electronic vacuum regulator is actually an integrated unit with a built-in vacuum pressure sensor, microcontroller, chamber and two electronic needle valves. In vacuum pressure control process, the built-in sensor measures pressure in chamber. If pressure is less than set value, the valve at air intake port will be opened until it is equal to set value. If pressure is greater than set value, the valve at exhaust port will be opened until it is equal to set value. It should ensure that pressure in chamber is always maintained at set value, and regulator cavity is communicated with concentrating container, that is, regulator cavity pressure is always equal to the concentrating container pressure.
It can be seen that pressure-controlled regulator is an independent vacuum pressure regulator with its own air intake valve. As shown in Figure 6, pressure-controlled pressure regulator can also be connected to an external sensor, and set value can be set manually or through a PID controller. For more reference about electronic vacuum regulator, please visit https://www.genndih.com/proportional-pressure-regulator/Electronic-Vacuum-Regulator-1-0bar.html