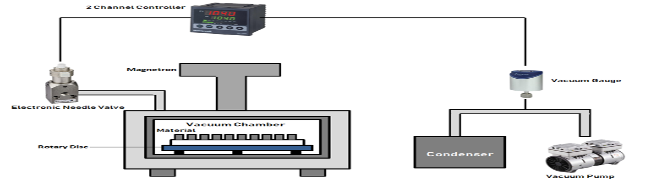
2022.03.25
Precise Control of Vacuum, Temperature and Rotational Speed During Vacuum Microwave Drying (VMD)
SHARE
MORE DETAIL
Precise Control of Vacuum, Temperature and Rotational Speed During Vacuum Microwave Drying (VMD)
Abstract: Focusing on the current local vacuum microwave drying technology research and equipment, the drawbacks are simple control equipment, poor vacuum degree control effect, and low product quality. This article proposes the corresponding solutions and integration of vacuum microwave drying using FC series pneumatic proportional flow control valve. The vacuum degree, temperature and speed controller of the type are introduced, and the corrosion-resistant pneumatic proportional flow control valve driven by stepper motor for gas flow adjustment are introduced, which can precisely control the vacuum microwave drying process.
1. Question
Vacuum microwave drying is a new type of microwave energy application technology that combines microwave heating technology and vacuum technology. In the drying process of materials, the drying temperature range is generally 30~60℃, and vacuum degree range is generally 0.01~95kPa, which has advantages of high drying output, good quality, low processing cost and low energy consumption. In addition, when drying at low temperature and low pressure, the oxygen concentration is low, and the oxidation reaction of dried material is weakened and slowed down, thereby ensuring the flavor, appearance and color of material, and it is easy to dry heat-sensitive materials, especially for traditional Chinese medicine extracts, meat food, chemical raw materials, low-temperature drying of fruits and agricultural products has unique advantages.
Since vacuum microwave drying technology utilizes the principle of lowering the boiling point of water under low pressure, and combines the characteristics of rapid, homogeneous and low energy consumption of microwave heating. Vacuum degree, temperature and rotational speed are the three key control parameters in application of vacuum microwave drying technology. In the current local application of vacuum microwave drying technology, there are generally problems such as rough control equipment, poor vacuum degree control effect, and low product quality, which are mainly reflected in the following aspects:
(1) For different materials, the vacuum degree, temperature and rotation speed required in the drying process are completely different. The variation range of vacuum degree is very wide, such as from 0.01kPa to 95kPa, so it is necessary to have accurate measurement and measurement of vacuum degree in a wide range. For different vacuum degree needs different control methods.
(2) The change of vacuum degree will have a serious impact on evaporation temperature, and temperature change after microwave heating will cause the rapid increase of vacuum degree. Vacuum degree and temperature are a set of variables that affect each other. In order to ensure product quality, the vacuum degree control is required to have a fast response time, so that vacuum degree in drying process is always constant and not affected by temperature changes, and the fluctuation rate of vacuum degree after homeostasis is small. Experiments have proved that the use of pneumatic proportional flow control valve can achieve the desired effect.
(3) In addition to the need to control vacuum degree and temperature (microwave heating power) at the same time, in order to ensure the stability of microwave heating materials, it is also necessary to select and control rotation speed.
(4) Because different materials require different PID control parameters and process parameters, the controller is required to have multi-program and multi-parameter storage functions, which are easy to call at any time during the process, so as to improve automation level of the entire drying process.
2. Vacuum microwave drying control scheme
The vacuum degree, temperature and turntable speed need to be precisely controlled in vacuum microwave drying process. At present, the commonly used control schemes in Taiwan are generally relatively simple. The improved scheme proposed here is shown in Figure 1.
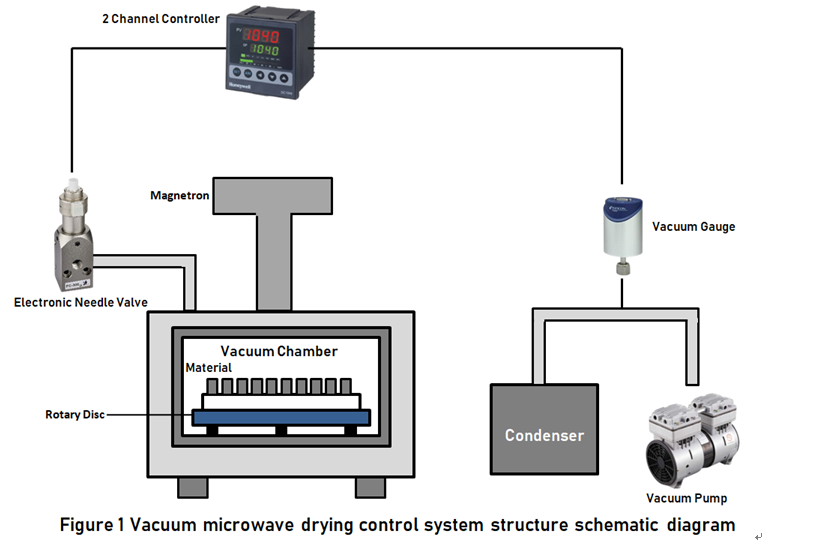
In the vacuum degree control system shown in Figure 1, a method different from the previous vacuum degree control method is adopted, that is, an air intake channel is added to vacuum chamber, and a numerically controlled electric needle valve, or so-called pneumatic flow control valve, and high precision multi-channel controller with fast response speed are used. This program has two outstanding features:
(1) It can reach precise control of vacuum degree in the range of 0.01~95kPa, with a fluctuation rate of less than ±1%. The specific implementation is that when vacuum degree is less than 10torr, the control adopts the upstream mode. When vacuum degree is greater than 10torr, the control adopts the downstream mode. At the same time, fast-response valves and controls ensure that temperature changes have minimal effect on vacuum.
(2) Equipped with 2-channel integrated PID controller, which can reach simultaneous control of vacuum degree, temperature and turntable speed. 2 independent channels are used for the measurement, control and display of vacuum and temperature, and the alarm output channel can be used to control the speed of turntable or start-stop of rotating motor.
3. 24-bit high-precision multi-functional controller
In order to reach the precise control of vacuum degree, temperature and rotation speed in vacuum microwave drying, KaoLu have developed FC series 24-bit high-precision programmable PID universal controller, as shown in Figure 2. This series of PID controllers are very useful and cost-effective.
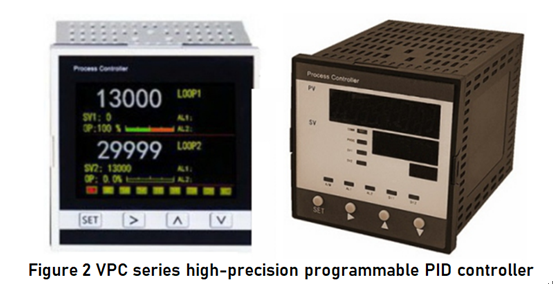
The main performance indicators of VPC series controllers are as follows:
(1) Precision: 24-bit A/D, 16-bit D/A.
(2) Maximum sampling speed: 50ms.
(3) Various input parameters: 47 input signals (thermocouple, thermal resistance, DC voltage) can be connected to various temperature and vacuum sensors for measurement, display and control.
(4) Various output forms: 16BIT analog signal, 2A (250V AC) relay, 22V/20mA solid state relay, 3A/250VAC SCR.
(5) Multi-channel: independent 1-channel or 2-channel output. 2 channels can reach simultaneous measurement and control of temperature and vacuum degree, and the alarm output channel can be used to control the start-stop of rotating motor.
(6) Multi-function: forward, reverse, forward and reverse bi-directional control, heating/cooling control.
(7) PID program control: The improved PID algorithm supports PV differential and differential advance control. It can store 20 groups of PID and support 20 program curves (50 segments each).
(8) Communication: Two-wire RS485, standard MODBUS RTU communication protocol.
(9) Display mode: digital hall and IPS TFT true color LCD.
(10) Software: The operation of controller and the data acquisition and storage can be reached through the software computer.
(11) Dimensions: 96×96×87mm (hole size 92×92mm).
4. Stepper motor drives corrosion-resistant high-speed needle valve
In order to reach high-precision adjustment in the process of vacuum degree control, KaoLu have developed a series of pneumatic proportional flow control valves with different flow rates based on the needle valve using stepper motors, as shown in Figure 2. The magnetic hysteresis of this series is much smaller than solenoid valves, and has a high-speed response within 1 second. In particular, the use of FKM sealing technology enables the valve to have superior corrosion resistance. The detailed technical indicators are shown in Figure 4 shown.
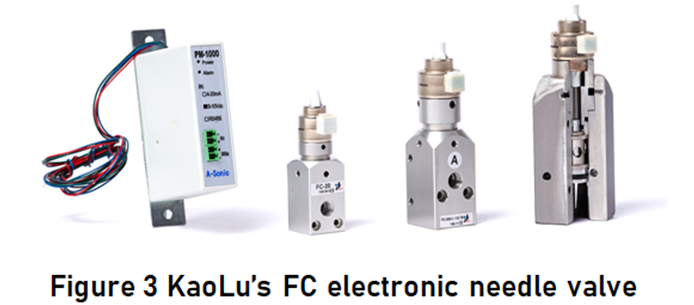
(Figure 4 Technical indicators of KaoLu’s FC electronic needle valve)
For further information, please visit https://www.genndih.com/proportional-flow-control-valve/mid-flow-proportional-valve-0-130L-min.html
FC pneumatic proportional flow control valve is equipped with a stepper motor drive circuit module, which provides the required power supply and control signal for FC pneumatic proportional flow control valve, and converts the DC signal into step control of bipolar stepper motor, and can also provide RS485 direct control of serial communication. Its specifications and dimensions are shown in Figure 5.
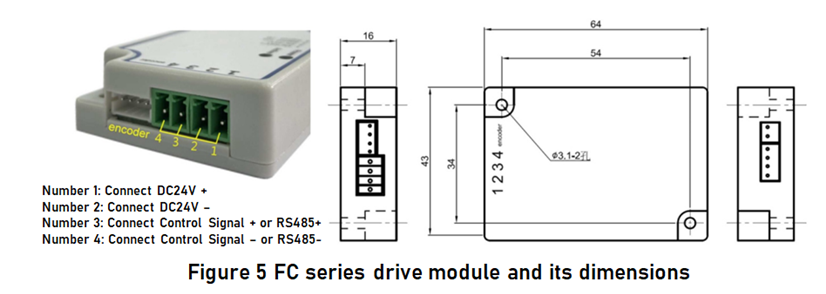
When using pneumatic proportional flow control valve in vacuum microwave drying, open-loop control method can also be used to install needle valve at the front end of vacuum pump instead of electric ball valve, and the vacuum degree can be controlled by adjusting pumping flow, but the stability of this open-loop control method is poor. It is difficult to reach higher stability requirements. Therefore, it is generally recommended to use closed-loop control method shown in Figure 1, that is, to add an air intake control valve to vacuum chamber, and to achieve precise control of vacuum degree by adjusting air intake flow and exhaust flow at the same time.
Abstract: Focusing on the current local vacuum microwave drying technology research and equipment, the drawbacks are simple control equipment, poor vacuum degree control effect, and low product quality. This article proposes the corresponding solutions and integration of vacuum microwave drying using FC series pneumatic proportional flow control valve. The vacuum degree, temperature and speed controller of the type are introduced, and the corrosion-resistant pneumatic proportional flow control valve driven by stepper motor for gas flow adjustment are introduced, which can precisely control the vacuum microwave drying process.
1. Question
Vacuum microwave drying is a new type of microwave energy application technology that combines microwave heating technology and vacuum technology. In the drying process of materials, the drying temperature range is generally 30~60℃, and vacuum degree range is generally 0.01~95kPa, which has advantages of high drying output, good quality, low processing cost and low energy consumption. In addition, when drying at low temperature and low pressure, the oxygen concentration is low, and the oxidation reaction of dried material is weakened and slowed down, thereby ensuring the flavor, appearance and color of material, and it is easy to dry heat-sensitive materials, especially for traditional Chinese medicine extracts, meat food, chemical raw materials, low-temperature drying of fruits and agricultural products has unique advantages.
Since vacuum microwave drying technology utilizes the principle of lowering the boiling point of water under low pressure, and combines the characteristics of rapid, homogeneous and low energy consumption of microwave heating. Vacuum degree, temperature and rotational speed are the three key control parameters in application of vacuum microwave drying technology. In the current local application of vacuum microwave drying technology, there are generally problems such as rough control equipment, poor vacuum degree control effect, and low product quality, which are mainly reflected in the following aspects:
(1) For different materials, the vacuum degree, temperature and rotation speed required in the drying process are completely different. The variation range of vacuum degree is very wide, such as from 0.01kPa to 95kPa, so it is necessary to have accurate measurement and measurement of vacuum degree in a wide range. For different vacuum degree needs different control methods.
(2) The change of vacuum degree will have a serious impact on evaporation temperature, and temperature change after microwave heating will cause the rapid increase of vacuum degree. Vacuum degree and temperature are a set of variables that affect each other. In order to ensure product quality, the vacuum degree control is required to have a fast response time, so that vacuum degree in drying process is always constant and not affected by temperature changes, and the fluctuation rate of vacuum degree after homeostasis is small. Experiments have proved that the use of pneumatic proportional flow control valve can achieve the desired effect.
(3) In addition to the need to control vacuum degree and temperature (microwave heating power) at the same time, in order to ensure the stability of microwave heating materials, it is also necessary to select and control rotation speed.
(4) Because different materials require different PID control parameters and process parameters, the controller is required to have multi-program and multi-parameter storage functions, which are easy to call at any time during the process, so as to improve automation level of the entire drying process.
2. Vacuum microwave drying control scheme
The vacuum degree, temperature and turntable speed need to be precisely controlled in vacuum microwave drying process. At present, the commonly used control schemes in Taiwan are generally relatively simple. The improved scheme proposed here is shown in Figure 1.
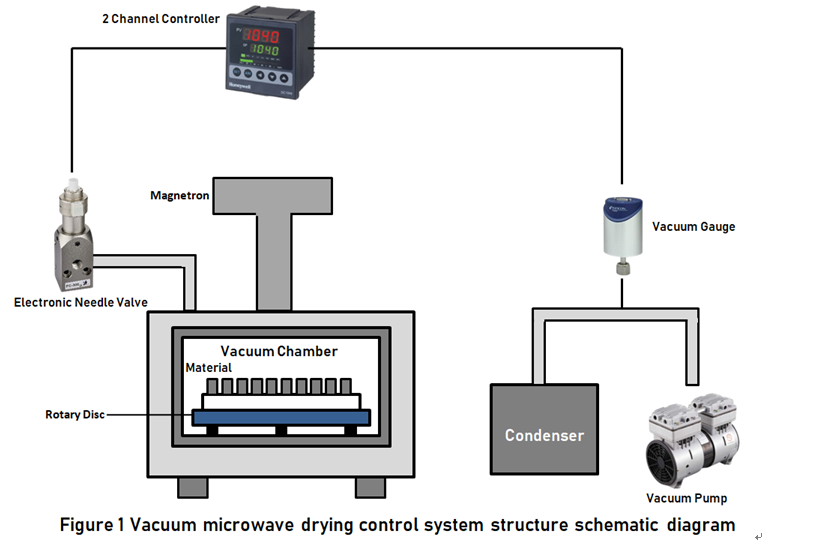
In the vacuum degree control system shown in Figure 1, a method different from the previous vacuum degree control method is adopted, that is, an air intake channel is added to vacuum chamber, and a numerically controlled electric needle valve, or so-called pneumatic flow control valve, and high precision multi-channel controller with fast response speed are used. This program has two outstanding features:
(1) It can reach precise control of vacuum degree in the range of 0.01~95kPa, with a fluctuation rate of less than ±1%. The specific implementation is that when vacuum degree is less than 10torr, the control adopts the upstream mode. When vacuum degree is greater than 10torr, the control adopts the downstream mode. At the same time, fast-response valves and controls ensure that temperature changes have minimal effect on vacuum.
(2) Equipped with 2-channel integrated PID controller, which can reach simultaneous control of vacuum degree, temperature and turntable speed. 2 independent channels are used for the measurement, control and display of vacuum and temperature, and the alarm output channel can be used to control the speed of turntable or start-stop of rotating motor.
3. 24-bit high-precision multi-functional controller
In order to reach the precise control of vacuum degree, temperature and rotation speed in vacuum microwave drying, KaoLu have developed FC series 24-bit high-precision programmable PID universal controller, as shown in Figure 2. This series of PID controllers are very useful and cost-effective.
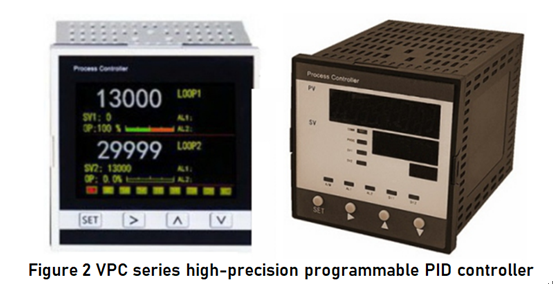
The main performance indicators of VPC series controllers are as follows:
(1) Precision: 24-bit A/D, 16-bit D/A.
(2) Maximum sampling speed: 50ms.
(3) Various input parameters: 47 input signals (thermocouple, thermal resistance, DC voltage) can be connected to various temperature and vacuum sensors for measurement, display and control.
(4) Various output forms: 16BIT analog signal, 2A (250V AC) relay, 22V/20mA solid state relay, 3A/250VAC SCR.
(5) Multi-channel: independent 1-channel or 2-channel output. 2 channels can reach simultaneous measurement and control of temperature and vacuum degree, and the alarm output channel can be used to control the start-stop of rotating motor.
(6) Multi-function: forward, reverse, forward and reverse bi-directional control, heating/cooling control.
(7) PID program control: The improved PID algorithm supports PV differential and differential advance control. It can store 20 groups of PID and support 20 program curves (50 segments each).
(8) Communication: Two-wire RS485, standard MODBUS RTU communication protocol.
(9) Display mode: digital hall and IPS TFT true color LCD.
(10) Software: The operation of controller and the data acquisition and storage can be reached through the software computer.
(11) Dimensions: 96×96×87mm (hole size 92×92mm).
4. Stepper motor drives corrosion-resistant high-speed needle valve
In order to reach high-precision adjustment in the process of vacuum degree control, KaoLu have developed a series of pneumatic proportional flow control valves with different flow rates based on the needle valve using stepper motors, as shown in Figure 2. The magnetic hysteresis of this series is much smaller than solenoid valves, and has a high-speed response within 1 second. In particular, the use of FKM sealing technology enables the valve to have superior corrosion resistance. The detailed technical indicators are shown in Figure 4 shown.
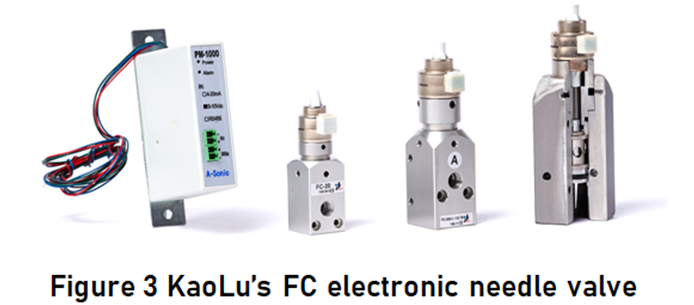
Model | FC-20 | FC-120 | FC-300 | FC-1000 |
Valve type | Needle Valve | |||
Spool Drift Diameter | 0.9mm | 2.25mm | 2.75mm | 4.10mm |
Actuator | Bipolar stepper motor control | |||
Response time | 0.8sec(Open to close) | |||
Standard size | G1/8” | G3/8” | ||
Fluid | Inert gas and liquid | |||
Contact Materials | Stainless Steel | |||
Pressure Range | -1 ~ 7bar | -1 ~ 5bar | ||
Maximum Flow | 50L/min @7bar | 240L/min @7bar | 290L/min @7bar | 600L/min @7bar |
Linearity | ±2% | ±0.1 ~ 1% | ±0.2 ~ 5% | ±11% |
Repeatability (Full scale) |
±0.1% | |||
Flow Resolution (Step length) | 0.1L/min | 0.1 ~ 0.2L/min | 0.2 ~ 0.75L/min | 1L/min |
Shift Resolution (Step length) | 12.7um | 25.4um | ||
Operating Temperature Range | 0 ~ 84°c | |||
Seal | Standard FKM or other choices of seals | |||
Control Signal | DC: 0 ~ 10V (or 4 ~ 20mA) | |||
Power Supply | DC: 24V (12W) |
For further information, please visit https://www.genndih.com/proportional-flow-control-valve/mid-flow-proportional-valve-0-130L-min.html
FC pneumatic proportional flow control valve is equipped with a stepper motor drive circuit module, which provides the required power supply and control signal for FC pneumatic proportional flow control valve, and converts the DC signal into step control of bipolar stepper motor, and can also provide RS485 direct control of serial communication. Its specifications and dimensions are shown in Figure 5.
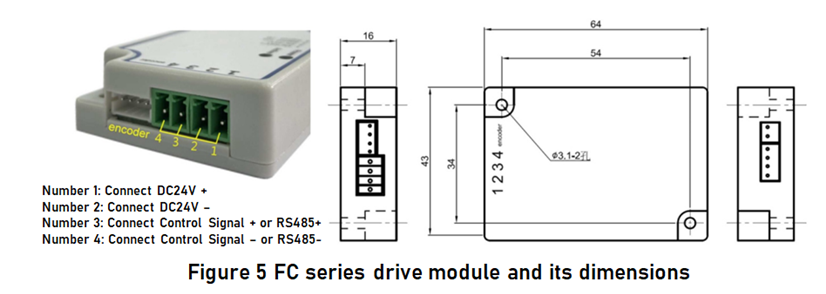
When using pneumatic proportional flow control valve in vacuum microwave drying, open-loop control method can also be used to install needle valve at the front end of vacuum pump instead of electric ball valve, and the vacuum degree can be controlled by adjusting pumping flow, but the stability of this open-loop control method is poor. It is difficult to reach higher stability requirements. Therefore, it is generally recommended to use closed-loop control method shown in Figure 1, that is, to add an air intake control valve to vacuum chamber, and to achieve precise control of vacuum degree by adjusting air intake flow and exhaust flow at the same time.