SHARE
MORE DETAIL
1. Introduction of KaoLu's Proportional Pressure Regulator
In the biomedicine and semiconductor industries, there are often high requirements for micro-positive pressure, requiring pressure control to reach an ultra-high precision of 0.1% under a micro-positive pressure slightly higher than a standard atmospheric pressure. At present, there are two problems in the micro positive pressure ultra-high precision control technology:
- Many micro-positive pressure controls directly use electric proportional valves, but limited by the built-in pressure sensor and controller precision. Electric proportional valves cannot meet the ultra-high precision pressure control requirements at all.
- In the field of measurement and calibration testing, in order to improve the precision of pressure control, an ultra-high-precision split structure is often used, that is, an independent pressure sensor, data collector, data controller and microcomputer processor are used to form a closed-loop control loop. Although this method can achieve very high accuracy (such as 0.01%), the overall cost is high and it is not suitable for industrial and instrumentation industries.
For this reason, this article introduces KaoLu's Proportional Pressure regulator. By connecting an ultra-high-precision pressure sensor and PID controller, while taking advantage of KaoLu's Proportional Pressure Regulator, the pressure control accuracy is greatly improved, and overall cost is kept at a low level.
2. How to solve the problem?
As shown in Figure 1, the specific solution is based on KaoLu's Proportional Pressure Regulator. A closed-loop PID control loop is formed by connecting a higher-precision pressure sensor and a PID controller externally to reach micro-positive pressure control with ultra-high precision of 0.1%.
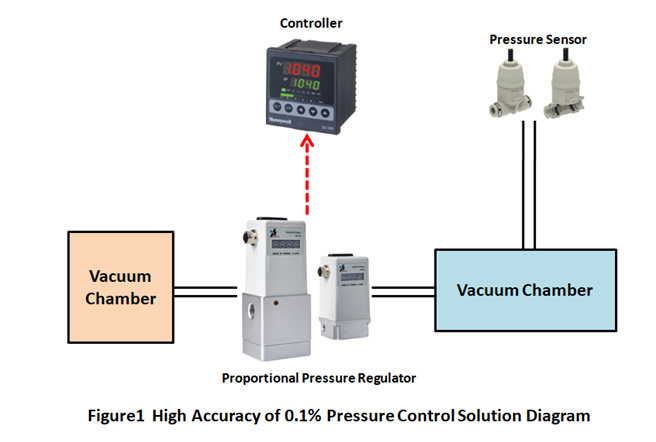
The characteristic of this solution is that KaoLu's Proportional Pressure Regulator is used as actuator, and ultra-high-precision control requires an external higher-precision pressure sensor and PID controller.
According to our previous assessment tests and control process data analysis, we have come to the conclusion that to reach a control accuracy of 0.1% for industrial integrated PID controller instruments, the following technical indicators need to be met:
- The external sensor must have an ultra-high precision of more than 0.1%.
- The external actuator (proportional pressure regulator) also needs to have high precision, but it does not necessarily require ultra-high precision of 0.1%. The overall accuracy can reach 1%, which is mainly due to the rate indicator of proportional pressure regulator used.
- The number of ADC bits of PID controller needs to be at least 16 bits, preferably 24 bits.
- The floating-point operation of PID controller must ensure that output percentage has an adjustment capability of 0.01%~0.05%.
- The number of DAC bits of PID controller needs to reach at least 14 bits, and the best is 16 bits.
From the above requirements on technical indicators and test results, it can be seen that in order to reach ultra-high precision pressure control, on the premise that external pressure sensor, proportional pressure regulator and PID controller ADC meet the accuracy requirements. The DAC control output of PID controller and Floating point operations must also have sufficient precision, and the minimum percentage of PID controller output must be capable of 0.01%.
Based on the above analysis, the hardware configuration in solution mainly includes the following parts:
- Pressure sensor: the accuracy is 0.05%, the range is absolute pressure 0.1~1MPa, and the corresponding voltage output is 0~10V.
- KaoLu's Proportional Pressure Regulator: The maximum input gas pressure is 300kPa, the set pressure control range is 0~100kPa, and the external analog quantity is to evaluate the effectiveness of above solution.
According to the above configuration, an evaluation test device is built, as shown in Figure 2. The input signal is 0~10DVC, the linearity is less than ±0.3%FS, the repeatability is less than ±0.2%FS, and the hysteresis is less than 0.3%FS. - PID controller: ADC is 24 bits, DAC is 16 bits, ADC range is 0~10V, DAC range is 0~10V, and the minimum output percentage of analog control is 0.01%.
3. Examine KaoLu's Proportional Pressure Regulator
In order to assess the effectiveness of above solutions, an assessment test device was built according to the above configuration, as shown in Figure 2.
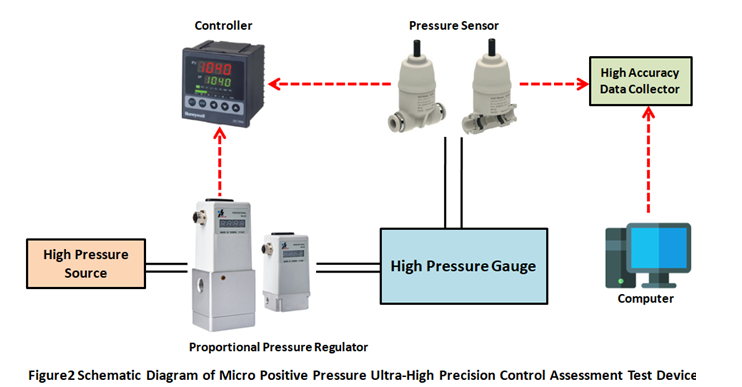
In order to effectively collect, monitor and store the assessment test data, the following content is added to the assessment test device in Figure 2:
- Multi-channel data collector
- High-pressure pipe fittings: It is used as pressure vessels, and connected with pressure sensors and proportional pressure regulator.
- Computer: It is used to communicate with PID controller and data collector. It can also install and run corresponding software programs to control, data acquisition, curve display and data storage of PID controller and data collector.
4. Conclusion
Through the above solution and assessment test results, it is proved that this solution is fully capable of reaching 0.1% ultra-high precision pressure control for micro positive pressure. The specific conclusions are as follows:
- The external ultra-high-precision pressure sensor and PID controller can effectively improve the pressure control accuracy of KaoLu's Proportional Pressure Regulator, and can reach 0.1% ultra-high-precision pressure control.
- In the ultra-high-precision 0.1% pressure control process, the measurement accuracy, control accuracy and floating-point operation of PID controller are the key technical indicators that determine the overall control accuracy. The solution described in this article uses 24-bit ADC, 16-bit DAC and high-precision floating-point operation with an output percentage of 0.01%, which proves that it can fully meet the needs of ultra-high-precision control.
- Through the solution and test verification in this article, it is proved that KaoLu's Proportional Pressure regulator can reach ultra-high-precision control at a lower cost.
- The solution in this article has great flexibility, pressure sensors and KaoLu's Proportional Pressure regulator with different ranges can be selected. Ultra-high-precision control in different pressure ranges can be reached through a general-purpose ultra-high-precision PID controller.
If you're interested in our Proportional Pressure Regulator, please visit our website!